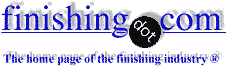
-----
Plating Electroless Nickel onto Aluminium
February 2, 2008
Dear all,
I've been unsuccessfully trying to plate a very big aluminium part (2 x 0,5 m). My tanks have just 1,3 x 1 m and therefore I've been trying to plate on 2 x. Meaning, on end first than turning 90° the part and dipping the other end.
Electroless Nickel plating goes well on both ends, with the exception of the joining line between both halves, where despite my efforts and appeals to the most variant pickling solutions, it produces always a line (around 2 mm) without Nickel, just the aluminium.
I've tried fluoride and nitric pickles, zincate, 2x zincate, even cathodic activation on the electrolytic degreasing, all without success.
It seems, an opposing electrical field between the 2 nickel sides
(aluminium) prevents either the zincate to plate onto the aluminium and consequently the nickel onto the zincate.
I'm reaching the point of giving up and concluding it is impossible to plate EN onto an aluminium part, when the part is too big to fit ones tanks.
I want to understand why this happens and I just thought of asking some opinion to people who have far more experience than I do.
Thank you in advance and best regards,
Paulo
Responsible for a plating shop - Portugal
Plating an aluminum body in 2 steps as you described is not a recommended practice.
You should try to verify first this in a small scale , such a aluminum plate in a 4 liters beaker.
Nevertheless if no chemical treatment has succeeded, you may try to hand scrubbing the problematic area (with scotch brite or pumice) before zincating. This may overcome your problem.
Good Luck,
Bnei Berak, Israel
February 9, 2008
I think that you have correctly analysed the problem. When a part that has surfaces with dis-similar metals is immersed in a conductive solution, a voltage difference is generated. In this case, the aluminum is anodic to the nickel and the zincate either will not plate or will dissolve off of the aluminum, right at the interface, causing blisters or peeling plate.
Other than a larger tank, one "trick" that may work is to put a low cathodic voltage on the part. This can overcome the voltage generated by the dis-similar metals and makes the zincate part immersion and part electroplated. For this to work, you need to enter and leave the zincate bath hot (with the applied voltage on).
consultant - Cleveland Heights, Ohio
February 12, 2008
Hi Paulo.
Read the letters 278,
13456, and in this thread you have a lots of plating tips for titanium materials.
Best regards,
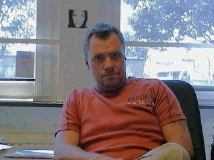
Anders Sundman
4th Generation Surface Engineering
Consultant - Arvika,
Sweden
March 5, 2008
We have successfully "splice" plated Electroless Nickel onto aluminum numerous times. We had many issues in our initial attempts with blistering on the parting line. What we discovered is that we cannot allow the zincate to cross over the nickel, simply get as close to the parting line as you can. With aluminum it is almost impossible to eliminate a splice line. Steel is much easier by way of improved agitation and acid preparation.
Rather than splice the parts, you may want to consider building portable tanks out of wood. Make sure to support the sides and line each chamber properly. You'll only need the zincate, zincate strip and strike solutions.
plating shop- Minneapolis, Minnesota
April 16, 2008
Q, A, or Comment on THIS thread -or- Start a NEW Thread