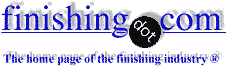
-----
Preparation Process, Anodizing and Sealing A356 and Cast Aluminum Alloys
Q. I'm having a problem trying to anodize various cast aluminum alloys. Actually, they appear to anodize fine, but they are not sealing (DI water seal, seal quality determined by admittance). The alloys in question are A356 and 535 (Al-7Mg).
Scott Dickerson- Fremont, California
2000
A. The first thing I would recommend is to check your seal operation. One way to check this is to anodize and seal a piece of wrought aluminum (a panel), Then do your seal quality test on the wrought panel. If the panel passes, then your seal is working ok and the problem is with the material. Of course if the panel fails, then your DI seal is not within spec. Incidentally, you may see seal smut on the wrought panel - this is the formation of seal product (boehmite) on the surface of the part. It actually means that the seal is working ok. There are a couple of DI seal additives commercially available that work as anti-smutting agents.
The most common error in running a DI seal is that it is not hot enough - the water must be at or above 98 °C. The pH must be between 5.5 and 7. You can buffer to help keep the pH in balance. Immersion time may need to be 30 minutes or more. Many manufacturers in your geographic area specify seal times of 1 hour per mil of oxide for critical applications.
Sjon Westre- Minden, Nevada
2000
Q. We are currently specifying some lightweight high strength Al parts that will need a high degree of corrosion protection. When anodized, the surface appearance of gravity cast or high-pressure cast A356 alloys is mottled or blotchy. Does squeeze casting with its near zero porosity and smaller grain size produce a visually more acceptable anodized surface finish?
Mike Putnam- San Diego, California
2003
A. I cannot address "squeeze" casting, but I can address 356.
First, you "anodize" "aluminum". All that silicon and other junk in the recipe does not anodize and comes out a grey color.
Also, in the case of thin walls in die castings and sand castings (again, I cannot address squeeze), the silicon concentrates even more on the surface.
Whether lesser or more porous, the industry standard for increasing the quantity of aluminum on the surface is a dip in 100% Nitric Acid with 2 pounds per gallon ammonium bifluoride.
All of this information was recently transferred in a half day seminar I presented in SanDiego for all the anodizers that I knew to contact in that area..
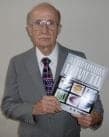
Robert H Probert
Robert H Probert Technical Services

Garner, North Carolina
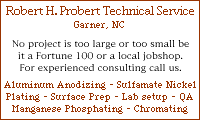
2003
Multiple threads merged: please forgive chronology errors and repetition 🙂
Q. Hi, I am currently working for a company that sells high voltage cable clamps that are sand cast (die casting will be considered) of the A356 alloy. For most customers this alloy provides sufficient corrosion resistance. However, we do receive some requests for an anodized clamp. I know this alloy is difficult to anodize and am therefore putting much thought into preparing a process that will result in a good quality anodize. Most of the knowledge I have obtained is from an old ASM metals handbook (8th ed.) and is likely out of date.
Please advise me on any parts of my plan that should be altered. Clearly I have not yet decided on most of the chemicals to be used. I have left out rinsing.
Vibratory finishing(smooth surface) … solvent clean(remove oils) … inhibited alkaline clean(remove soils) … acid clean(remove oxides) … acid etch(nitric acid with fluorides - remove precipitate and desmut) … anodize.
I would also like to know how important the mechanical finish is, must the surface be smooth to anodize well or just clean? In my mind it seems a good anodize requires a clean surface with minimal precipitate and small grain size, is this correct? Also hould I be considering grain refiners?
Thank you very much, any help is greatly appreciated.
product designer - Melbourne, Victoria, Australia
January 6, 2008
January 9, 2008
Q. After more searching through the earlier posts on this site I have made a little more progress on the plan:
1. Trichloroethylene clean
2. Acid clean
3. Caustic etch
4. HF/nitric desmut
5. anodize
My theory is this:
Trichloroethylene removes all oils. Acid clean removes soils and oxide. Caustic etch evens out the surface but reveals more silicon. HF/nitric acid removes silicon. Surface is then clean and ready to anodize.
I removed the tumbling step as I am not sure it is necessary.
I am still very uncertain and am only stating my plan as a base to work with.
Thank you for any suggestions.
- Melbourne, Victoria, Australia
A. Step 1 is fine, but you may find the use of trichloroethylene regulated to an extent that an ultrasonic cleaning station may be an easier approach. Step 2 will usually be a non-etching alkaline cleaner rather than an acid cleaner. Don't forget Step 6, sealing -- it's not optional. Good luck.
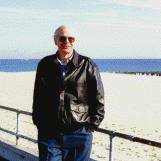
Ted Mooney, P.E.
Striving to live Aloha
finishing.com - Pine Beach, New Jersey
January 10, 2008
![]() |
A. Aluminum fines can cause a serious problem in a vapor degreaser using trike. Notice it is "can" , not "will". There are some conditions that go with it, but many people do not properly maintain their degreasers. Check your literature on the degreaser and possibly the internet. James Watts- Navarre, Florida January 10, 2008 January 10, 2008 Q. Ok. Thank you for your help. I hate to ask questions that are too simple to be of any interest to the people on this site, but I have been researching this for over a week and still have not found a pretreatment process for these casts. - Melbourne, Victoria, Australia |
A. The alkaline cleaner is intended to be a cleaner not an oxide remover; it is the nature of how cleaning works that alkaline cleaners are better than acid (higher temperature for greater solubility, caustic for saponification, etc.)
Ammonium bifluoride is slightly safer than HF, but still a scary process.
If you are missing anything here, it's that most anodizers buy proprietary cleaners, desmutters and seals, and the chemical houses that supply them are usually willing to run sample parts for you. Detailing a successful process is easier and faster when a skilled practitioner is working at it in a well equipped lab, especially if you are working with a difficult to anodize part.
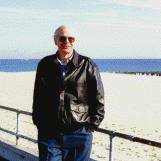
Ted Mooney, P.E.
Striving to live Aloha
finishing.com - Pine Beach, New Jersey
January 11, 2008
![]() |
A. Stay out of alkali etch, it does the opposite of what you want. You want to decrease the area of silicon on the surface and increase the area of aluminum (which is what you "anodize"). Alkali etching chews away the aluminum and increases the area of silicon, you do not want to do that. ![]() Robert H Probert Robert H Probert Technical Services ![]() Garner, North Carolina ![]() January 11, 2008 A. You are adding the ammonium bifluoride to get the fluoride ion. Ammonium bifluoride is extremely safe to handle compared to many other materials if the barest of minimum safety procedures are used. HF on the other hand, even 48% is mean wicked and nasty, but is a relative pussycat compared to 70% HF. - Navarre, Florida January 11, 2008 |
January 15, 2008
Q. Thank you all for your help.
The clamp is composed of 2 parts, top and bottom, with a bolt on each side to pull each part together and clamp onto the cables.
The strange result from the anodize is that each part turns out a different color. The bottom part turns out with little color change and the anodize is more easily scratched off. The top part turns out darker gray, which I understand is due to the silicon, but the anodize is harder to scratch off. The bottom part also appears to have been polished with a coarse belt on some surfaces (~20% of total surface area).
The shop has not opened after the new year yet so I cannot ask them their process.
Is it likely that while they polished the bottom part mechanically they instead used a stronger etch on the top part, revealing more silicon leading to the darker appearance? I am confused that if this is the case, the part with greater silicon surface content seems to have anodized better (harder to scratch off).
Robert, do I not need the caustic etch to smooth the surface? It is quite rough after sand casting.
Should I used vibratory tumbling (or some other method) to smooth it? I am still unclear whether a smooth surface is required for a good anodize. Also, does the acid treatment remove oxide?
Now, regarding HF/Nitric vs Ammonium Bifluoride. If ammonium bifluoride is the safer option, does this mean HF/nitric is the more effective option?
I think that I'm being told that HF/nitric is only slightly more dangerous, but pure HF is extremely dangerous (Ted and James?).
Anyway, thanks again for all the help.
- Melbourne, Victoria, Australia
A. You are adding the bifluoride to nitric acid to get an equivalent (virtually identical) acid to a nitric-HF tank.
Caustic etch on a sand casting is a mixed bag as some of the high spots will be reduced and some will be accentuated.
Sand cast parts are typically not cosmetically attractive, especially when dyed.
I always thought that a high silicon aluminum needed to go thru a fluoride containing bath step. It is a decent combination of desmut/deoxidizer and etch when the tank is new.
- Navarre, Florida
January 17, 2008
A. James Endersbee,
Do exactly as Robert Probert suggested. I don't think you need to etch in an alkaline cleaner before or after it. But you can customize the process if it suits your needs.
Some years ago, I tried the same formula on sand casting and it worked.
If it works for you then let us (India) equal the series with Australia in Adelaide...Good luck
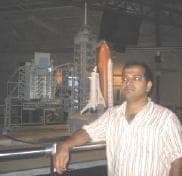
Hemant Kumar
- Florida, USA
January 21, 2008
Now that I pay attention, Mssrs. Probert and Bansal are correct, of course. There is little advantage and a lot of disadvantage to alkaline etching in this case.
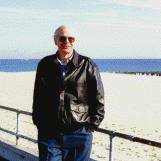
Ted Mooney, P.E.
Striving to live Aloha
finishing.com - Pine Beach, New Jersey
January 22, 2008
January 24, 2008
Q. Ok, I think I'm sorted then.
1. Ultrasonic clean
2. Non-etching alkaline clean
3. Nitric + Ammonium bifluoride
4. Anodize
5. Seal
(rinsing not shown)
Thank you all. Hopefully I will have some samples done soon, in which case I will let you know how they turn out.
Hemant Kumar, while I appreciate your help, unfortunately I don't have the power to affect the outcome of the test! Let's see how it unfolds.
Can I not skip the ultrasonic clean? Isn't the alkaline clean effective enough?
James Endersbee [returning]- Melbourne, Victoria, Australia
A. First the generic answer, James: Unlike most other metals, aluminum cannot be electrocleaned; further, the alkaline cleaners for aluminum must be kept relatively mild. So it is often necessary to preclean in a vapor degreaser or ultrasonic cleaner. But, yes, sometimes a corner can be cut.
Now for the specific situation. None of us have seen the parts nor do we have a clear understanding of all of the fine details of the parts and the soils they have been exposed to. All of what you read on this thread -- I'm pretty sure you understand this, but we'll say it for the benefit of others -- is general guidance regarding what to try in your lab development phase.
Nobody is suggesting that you install an untested anodizing sequence based on book knowledge of what often works for someone else's parts. I can't count the times people have set up process lines, or made very large but wrong chemical additions to a huge process tank, or created thousands of gallons of witches brew in an attempt to do waste treatment by adding this, and then that, and then the other thing :-)
Book knowledge is a guide for things you should consider, not a substitute for experiment. Good luck.
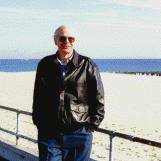
Ted Mooney, P.E.
Striving to live Aloha
finishing.com - Pine Beach, New Jersey
February 7, 2008
![]() |
Q. What is the balanced equation for adding ammonium bifluoride to nitric acid and water? Chuck Ritchard- Grand Rapids, Michigan, USA April 19, 2013 April 23, 2013 A. Hi Chuck. I don't think 'balanced equation' is exactly the right term; it's a mixture, not a compound. I think you are asking in what ratio these chemicals should be mixed. I believe it depends on the application but that Bob Probert has offered one very good answer. Good luck! Regards, ![]() Ted Mooney, P.E. Striving to live Aloha finishing.com - Pine Beach, New Jersey |
Q. My question regarding the balanced equation was to understand what the by-products were when mixing Ammonium Bifluoride and Nitric Acid and whether or not they could be reclaimed through a filtration process.
Charles Ritchard [returning]- Grand Rapids, Michigan, USA
April 24, 2013
A. Those materials do not react with each other to produce any filterable precipitates. They both just stay in solution.
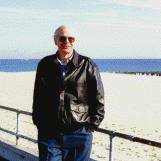
Ted Mooney, P.E.
Striving to live Aloha
finishing.com - Pine Beach, New Jersey
April 29, 2013
Pretreatment of A356 aluminum before anodizing
June 3, 2020Q. I am currently processing a356 aluminum for anodizing using the following pretreatment process:
1) non-etch cleaner
2) rinse
3) alkaline etch
4) rinse
5) acid desmut - HNO3 + fluoride salts
6) rinse
7) proprietary iron-based, nitric-based deoxidizer
8) rinse
9) sulfuric anodize
The reason I use an alkaline etch is because if I do not, I get a non-uniform appearance following anodizing. I have recently ran tests using the following process.
1) non-etch cleaner
2) rinse
3) proprietary deoxidizer - Fe and HNO3 based
4) rinse
5) anodize
These parts came out with a non-uniform appearance. I would like to ultimately remove the need for the homemade acid desmut (HNO3 & fluoride salts) because of the fumes produced. I would also prefer to not use the alkaline etch as I always thought you should never etch a casting.
Any feedback would be much appreciated.
- Brunswick, Ohio, USA
![]() ![]() |
June 4, 2020 A. Hi D! ![]() Rachel Mackintosh lab rat - Greenfield, Vermont A. The reason to avoid alkali etching is because the alkali decreases the exposed area of aluminum and increases the exposed area of silicon, exactly opposite of what you want to do. On 356, change your acid to 100% commercial nitric acid with 2#/gal ammonium bifluoride, then after about 30-40 seconds jerk it out and double rise and enter the anodize. You do not need the wrought alloy deox on 356 sand castings. ![]() Robert H Probert Robert H Probert Technical Services ![]() Garner, North Carolina ![]() June 4, 2020 |
Thank you Rachel and Robert for your timely response to my post. I forgot to mention that these castings are being cleaned prior to anodizing or chem-film. I was really certain that using a ferric/nitric-based deoxidizer would be enough to obtain a clean and uniform surface. Perhaps the condition of these parts from the manufacturer require at least, a slight etch in order to provide some uniformity to the surface. As you can see from the original pictures, the non-etch parts do not possess a uniform appearance similar to the etched parts. It is possible that I setup my process to include a quick etch (long enough for the reaction to begin), followed by a few minutes in the proprietary deoxidizer. This would at least remove the use of the secondary, highly concentrated nitric desmut. Eliminating the fume from that solution is my first priority.
Q. If you have any additional feedback, I would enjoy reading it. Thank you both and stay safe.
D Shoaf [returning]- Brunswick, Ohio, USA
June 5, 2020
A. Our main impetus for trying to find a "safer" desmut with a dual use was twofold:
the big part was not the nitric so much as the hydrofluoric. We inherited a few techs from a now-defunct circuitboard manufacturing plant in the region, who came to us with scars and stories. My mentor and I both pledged ourselves to do everything we could to protect our crew. They say, familiarity breeds disrespect, or some such.
I never want to see one of my work buddies suffer HF burns. But of course that comes with a price, which is that a non-HF desmut tank has a short shelf life. You will have to dump this tank A LOT.
The other bit is that we ran out of space for tanks. Lol. If we had space for even one more, I'd just turn it into a castings-only desmut tank. And they know that. I put one in a vacant dye half-tank when they weren't looking ; )
I respect what you are doing. It may not be finishing best practices, but it is worth thinking out of the box when you actually like your coworkers! Best of luck to you and your impellers!
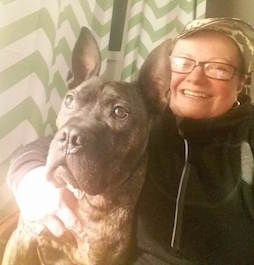
Rachel Mackintosh
lab rat - Greenfield, Vermont
June 11, 2020

Q, A, or Comment on THIS thread -or- Start a NEW Thread