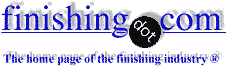
-----
Electropolishing does not create hydrogen embrittlement - it actually reduces it!
January 23, 2008
Several respected fellows have stated that due to the oxygen film that develops at the workpiece during electropolishing, no hydrogen embrittlement occurs during this process. Others claim that hydrogen is, in fact, removed from the workpiece during the process.
I now have a potential client that would like to see the hard data behind the claims. While I can find multiple references of the stated fact, I cannot find any study that documents the conclusion(s).
Can anyone point me in the right direction? Is there a body of work anyone can reference, or an expert in the field that can address this issue for me?
Job shop owner - Colorado Springs, Colorado
First of two simultaneous responses -- January 25, 2008
Jim
Refer to ASTM B242 (2004), section 7.2.1, and
ASTM A380
Annex A2.4
- Colorado Springs, Colorado
Second of two simultaneous responses --
Hydrogen atoms (relative size 1) are perhaps the smallest of all (He?), so they easily find their way to penetrate arrangements of larger and heavier atoms like iron (size 26). Oxygen atoms (size 8) are always in pairs forming the O2 molecule (size 16), thus, they cannot penetrate steel as easily.
Guillermo MarrufoMonterrey, NL, Mexico
January 26, 2008
January 29, 2008
An interesting string. Electropolishing is done anodically, so any gas that is released during the electrochemical processes will be oxygen, not hydrogen, so there is no risk of hydrogen embrittlement during the process. The electropolishing process creates a surface with a chemical equipotential; this results in an electrochemically uniform surface layer that much reduces the opportunity for micro-polarisation on the surface and hence the risk of corrosion is reduced. The equipolarisation is achieved through the formation of a very thin complex structure, often based on phosphate ions (if the electropolishing solution is based on a mixture of sulfuric and phosphoric acids). Other acids suitable for electropolishing will form similar layers. Amongst this complex structure will be a myriad of different metal oxides that will also help protect the metal substrate. These layers will hinder the diffusion of hydrogen into the substrate if the metal is subsequently processed in a way that will induce hydrogen embrittlement. However, such processes normally disrupt the reflectivity of the surface, so electropolishing would normally be one of the last operations carried out on a workpiece, so there is little opportunity for hydrogen embrittlement to occur.
Since electropolishing is anodic, it dissolves the metal to create metallic cations; hydrogen ions are also cations, so if present, the hydrogen can be removed from the surface. When hydrogen is entrapped in the metal structure (as for instance in palladium, which can hold
1,000 times it's own volume of hydrogen) the dissolution of the metal will release any trapped hydrogen, thereby reducing and even eliminating the risk of hydrogen embrittlement.
One final thought - the idea of having both oxygen and hydrogen being discharged from the same electrode does not make me feel too safe....
All the same, I would agree that electropolishing could reduce or even eliminate hydrogen embrittlement.
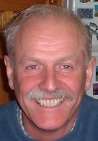
Trevor Crichton
R&D practical scientist
Chesham, Bucks, UK
Trevor Crichton:
You wrote: "Electropolishing is done anodically, so any gas that is released during the electrochemical processes will be oxygen, not hydrogen, so there is no risk of hydrogen embrittlement during the process."
I respectfully disagree; whenever one puts metal in acid, hydrogen is generated.
When you state that "the dissolution of the metal will release any trapped hydrogen, thereby reducing and even eliminating the risk of hydrogen embrittlement.", you must be assuming (and should so state) live entry and exit. "Live entry" is when the workpiece is connected to the positive charge BEFORE touching the acid bath.
My concern lies in the following scenario: A user reads "there is no risk of hydrogen embrittlement" and proceeds to have his workpiece electropolished. The part goes into the acid bath, generates atomic hydrogen, which becomes entrapped in the granular cleavage zones. Then the current is connected and the electropolishing process begins. Surface dissolution occurs as we are all familiar with, but does NOT remove all entrapped hydrogen. I am not comfortable with the statement "there is no risk." I believe hydrogen embrittlement can occur unless the process is specifically engineered for live entry and exit.
Thanks for your time, I look forward to hearing your take on the above.
Aerospace manufacturer - Chandler, Arizona
August 25, 2008
August 26, 2008
Hi, Karl. Thanks for the insight! Regardless of whether Trevor happens to see this and finds time to respond, no user should ever make a final decision based on an opinion rendered by someone who hasn't seen the parts, isn't familiar with the fine details, and who he doesn't even know! An internet forum is just food for thought, and hopefully only a very tiny piece of the process of deciding what to do.
Regards,
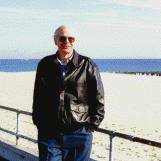
Ted Mooney, P.E.
Striving to live Aloha
finishing.com - Pine Beach, New Jersey
January 18, 2009
HYDROGEN ABSORPTION AND DESORPTION DURING ELECTROPOLISHING
Depending of electrolyte composition, properties of material to be electropolished and another factors electropolishing process can be performed in two different polarization conditions below and on plateau or above plateau of polarization curve. Those two different electropolishing conditions are manifested by oxygen evolution from the anode in the case of electropolishing above plateau and by lack of it in former case and they can both be visually observed. In both cases very good smooth finish can be obtain (one of the purpose of the utilization of this process). But this is the end of achieved similarity. It is common knowledge that on the opposite electrode
(cathode) hydrogen gas evolves in both cases. Some hydrogen outgases from the electrolyte and some of it remains in the electrolyte. Taking under consideration that that hydrogen and oxygen are very antagonistic to each other and by this hydrogen can not enter material which is electropolish above plateau and is blanketed by outgassing oxygen (the case of most commonly electropolished material; austenitic stainless steel in phosphoric/sulfuric electrolyte). But in another case when electropolishing is performed below or on plateau of polarization curve (below oxygen evolution level) hydrogen created on the cathode enter electrolyte in gaseous form H2 (molecular)adsorb on anode surface where dissociate to atomic form and absorb into the metal and create problem called hydrogen embrittlement(as in cases of many valve metal as titanium,niobium,tantalum etc. also in NITINOL). To remove absorb
(trapped) hydrogen heat treatment is commonly used. But is the new method of electropolishing (in the case of electropolishing below oxygen evolution regime) which not only prevents hydrogen absorption but also removes residual hydrogen from metal the process is called
"magnetoelectropolishing". To learn more about this process you can go to GOOGLE web site and enter the word "magnetoelectropolishing". In the case of electropolishing NITINOL you can read the latest article in Transaction of the Institute of Metal Finishing, Volume
86, Number 5, September 2008, pp 280-285 entitled "Nitinol surface finishing by magnetoelectropolishing".
Sincerely
electropolishing shop - Macungie, Pennsylvania
Q, A, or Comment on THIS thread -or- Start a NEW Thread