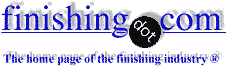
-----
Pitting of Electrodeposited Ni-W
January 11, 2008
Hi,
I'm trying to electroplate Ni-W on a finely polished copper substrate in a bath containing nickel and tungsten salts (copper is cleaned by dipping in a sulfuric solution for a few seconds). The plating is done in a 250cc beaker [beakers on
eBay
or
Amazon [affil links] which is heat to 75 °C and done in DC mode. Magnetic stirrer is kept running in the beaker during deposition.
My problem is that the surface of the coatings always appear to have lots of small holes, which probably come from formation of hydrogen bubbles. Could you please suggest possible solutions for this problem? Thank you very much.
Vee
product designer - Bangkok, Thailand
The primary way of addressing this pitting is by lowering the surface tension with sodium lauryl sulphate or similar wetter. The bigger issue is whether you have analyzed the deposit because I am surprised that you are able to deposit a Ni-W alloy.
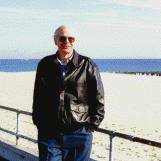
Ted Mooney, P.E.
Striving to live Aloha
finishing.com - Pine Beach, New Jersey
January 11, 2008
January 11, 2008
Ted, you may be thinking of tungsten carbide. Tungstanate has been added to nickel plating for years for a thin chrome like hard top coat, especially in brush plating.
The wetting agent is very necessary.
The use of boric acid to control surface pH is also very common.
Agitation is very important. I would make an air sparger rather than a spin bar. For the air source, you can use a small fish bowl air pump. Note that you can not use the "air rock" that comes with it as it is plastic foam that will dissolve.
75C is a bit high. Some of the organics break down at this temp. 65 would be better and 70 a practical max.
You might get by with using a tearless baby shampoo for a wetting agent. Use only one drop to start with. It might destroy your plating solution, but some have been used, years ago, for tiny lab work.
- Navarre, Florida
January 16, 2008
Nickel-tungsten alloys can be deposited from a modified Watts-type nickel bath. The tungsten is added in the form of sodium tungstate, but only small amounts are deposited. I recall seeing some SEM sections of these alloys and the tungsten is deposited as discrete layers. I do not know the efficiency of tungsten deposition, but I would be surprised to see it at 100%, so it is quite probable that hydrogen is also being deposited and this could result in the pitted appearance. I suspect it may be interesting to use pulse plating with this system to see what happens!
The problem in question sounds to me as if it is a wetting agent problem, so Ted is right in recommending the use of a surfactant. I am also slightly concerned about the process being done in a 250ml beaker [beakers on
eBay
or
Amazon [affil links] - this seems a bit small to me, unless the components are very small. I would recommend a larger vessel - say 1 litre, and have good solution agitation. However, do not give it too much or you will start to take air into the electrolyte and this could make the tungsten throw out an oxide/hydroxide precipitate. I would recommend a suitable magnetic bar stirrer
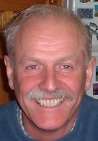
Trevor Crichton
R&D practical scientist
Chesham, Bucks, UK
Dear Ted, James and Trevor:
Thank you very much for all of your very helpful suggestions! I will modify my bath by adding some wetting agents and also better control the way to agitate the bath.
I'm grateful for your comments and helps.
Regards,
Vee Boon
- Bangkok, Thailand
February 13, 2008
Sorry that I didn't realize that Ni-W is a plateable alloy; but James and Trevor got us back on track there.
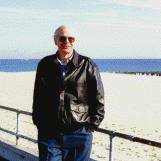
Ted Mooney, P.E.
Striving to live Aloha
finishing.com - Pine Beach, New Jersey
February 13, 2008
Trevor, if we consider Watts type bath for Ni-W deposition, you are right. But take under your account that Ni-W plating is not a beaker curiosity but a real existing process. The Ni-W deposition is applied for glass casting (kinescope lamps) instead of chromium because of very low adhesion of molten glass and low cracking. In this kind of deposition the tungsten content is near 40% and the bath is not similar to Watts type. In the case avoiding of pits is crucial for reaching appropriate production. It's not easy, because of high temperature of the bath and breaking down of surfactants.
Janusz LABEDZ- Warsaw, Poland
March 4, 2008
March 6, 2008
- Diminish your AMPERAGE (between 1/2 to 1/3)
- Diminish T too
- Interfacial tension is in some way compensated by increasing rpm
(but introducing air bubbles. Find improvements Before add a surfactant to increase your state of knowledge of the process.
Jose Castellanos
Minneapolis. MN
- Minneapolis, MN, USA
Any experience with Ni-W brush plating as a substitute of hard chrome plating? I found some results from 1997 but nothing recently published. The application would be onto precipitation hardenable steel (15-pH) as anti wear coating (lubricated).
Eve Izkara- Madrid, Madrid, Spain
October 17, 2008
Q, A, or Comment on THIS thread -or- Start a NEW Thread