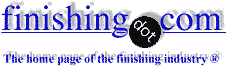
-----
Gold rhodium plating method
2007
dear sirs,
I would like to know the exact steps that I have to use for max quality results at gold rhodium plating.
-is there a specific rate between the volume of the gold jewellery that I want to plate and the size of the anodes?(ex. sometimes I have to rhodium plate just rings weighting 7 gr each and other times chains weighting 30gr each)
-for anodes I use Ti/Pd , witch sould be the best material for the cathode?
-the rhodium solution normaly has inside H2SO4 or phosforic acid? so after the de-oil and before I go to rhodium I have to make a acid bath by H2SO4 or phosforic acid solution?
-after the rhodium bath I leave the jewellery in a bath with hot water and soda , is it correct or there is another better way for deactivation?
-I use the same rhodium solution, for a specific company, and I do not have the same results, is it possible the company that produce it to have several qualities(colors) for the same percent of Rh per lt?
-is it a way to make more microns Rh plating so the final jewellery to be more strong( the 18k are very soft and easily you can skrach, mark them)?
thank you,
jeweller - Athens, Attiki, Greece
Marios,
I'll try to answer your questions in order. The anode material area should equal to or can be greater than the cathode material area. We go by area of the cathode, not weight. You can drape the chains on racks in a horizontal fashion, so they don't hang way below the anodes. Cathode material should be copper, whether it's wire or the base material for a plastisol coated rack. Rack tips or prongs can be stainless steel. The cathode bar can be 316 stainless rod. You don't really need an acid dip before Rh plate as long as the ultrasonic or soak clean solution is rinsed well. Gold does not have to be activated. Most jewelry mfgs use a hot DI rinse, steam dry, or oil free air blow dry following Rh plate. I don't know why you would need a hot soak at the end of the process. Remember the Rh plate will be directly representative of the substrate appearance. It is only a thin coating. The Rh solution should be sent out for analysis once per month at a minimum to be sure the solution is up to par. I like to keep the Rh concentration close to 10 grams Rh metal per US gallon. If the concentration is as such you can achieve a slightly higher thickness. "Microns" is out of the question. How about 10 microinches for thickness (about a quarter of a micron)? That is more than most jewelers plate, and would give you good quality. I hope this helps you!
Process Engineer - Syracuse, New York
2007
hello sir I'm having some problems with my Krohn rhodium plating solution. I recently bought a 1/2 gram bottle of the solution to plate on silver jewelry that I produce for sale but the plated piece comes out with a dark colour so I was wondering if its the wrong cathode I'm using..I'm using the rhodium plated anode and cleaning the pieces throroughly through a boiling process of soap and water and then brushed, rinsed and heat dry then I plate the pieces but the outcome is a dark colour please help me..please recommend tips or even steps I should follow thanks
Rick Deokie- Guyana, South America
April 22, 2010
Q, A, or Comment on THIS thread -or- Start a NEW Thread