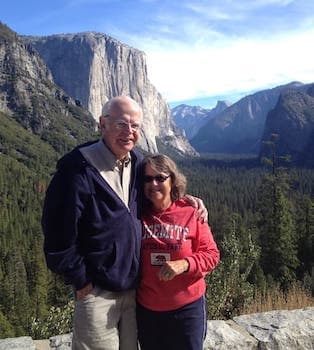
Curated with aloha by
Ted Mooney, P.E. RET
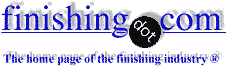
The authoritative public forum
for Metal Finishing 1989-2025
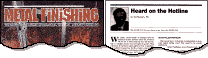
-----
Does chrome become passive
Does chrome plate become passive? I work with a sometimes difficult individual who has basically reinvented plating as we all know it. We plate chrome directly on to tool steel (A-5 or equivalent). When we initially plate the barrels, we reverse etch in a dedicated tank (for a too-long 3 minutes, which I did negotiate with this individual from his original 10 minute etch (nodule city). Occasionally if a barrel is slightly overbore (not enough plate), we reverse etch and add more chrome. We used to do this reverse etch in the same dedicated tank as the initial plating, but now I'm told we can't do this any more because the chrome will passivate in the 20 seconds it takes to transfer from the etch tank to the plating tank, resulting in massive adhesion failure (I've never seen it). We now reverse etch in the plating tank. The dedicated etch tank, enhanced by the extreme long etch times, builds up with iron, and after a while the parts are loaded with nodules. When I renew the etch tank, the nodules go away. I realize lots of people reverse etch and plate in the plating tank, only for seconds, not minutes. We already bulid up enough iron in the chrome tank as it is. Also, when we etch in the plating tank, we are told we can't plate anything (anode and cathode are segregated between multiple rectifiers, no common leg).
George Brackett IIIPlating engineer (35+ years) - Saco, ME, USA
January 30, 2008
First of two simulltaneous responses -- January 31, 2008
For my two cents:
Time is relative to the amperage (and voltage applied in reverse) but
10 min is grossly excessive. 1 min at half the amperage of plating is more than enough in my experience.
Will it passivate in 20 seconds-NO. but that also depends on how long it sets in the plating tank. Is the part allowed to warm up to plating temp before hitting it with full plating amperage? If not, it easily might delaminate.
The best money that your company can spend would be to buy a porous pot setup! My favorite is Hard Chrome Consultants in Cleveland,OH. It works and was several times cheaper than a comparable unit. You need a unit for both the etch tank and the plating tank. The etch tank might require a slightly larger unit than the plating tank. (see later comment) You will need a small rectifier for each unit. It will take a while for it to remove nearly all of the trivalent and trash metal ions, but eventually you will only run it pat of the time. If you used two small units, you could use the plating unit in the etch tank part of the time and it would save a bit of money in buying a larger unit. It will simplify everyone's life!
There is a very remote possibility that you should not be plating other parts at the same time as etching, but I will not buy that without additional evidence, as I have seen a tank the size of a railroad car at an AF base in Texas do it with tiny to huge parts.
A couple of my favorite sayings: But we have always done it that way; and don't bother me with facts (or possibilities) because my mind is already made up.
Hang in there. They told me to cheer up, it could be worse, so I cheered up and it did get worse. Jim
- Navarre, Florida
Second of two simultaneous responses --
You seem to be pretty sure of what you're doing. Your posting sounds more like an intent to find advocates to your point of view instead of technical advise. Convince the customer that after so many years of experience you "know how". Otherwise do as he says.
Incidentally, yes, chrome passivates on exposure to air but is re-activated reasonably well in certain chemistries (basically those containing fluorides) during the initial seconds of the plating cycle.
Monterrey, NL, Mexico
January 31, 2008
We use porous pots, but they are set up to "batch" purify solution when the trivalent gets too high. We cut the solution and readjust. The decant portion goes to the porous pot purification area. I wouldn't have done it this way (my "partners" idea, before I started here), I believe in keeping chemistry as "steady state" as possible, not totally disrupting the process by cutting and readjusting, or by letting the trivalent climb to near-problem levels. (Sigh). I would love to convert this purification to a continuous process, but can't get him to agree...
George Brackett III- Saco, ME, USA
February 7, 2008
Q, A, or Comment on THIS thread -or- Start a NEW Thread