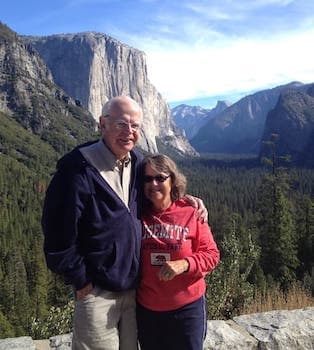
Curated with aloha by
Ted Mooney, P.E. RET
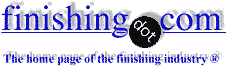
The authoritative public forum
for Metal Finishing 1989-2025
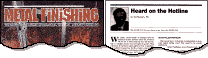
-----
White rust formation on fasteners within one day after plating
Hello all,
I am Murali Sundaram working as a product engineer in a fasteners industry. Recently we have commissioned a auto acid zinc plating plant for fasteners. We have conducted the trial and the plating was visibly ok after removing from the drier. But within one day it starts black patches especially on threaded places. The black patch is not coming on shank (plain) or other places. It is coming on all passivations. For the same components if we dry it in sunlight itis found to be ok. The plating bath parameters are perfectly within the manufacturers specifications.
Is it due to ineffective drier or could be any other reason?
can anyone help me in this issue.
Thanks in advance.
Regards,
process engineer - Coimbatore, Tamil Nadu and India
January 5, 2008
First of three simultaneous responses --
Hallo Murali,
Let us know, what exactly the matter is: white rust or black patches. They seem to be quite different problems. Besides, do you observe also red rust formations in such a short time?
- Warsaw, Poland
January 9, 2008
Second of three simultaneous responses --
Options are get the vendors involved if you bought a turnkey operation or complete equipment from one vendor and proprietary solutions from another.
If it is home built and home brew, you would be best off to hire a highly qualified consultant. there are too many variables, even when it is within "specs". The probability of the drier being the primary cause is small.
- Navarre, Florida
January 9, 2008
Third of three simultaneous responses -- January 10, 2008
This is just guessing without detailed information on the processing and thickness.
I think based upon the "sunlight drying OK" that you may not have enough thickness on the threaded area of the parts (a low current area). In many chloride zinc plating processes there is a large differential in coverage rate (throw) between the high and low current density areas. This less thick plating is subject to abrasion in the dryer and becomes even thinner. Thin plating tends not to get a good conversion coating and this is made worse by rub off in the dryer. The third possibility is that the dryer is not functioning properly. Parts are either not fully dried before being put in storage or the temperature is too high and the chromate coating is being powdered.
As I said, these are guesses at common causes.
process supplier - Great Neck, New York
Q, A, or Comment on THIS thread -or- Start a NEW Thread