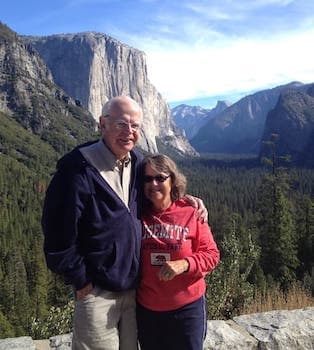
Curated with aloha by
Ted Mooney, P.E. RET
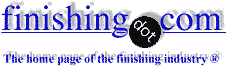
The authoritative public forum
for Metal Finishing 1989-2025
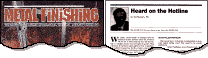
-----
Nickel sulfamate plating and then some chromium plating on top of that. Defects causes?
I am currently involved with a SIX Sigma project to resolve a long standing problem regarding defects in Nickel sulfamate plating and Chromium plating plating process applied across two different parent materials, (a CARBON STEEL AND INCONEL). We are experiencing blisters, oversize plating thicknesses and voids. I am looking for measurements (Clues) to to help identify some possible causes. Can anyone help?
Ty TrykowskiStudent of the Art of plating - Euclid , Ohio
February 6, 2008
I greatly admire the ideas and the discipline of the six-sigma approach, Ty. But I reject the idea that significant plating problems can be solved in formulaic fashion without significant plating knowledge and experience. Some quick clues are: 90 percent of plating problems are cleaning problems; Inconel will require an activating pretreatment step; Faraday's Law determines plating thickness; the plating step per se doesn't often generate voids; finally, and most importantly, the process vendors have technical service people who can come out and quickly get your efforts steered at the right point in the process. Good luck!
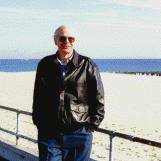
Ted Mooney, P.E.
Striving to live Aloha
finishing.com - Pine Beach, New Jersey
February 6, 2008
Ted, let me first thank you for your response. This project has the vendor plating personnel participating on the team. I do have an appreciation for the art of plating and many feel this is a hit/miss endeavor. You mentioned an "activating pretreatment step" may I inquire as to what is meant by this. I do apologize for my ignorance but I am deeply trying to help. Through my brief introduction I understand that, bath chemistry, amperage, bath temperature, part temperature, part cleanliness, wetting all play a factor in the final product. Blisters puzzle me, if I can plate, nickel strike, nickel plate with no visual blisters and then chromium plate with no blisters visual appearing immediately after plating why would the blisters appear hours after plating. At least this is what I am being told. Do you have any input?
Ty Trykowski- Euclid, Ohio
February 11, 2008
You are getting blisters because you lack a metallurgical bond between the plating and the substrate. That is either because: the parts are not truly clean; or the Inconel is not properly activated and you are trying to electroplate onto a tarnish instead of onto a metal; or during the electroplating process you are encountering breaks in applied current that is allowing the nickel to passivate. Ignore the time delay before the blistering is evident; exactly why it's taking the plating some time to creep into a blistered attitude is not important.
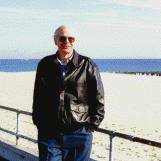
Ted Mooney, P.E.
Striving to live Aloha
finishing.com - Pine Beach, New Jersey
February 11, 2008
First of two simultaneous responses -- February 11, 2008
Over cleaning and/or over etching of high carbon steel can lead to blisters between the metal and the 1st plate layer.
High nickel steels are difficult to properly activate, so a poor bond.
The blister is an accumulation of gasses under a weak bond spot(s) in the plate. This is one reason that you bake the part immediately after plate.
1st, you need to break some blisters and decide where the delamination is occurring-base metal to 1st plate or 1st plate to 2nd plate.
An addition to what Ted said- As long as there is unverifiable cleanliness and activation of the parts along with the huge human factor, anyone that thinks that you can successfully apply 6 sigma to small lots of plating is seriously deluding themselves.
In the old days, we would tell you to check out their cigarettes.
- Navarre, Florida
Second of two simultaneous responses --
Thank you Ted, your information has pointed me and the team in a good direction. I do appreciate your input. I will keep you posted as to our progress and the items we choose to measure in regards to this plating application. Pondering the thought of cleanliness how might you suggest we measure or ensure cleanliness throughout the plating application? Thanks Again Ty
Ty Trykowski- Euclid, Ohio
February 12, 2008
You're very welcome. The simplest and most obvious cleanliness test is the "water break" test. You can find a lot about that without even wandering off this site. But don't overdo it; there is a thread on line here (letter 31926) where people who didn't know better tried to make this qualitative test a quantitative test.
Every employee in the plating shop knew the waterbreak test on their first week on the job -- are you sure the communication lines are open? :-)
There are more advanced water break tests using wetting solutions of various surface tension, and the spec numbers for ASTM cleanliness test specs are described in the referenced letter. Good luck.
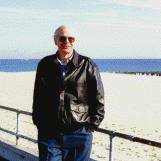
Ted Mooney, P.E.
Striving to live Aloha
finishing.com - Pine Beach, New Jersey
February 12, 2008
Ted, thanks for the response. As far as the communications lines yes they are open maybe a little garbled at times but open. The plating supplier is very familiar with the water break test and has mentioned it several times as part of the process. However, the length of time was never directly mentioned in association with the test. Reading the attached link that you provided it seems the experts disagree as to the time frame ranges ( some place between 2 seconds and 1 minute). The component we are plating I guess has a fairly large area to be plated. We are plating an area approximately
6 Á" in diameter by some 24 inches long. The water break test is applied with the work piece hanging Vertical to the ground. How long would you suggest the time be? Ty
Dear Mr. Watts, thank you for the response. This project is termed Six Sigma project but we are attempting to solve a long standing plating pain utilizing the DMAIC problem solving method. Statistical use and data are strictly governed from the perspective of solving plating defects. The expertise of the team (the platers) will ultimately solve the problem. Hopefully, six sigma (DMAIC) can point us in a direction that proves to individuals where the problems lye. Again, thank you, for your response and your input. As far as the cigarettes; if that could help solve the problem it would be worth trying.
Ted, I acquired and read the ASTM Spec F22 -02 (2007). This specification has prompted several other questions. So please be patient with me. In the specification section 8 Reagents and Materials item 8.2 Purity of Water it reads Deionized or distilled water is preferred. From my experience with electrical discharge machining the deionization of water can be held at different levels. So in the context of Plating what level of deionization should the water be maintained? The next question is in regards to the statement
" The water used must be free of Hydrophobic and hydrophilic substances. " So how do we measure that the deionized water is free from this substances? Thank you for your help. Ty
- Euclid, Ohio
February 18, 2008
The point I was making was that the waterbreak test is qualitative, not quantitative. In fact, it's not so much a test as a guideline. An experienced operator takes a quick look and says it's clean or it's not; and he looks right after the cleaner tank knowing this isn't fully valid, and looks again after its rinse, knowing that isn't valid either, and looks again after the acid rinse. If you want to say 10 seconds that's fine. And if you find a spec that says 20 or 30 seconds, I personally think it's silly because no one lets the parts drain that long (the parts might dry or the plating go passive, as well as halting production) but compliance with specs is more important than opinions. Your other questions about measuring the hydrophobic and hydrophillic substances are about a spec that, in my opinion again, sort of tries to pervert a guideline into a requirement. Obviously, once the part has been in the cleaning tank it's impossible for it to be totally free of hydrophillic substances, so I would interpret that statement loosely that the part is well rinsed and the rinsewater isn't deliberately laced with surfactants.
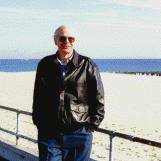
Ted Mooney, P.E.
Striving to live Aloha
finishing.com - Pine Beach, New Jersey
February 21, 2008
March 16, 2008
Hi , the possible cause for the blistering you are having may be due to the nickel going passive before you reach the chrome bath - also try plating at a lower current in the chrome for a short period
, then raise the power to what it should be .
The voids in the plating must only due to poor cleaning , or poor rinsing - especially if there is a chance of solution being trapped by any masking aids - lead tape , wax etc...
- Essex, UK
Q, A, or Comment on THIS thread -or- Start a NEW Thread