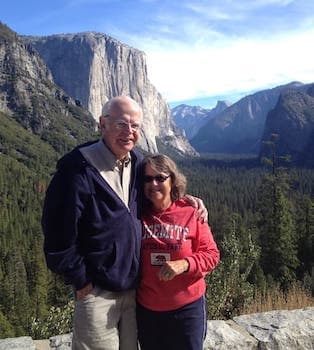
Curated with aloha by
Ted Mooney, P.E. RET
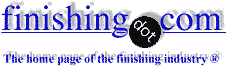
The authoritative public forum
for Metal Finishing 1989-2025
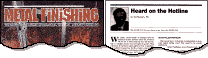
-----
Fluxing Problem in Galvanizing plant
Good day. Our plant has been operating for 10 years and lately we observed some green and yellow spots / discoloration in our galvanized item. What should we do to eliminate such discoloration.
In our flux bath we use ammonium chloride and zinc chloride, what is the appropriate ratio of ammonium to zinc to product a good galvanize finish? We have some problems with items with threaded parts after fluxing. Again thank you.
Galvanizing Plant - Bulacan, Philippines
January 17, 2008
First of two simultaneous responses --
Need a bit more information in this question.
Do you have any quench / passivation after zinc immersion?
Is your flux heated? What temp? Do you measure the concentration of the flux? If so, what is it?
Do the spots have any solid material that can be removed from the galv surfaces?
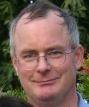
Geoff Crowley
Crithwood Ltd.
Westfield, Scotland, UK
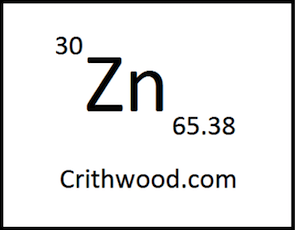
January 19, 2008
Second of two simultaneous responses -- January 19, 2008
Dear Roseanne aka Rose Ann?
Are these green and yellow spots/discoloration after galvanizing? If yes, then perhaps the aluminum in the zinc is too low. If you are talking green/yellow (also maybe orange and black) on the fluxed steel, then the pH of the flux may be too high.
I have found that the best ratio of ammonium chloride (as numerator) to zinc chloride (as denominator) for "dry" kettle (no black bubbling top flux) is 1.6. I have "coined" this ratio numbering system "ACN" during my work in South Africa. Thus "double salt" has an ACN of 0.8,
"triple salt" has an ACN of 1.17. The best result for most general galvanizers is Quadraflux with the ACN 1.6.
What are your problems with threaded parts after fluxing? For more information about flux and fluxing, search this site and you will find a good deal of useful information. Also I have published 25+ articles in the journal Metal Finishing.
Regards,
Galvanizing Consultant - Hot Springs, South Dakota, USA

Q, A, or Comment on THIS thread -or- Start a NEW Thread