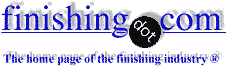
-----
Anodising thickness not being achieved

Q. Hello Mr Probert. We met back in Valdese NC when you came to help us start up our anodizing line.
We are currently trying to get the thickness on some parts to the customer specifications as well as the color to dye black dark enough. The parts they're sending us are made from sandblasted 7075 alloy and our aluminum racks are 6061 alloy.
They want Type 3 @ 1 mil thickness but even at 15 min ramp /75 min run time and 13 amps (81 sq in surface area @ 24 amps per sqft) per part (test running only one at a time) and all chemicals have been tested and are at appropriate levels ... we cannot get the thickness over 0.4 to 0.5 mils.
Is it possible that the rack (6061 alloy) is robbing the amperage from the part? And if so could this be because of running only one part? And would running more compensate the amperage loss ... or should we increase the amperage?
- Valdese nc
December 28, 2022
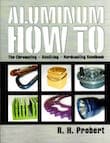
Aluminum How-To
"Chromating - Anodizing - Hardcoating"
by Robert Probert
Also available in Spanish
You'll love this book. Finishing.com has sold almost a thousand copies without a single return request :-)
A. Since 7075 is very slightly more conductive than the rack 6061 (my page 53), then you can expect the opposite effect, but here, the current had to go somewhere, so it probably went to the rack because the electrical contact was not broad enough, which is a common problem with shops who do Types II and III: production rackers do not notice that 24 ASF takes a broader contact than 12 ASF. Check the rack thickness and come on back.
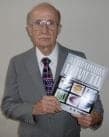
Robert H Probert
Robert H Probert Technical Services

Garner, North Carolina
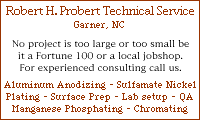
Q. Hello Mr Probert. We met back in Valdese NC when you came to help us start up our anodizing line,
We are currently trying to get the thickness on some parts up to the customer specifications as well as the color to dye black dark enough. The parts they're sending us are made from sandblasted 7075 alloy and our aluminum racks are 6061 alloy.
They want them type 3 @ 1 mil thickness -- ut even at 15 min ramp, 75 min run time and 13amps (81 sq in surface area @24 amps per sqft) per part (we're test running only one at a time) and all chemicals have been tested and are at appropriate levels. We cannot get the thickness over 0.4 to 0.5 mils.
1. Is it possible that the rack (6061 alloy) is robbing the amperage from the part? And, if so, could this be because of running only one part? AWould running more compensate the amperage loss.
Or should we increase the amperage?
- Valdese North Carolina
December 28, 2022
⇩ Related postings, oldest first ⇩
Q. We are currently anodizing aluminum die castings with titanium racks. For some reason we cannot reach 25 micron (1 mil) thickness. Is it because of the titanium racks or because of the alloy. On other alloys we reach 25 microns and more without any problem.
Chloe Vanalle- USA
2002
A. Based upon the limited information (and no mention of burning at contact points), I suspect a high-silicon diecast alloy. The Aluminum Anodizers Council's Anodizing Reference Guide (http://anodizing.org/reference_guide.html) shows 0.0005" maximum hard anodize thickness for alloys 360 and 380. Titanium racks can often be used for hard anodizing very small parts but are generally a disaster for any anodizing of large surface area parts.
Ken Vlach [deceased]- Goleta, California

Rest in peace, Ken. Thank you for your hard work which the finishing world, and we at finishing.com, continue to benefit from.
A. Due to the high percentage of alloy content in die-castings, it is extremely difficult to achieve thick anodic coatings without burning. The above quoted 0.5 mils is about the maximum for normal anodizing methods. There is, however, at least one proprietary method which can can build up to 2 mils of anodic hardcoat on these high pressure die-castings.
Chris Jurey, Past-President IHAALuke Engineering & Mfg. Co. Inc.

Wadsworth, Ohio
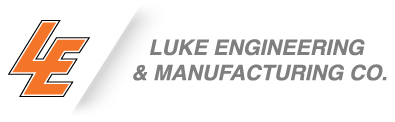
Multiple threads merged: please forgive chronology errors and repetition 🙂
by Runge & Kaufman
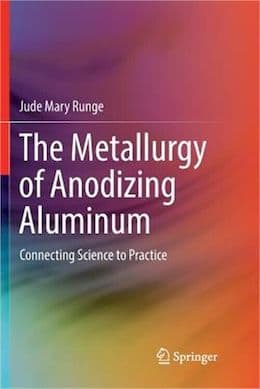
on eBay or Amazon
or AbeBooks
(affil link)
Q. We are working with hard anodize of aluminium with standard sulfuric acid solution and cannot reach a thickness more that 75-80 micron. Please let me know if there is a possibility to reach a thickness of 150 micron and more with this process or do we need something else.
Thanks in advance.
- Israel
2002
Treatment &
Finishing of
Aluminium and
Its Alloys"
by Wernick, Pinner
& Sheasby
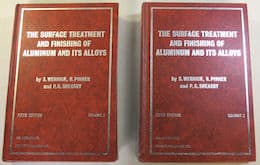
on eBay or Amazon
or AbeBooks
(affil link)
A. Yes ... it is possible (but unusual) to get 150 microns (.006") depending on the alloy, your use of proper racking techniques, and processing parameters.
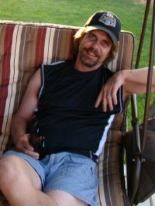
Marc Green
anodizer - Boise, Idaho
A. I think in inches so 0.000 040 X 80 = 0.0032 inches thick. If that is right, then YES, let us now know the alloy and we will come back to you with more data.
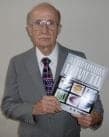
Robert H Probert
Robert H Probert Technical Services

Garner, North Carolina
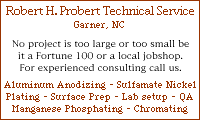
? Am I incorrect? I believe approx. 25.4 microns = 1 mil (.001")?
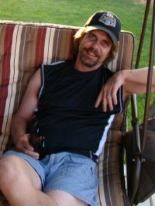
Marc Green
anodizer - Boise, Idaho
You're both right. 25.4 microns to the mil, so divide the microns by 25.4 to get mils, or multiply the microns by .000 040 to get inches.
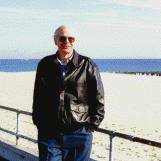
Ted Mooney, P.E.
Striving to live Aloha
finishing.com - Pine Beach, New Jersey
? But Ted,
By my calculations he is wanting almost a 6 mil coating, yet by Roberts figures...the coating is 3.2 mil...unless Robert was looking at coating growth on top of the substrate?
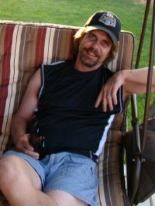
Marc Green
anodizer - Boise, Idaho
A. The coating he is getting is 75-80 microns, equals 3.2 mil. The coating he'd like to get is 150 microns, equals 6 mil.
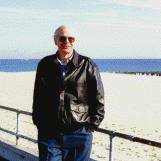
Ted Mooney, P.E.
Striving to live Aloha
finishing.com - Pine Beach, New Jersey
A. We anodize at 0°C in a 10% H2SO4 electrolyte and can achieve that kind of thickness, temperature is critical because if the part gets too hot due to high current density you will burn the part.
Guillermo Luna- Mexico City, Mexico
A. Max thickness of hardcoat is limited primarily by the alloy. Since the coating is an electrical insulator, the better the structure (tighter, denser, etc.) the better it insulates and the lower the maximum thickness obtainable will be. On 6xxx alloys, getting anything over 75 microns (roughly 3 mils) is nearly impossible.
On 7xxx alloys on the other hand, getting 150 microns is possible. Ramping is critical (how fast the maximum current density is achieved ). Others may argue that modified power, either superimposed AC over DC or pulse rectification will have a benefit. That would be up to the suppliers of the specific process you employ.
Good luck and let me know how you make out.
For your information, there is an International Hard Anodizing Association (www.ihanodizing.com) that has technical symposiums every 2 years. Attending something like this might establish the network you need to tackle hardcoat concerns.
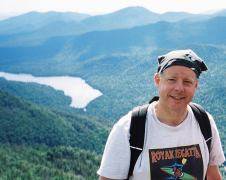
Milt Stevenson, Jr.
Syracuse, New York
Multiple threads merged: please forgive chronology errors and repetition 🙂
Q. Hi all,
We are having trouble achieving a 25µm anodised layer on our components.
The alloy we are anodising is 6026 T6 and our anodising parameters are stated below.
Concentration - 10% sulfuric acid by weight
Temperature - 21°C
Voltage - 13.5 V
Current density - 1 A/dm2
Time - 80 minutes
Is this lack of thickness to do with the current density being too low?
Also, should we be achieving the required 25µm thickness quicker?
Regards,
production engineer - Gloucester, UK
2007
![]() |
A. OK, 25 µm is 0.001 inches. 10%/weight is only 110 gm/L, you need at least 165, so add 55 gm/L (that is 4 fluid ounces per gallon of 66 degree baumé Sulfuric Acid. ![]() Robert H Probert Robert H Probert Technical Services ![]() Garner, North Carolina ![]() A. Yes, your voltage is way too low, and that's why you are not achieving the desired thickness in a reasonable amount of time. Are you limited to only 14 volts with your rectifier? If not, just anodize at the same current density you are, and let the voltage float. At 12-15 amps/sq ft, you should achieve 25 microns in approx. 45 minutes. ![]() Marc Green anodizer - Boise, Idaho A. First, I doubt if 13.5 volts is giving you 1 amp/DM. I will bet that your rack is pulling part of the amperage. - Navarre, Florida A. I'm sure you can get your target thickness with shorter time (around 50 minutes) when you lower the temperature to 18 °C and increase voltage to 17 or 18 volts. John Hu- Singapore |
A. John
You do not state what thickness you are achieving, but using your parameters, you should be able to achieve 25 µm in about 72 minutes. If you do not have particular coating requirements, you could go to 1.5 asd and achieve the same thickness in about 48 minutes.
Make sure your connections and agitation are good, and that you are not overloading your racks.
- Colorado Springs, Colorado
A. Consider the formula for anodizing thickness:
Thickness (mil)= ASF x Time (min)/720
It seems to me that your current density is too low and at 80 minute time, you may be dissolving some coating as well.
I suggest increase your current density and make sure the parts enter clean in anodizing bath. 70 F temp should be good.
Concentration of the acid is fine. Some people run anodizing at 15% v/v but we have been running at 10% with no issues.
Thanks
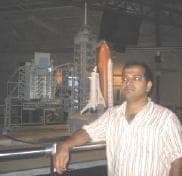
Hemant Kumar
- Florida, USA
January 2, 2008
Q. Respected Sirs,
I am Prem Easwar from India, I am an under-graduate student and I am involved in an anodizing project for my final year. We are required to optimize the anodizing coating at an "UNIFORM thickness of 25 µm" in a "HARD ANODIZING PROCESS".
Initially we do soap degrease, drag-out rinse, cascade rinse, desmutting (H2SO4) and cascade rinse (demineralised water). The cascade rinse is carried out for 15 seconds at ambient temperature and 250 micro semen/cm.
Then Hard Anodizing is done using H2SO4 for "30 MINS" the temperature being maintained at 0-5 °C and the concentration of H2SO4 is 240-260 g/l and 5-17 g/l aluminium content!
Then cascade rinse is carried out for 15 seconds at ambient temperature and 70 micro semen/cm. Then finally sealing is done with Demineralized water at 95 °C for 10 minutes and pH is 6.5-7.5
We use a Lead-Tin alloy Cathode and current density is 35-45 amp/sq.ft.
Please give me advice as to what to do to optimise the coating thickness at 25 um.
- Tamil Nadu , India
January 6, 2010
A. Hi, Prem. The only thing that sounds funny is the H2SO4 desmutting. What kind of smut will this remove? I don't think it will remove either silicon or copper.
The temperature sounds a bit high, with -1 C to 0 °C being more common. The current density seems high, and you haven't mentioned the voltage, but you will need excellent local agitation to prevent burning. The acid concentration sounds high. Do you have some good anodizing books you are working from?
"Optimize" usually means to improve. How well does the process operate as you have described it? In what way do you see it as less than ideal? Thanks.
Regards,
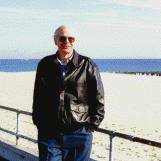
Ted Mooney, P.E.
Striving to live Aloha
finishing.com - Pine Beach, New Jersey
Q. Respected Sir,
The coating is done on aluminium components and the H2SO4 de-smutting is done to remove the aluminium oxide layer that is formed on the surface of the component prior to anodizing.
Also the Industry says that they do not encounter silicon or copper impurities.
And I am very sorry for having omitted the voltage value in my previous post, the voltage maintained is 22 v.
The industry wants a coating thickness between 23 -27 µm (customer specification) so we thought having it at 25 µm would represent a middle value and also give way for some small variation (though we plan to use some statistical control techniques later to reduce variation)
Sir you have mentioned that the acid concentration, current density sounds high, could you suggest some possible values for acid concentration, current density and voltage?
PRESENT VALUES:
1) ACID CONC:240 - 260 g/l ,5-17 g/l Al content
2) CURRENT DENSITY: 43 Amp/Sq.ft at one end and 38 Amp/Sq.ft at the other (Where current enters and leaves respectively)
3) VOLTAGE: 22 V
Please adviSe -- eagerly awaiting your response.
Thank You,
Prem
- Tamil Nadu, India
A. Hi, Prem. It isn't clear to me whether this is an actual anodizing line which is not working properly and you are making adjustments to it, or whether this is a thesis assignment about a hypothetical anodizing line where you are supposed to research this stuff.
You didn't answer yet if you have some good anodizing books to work from. If this is a thesis assignment, you should try to get hold of a copy of "The Surface Treatment and Finishing of Aluminum and its Alloys"; if you need quick practical answers to get a real anodizing line working properly again, I'd suggest Probert's "Aluminum How-to".
This page suggests 165 g/l H2SO4 and if you search the site for "hard anodize" or "hardcoat", you'll see recommendations up to about 210 g/l.
35 to 38 ASF sounds okay for hard anodizing, but there should be no measurable difference from one end of the part to the other; I don't understand that part.
22 volts sounds low for hardcoat, but if you can get 0.001" with that voltage, then it's enough. Please spend some time searching the site as you will find dozens of threads on the topic. Good luck.
Regards,
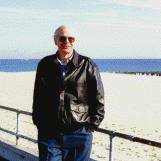
Ted Mooney, P.E.
Striving to live Aloha
finishing.com - Pine Beach, New Jersey
Q. Dear Sir,
I would like to make some clarifications based on your previous post.The problem that I had referred to is in a real anodizing line that is not working properly.
We did go through the various threads in this site and many others over the net as advised by you but we could not find the specific acid concentration that would be required for 25 µm.
Also you have said in your previous post that 22 V sounds low, so could you possibly suggest values for the voltage and acid concentration that would actually be required?
It would be of immense help to us if we had these values with us for further experimentation! Eagerly awaiting your response.
I forgot to mention that we require 25 µm anodizing thickness in HARD ANODIZING!I just thought I would make that clarification. As always I am eager to hear all the responses that I can get.
Thank You,
- Tamil Nadu, India
A. Hi, Prem. Perhaps it wasn't clear, but you don't vary the solution concentration depending on the intended thickness. As previously mentioned, use the 165 g/l suggested by Robert Probert as a minimum, to as much as 210 g/l.
I need to say again that in my opinion to approach the project correctly requires having respected books on the subject on hand. The company should also have specs on hand such as MIL-A-8625 / MIL-PRF-8625 [⇦ this spec on DLA] and ASTM B580 because, regardless of any individual's opinion on a good concentration, voltage, amperage, temperature, or procedure, parts must always be processed according to specifications.
You came here asking our advice because you are new to the technology, and I am trying to help you learn the crucial lesson that although internet forums can be an excellent way to quickly get steered in a proper direction or pick up a clever tip, internet hear-say is not a proper substitute for respected reference materials. If you complete this project without convincing your employer to stock a proper anodizing reference library, then I have failed you in your outreach.
These books and specs will tell you that the required voltage depends upon the alloy that you are processing. But for hard coat of .002" (50 µm) you are probably looking at something like 75 volts. For your .001" (25 µm), maybe about 40 volts. Generally speaking, hardcoat anodizing is considered to be .002" (50 µm thick). Best of luck!
Regards,
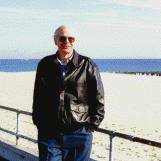
Ted Mooney, P.E.
Striving to live Aloha
finishing.com - Pine Beach, New Jersey
Q. Dear Sir,
I will be very grateful to him if anybody sort out my this problem.
I have job in Aluminium Alloy, 91% Aluminium and 7.2% silicon & rest others.
The required Parameter is Thickness (15-25 Microns), Hardness (HV 400-500), Roughness (Ry-15, Ry-6.3), Area of job is 15.5 sq. inch both sides.
I do this with normal rectifier with sulfuric acid bath, Sp. gravity 1150-1200, temp. 10-15 °C.
Now please advise the required parameters for above standard anodizing like required voltage, required amps, required temperature and required time per cycle.
Please Advise.
- Faridabad, India
April 9, 2012
A. Hi Pooran. We appended your inquiry to a thread which should help you determine the ideal operating parameters for your situation.
However, you have also introduced the issue of surface roughness; and for that topic you might want to go on to letter 51222, "Maintaining a Surface Finish after Anodizing" and letter 22123, "Hardcoat anodizing surface roughness, Ra/RMS issues, Honing". Good luck.
Regards,
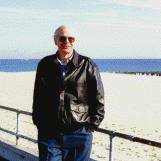
Ted Mooney, P.E.
Striving to live Aloha
finishing.com - Pine Beach, New Jersey
Q, A, or Comment on THIS thread -or- Start a NEW Thread