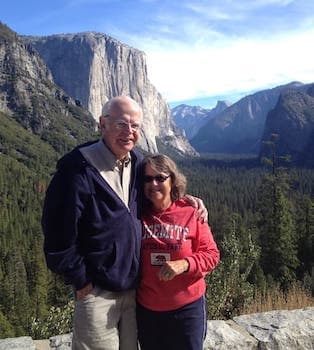
Curated with aloha by
Ted Mooney, P.E. RET
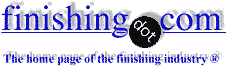
The authoritative public forum
for Metal Finishing 1989-2025
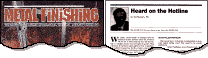
-----
Etching/Pitting problem with brass parts in bright nickel plating; decorative hardware
February 1, 2008
Experiencing a problem with etching/pitting on brass decorative hardware parts as part of a Bright Nickel electroplating process; final co-deposit is Hex-Chrome. Parts are run on a automated hoist line and etching/pitting occurs when the racked parts transfer from the cleaning system rinse to the bright nickel plate. Etching occurs on the lower edge of the part common to the area on the part where the rinse water sheets or drips off. If we change the orientation of the part on the plating rack to have the back of the part enter the Bright nickel solution first v.s. lower edge (horizontal orientation v.s. vertical orientation on rack) etching is minimized or eliminated. Nickel tank spec's:
Rectifier voltage - 4.5 ± 0.5 volts.
Filtration; yes, specified for 2 turns/hr
Tank temp 120 degrees ± 10 degrees
Ni concentrations are running between 11 to 12 oz/gal
Nickel sulphate concentrations are running between 44 to 46 oz/gal
Immersion time - approx. 5 min to 7 minutes depending on part
Tank was dummy plated approx. 7 days ago; wet analysis indicates brighteners are within specification. Last carbon treat is unknown.
Thanks
Process Engineer - Colorado Springs, Colorado, USA
First of three simultaneous responses --
Try making elecrical contact before the rack bottom hits the nickel solution. This is called a "hot entry" to reverse the galvanic current between the bare brass and the nickel tank current.
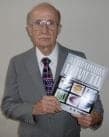
Robert H Probert
Robert H Probert Technical Services

Garner, North Carolina
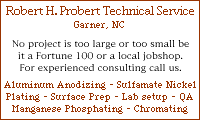
February 6, 2008
Second of three simultaneous responses --
Jonathan,
I'm not quite sure how you can get "etching" going from the cleaning rinse to bright nickel. Do you mean etching of the brass substrate, or are you referring to nickel peeling from brass? Please clarify so we can better help you. If you are getting pits in the nickel, you probably need some anti-pit in the Ni bath, better solution or cathode agitation to dislodge those hydrogen gas bubbles.
Process Engineer - Syracuse, New York
February 6, 2008
Third of three simultaneous responses --
It sounds to me like something is happening before going into the nickel tank- possibly cleaner drying on- you might try misting the parts with DI water to keep them wet...you may have to lower your cleaner temperature, or rinse temperatures if you heat your cleaner rinses. I've seen this "problem" frequently in the past.
George Brackett III- Saco, ME, USA
February 7, 2008
February 11, 2008
Jonathan
I would agree with dry on. But, if you turn the part around and it is minimized, it tells me there is another problem. If it is minimized due to the turned surface being larger or bigger, then you may have a nickel problem. The problem my not be the nickel per say, but too high of current. Does it show up more on the edges of the bar as opposed the center? Has the air movement been hindered? (Maybe the air line accidentally moved?) Lastly, 120 degrees seems a bit low, especially saying ± 10 degrees.
Regards,
Warren, Michigan, USA
Q, A, or Comment on THIS thread -or- Start a NEW Thread