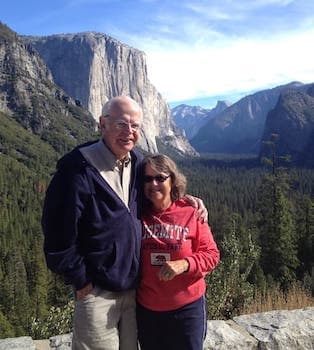
Curated with aloha by
Ted Mooney, P.E. RET
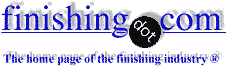
The authoritative public forum
for Metal Finishing 1989-2025
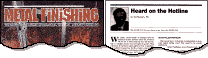
-----
Quality Control Test for Flux Bath
for Engineers, Shops, Specifiers
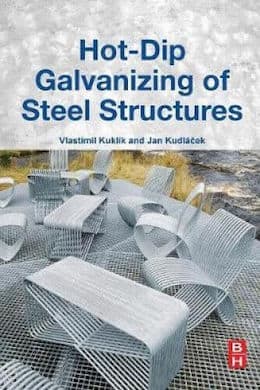
avail from eBay, AbeBooks, or Amazon
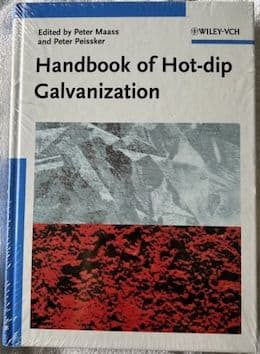
avail from eBay, AbeBooks, or Amazon
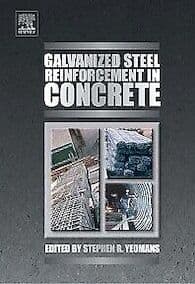
avail from eBay, AbeBooks, or Amazon
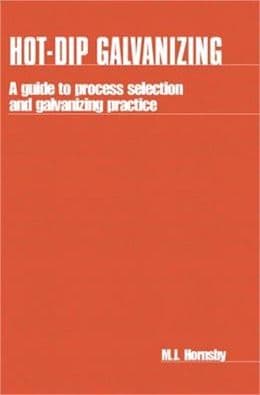
avail from eBay, AbeBooks, or Amazon
avail from Amazon
"User's Guide to Hot Dip Galvanizing for Corrosion Protection in Atmospheric Service" by NACE (1997 only rarely avail.)
avail from AbeBooks, or Amazon
(as an Amazon Associate & eBay Partner, we earn from qualifying purchases)
Q. Dear Dr. Thomas H. Cook
I wish to ask you about the QC tests for fluxing.Which tests are common? any ASTM or other standards could you please suggest?
Noteworthy that , this is about a pipe Galvanizing plant which uses
(12 000litre)double flux bath with baumé No. 47 prior to preheating for zinc pot.
In particular I wish to know if the CuSO4 test (for specimen taken after galvanizing)(to detect red or coppery spots on the surface) is of any use.
Your response is highly appreciated
Sales engineer - Tehran, Iran
2007
A. Sir: Tests for flux are:
1)Degrees baumé of flux solution as measured with a hydrometer at room temperature.
2)"ACN" which is the percent by weight ammonium chloride (numerator) divided by percent by weight zinc chloride (denominator). Measured using heat of solution of dried flux. (e.g. dissolving ammonium chloride the solution gets colder, whereas dissolving zinc chloride the solution gets hotter). From calibrated table ACN is determined. I had 13 outside testing companies test a flux that I made up using exactly the same amount of ammonium chloride as zinc chloride (e.g. ACN = 1.000). Not a single testing company got an acceptable result.
3)Iron +2 as percent by weight. Measured using stable hex chrome as titrant, acid buffer, and iron indicator. Fe +2 not to exceed 1 percent, purify as required using NH4OH and H2O2.
4)sulphate percent by weight (if sulfuric acid is used for pickling the steel). Measured using a precipitating agent and centrifuge until clear solution obtained on adding further precipitating agent. Not to exceed 1%, otherwise precipitate (purify) using barium chloride dihydrate (toxic).
5)Suitable wetting agent in effective range of 1 to 6 parts per 10,000 of flux solution. Only one wetting agent passed all three requirements: (a) reduces surface tension from 80 dynes/sq cm to 30 dynes/sq cm. (b) excellent corrosion inhibitor. (c) provides suds to retain heat at liquid/air interface.
6)pH of 4.2 as measured by pH indicating dye. pH papers and meters do not work. Required HCl or NH4OH to correct pH is done by titration using 1:10 HCl or 1:10 NH4OH to indicating dye end-point and then calculating required conc. HCl or conc. NH4OH to attain pH=4.2. This test required daily.
7)Non-volatiles not to exceed 1% or 2% on a dry weight basis as measured by AA. These being mainly sodium chloride and potassium chloride that may come from flux supplier.
8)Flux solution temperature. This is difficult in pipes galvanizing. Larger diameter pipes can use higher flux temperature. Smaller diameter pipes that are on the "breaking table" longer require lower temperature flux so as to not corrode and "spoil" before galvanizing. Thus the first half of the pipe bundle galvanizes fine but the second half is all rejects.
Pipe galvanizing is my favorite although it is about 20 times more difficult than general galvanizing. Also the equipment must be proper. Your double salt, when you first used it, had an ACN of 0.8. When refluxing rejects, zinc is dissolved from the rejects
(increasing zinc chloride in the flux solution) so your ACN goes down. You are likely low in ACN and you likely need to add some ammonium chloride to improve your galvanizing. You must not add too much ammonium chloride or your flux will be unstable to preheating.
The best results are obtained using "walking-beam" pipe transfer
(rather than "end-on" transfer). Screw pipe entry using ventilated, progressive screws work best. A steam accumulator near the blow head increases the power delivery over a shorter time to give thinner, smoother i.d. coatings. In South Africa and southern India the best results were obtained using quadraflux with an ACN=1.6. Also the baumé of the flux was quite low. Only mild preheating (drying) is used. By these flux modifications zinc usage was reduced 15% to 40% and the product was much, much better with only 1 or 2 pipe rejects/10,000 (from a bent tube). Other technologies can reduce zinc usage an additional 10% to 30%, depending on the required zinc on the pipes.
In North America, I believe the copper sulphate
⇦ this on
eBay or
Amazon [affil links] test is no longer used. Magnetic zinc thickness gauges are used for the o.d. and strip and weigh tests are used for the i.d. You should do profile i.d. testing along the length of the pipe at about 1 meter spaces.
>From about 1974 to about 2005, I published about 30 articles on hot dip galvanizing, mostly in Metal Finishing. I suggest you go to a large library and obtain these articles through interlibrary loan.
I do not like 47 deg. Be' double salt for pipes galvanizing. The i.d. zinc coatings will be thick and rough. The pipes try to float and come back up after initial immersion. Zinc usage will be very, very high and the money loss is also very high.
Regards,
Galvanizing Consultant - Hot Springs, South Dakota, USA

Q, A, or Comment on THIS thread -or- Start a NEW Thread