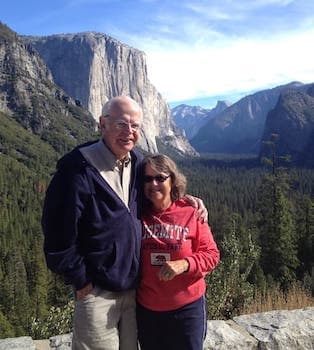
Curated with aloha by
Ted Mooney, P.E. RET
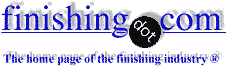
The authoritative public forum
for Metal Finishing 1989-2025
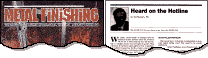
-----
Dissolving aluminum with caustic soda
Q. Hello everyone, I require assistance with an idea I have with caustic soda ⇦liquid caustic soda in bulk on
Amazon [affil link]
. My company currently has a process in which we submerge a steel diecast in a caustic soda bath to eat away melted aluminum. I have been given the task of improving our current process.
Current Process: 2/3 Caustic soda sits in an immersion tank heated to 80 °C. The diecast is set into the bath for about 24 hours and then washed with fresh water. We are overkilling this process based on everything I have read in this feed and others.
Process Improvement Idea: External heating system with a pump that continually circulates caustic soda to add some agitation and reduce sludge buildup inside the immersion tank. I would have a filter after the tank to catch the sludge before the soda was returned to the heating chambers.
My question: Do you think this will work? What flow rate might work? What microfilter would anyone suggest?
Thank you for any help.
- Huntington Beach, California
October 24, 2023
A. Hi.
I think it will work, but make sure to specify "all-iron" pump or lined materials because caustic soda will ruin bronze and brass. There are small venturi "eductor" nozzles
⇦ this on
eBay
or
Amazon [affil links] you can buy which screw into holes in a pipe to make a sparger system for better agitation, probably best pointed at the components you are treating.
Without knowing how many parts you process or how big they are, it's hard to suggest a pump and filter size, so maybe work backwards from the eductor nozzle capacities.
I don't think the micron size of the filter will be critical, but easy cleaning will be because this process builds nasty sludges that turn rock hard. If the solution cools itself a bit at and before the filter it will probably improve the filtration.
But before you get carried away you might investigate a proprietary aluminum etch process in lieu of straight caustic soda. They add sodium gluconate and/or other materials which make for more efficient dissolution and suspension of the aluminum.
Luck & Regards,
Ted Mooney, P.E. RET
Striving to live Aloha
finishing.com - Pine Beach, New Jersey
Q. I am trying to see if it possible to remove Aluminum that was rubbed onto glass, by either dissolving it or some other method. If so, how and what products might I need? Thank You for any response you might have.
J Casper- Fresno, California, USA
2002
A. Aluminium is soluble in caustic solutions. Try a warm solution of sodium hydroxide ⇦liquid caustic soda in bulk on
Amazon [affil link]
, strength - 40 g/l. If this is not effective then double the strength. But, watch out for etching of the glass which can happen if the solution is too strong or left on the glass for a long time.
Good luck.
- Melbourne, Victoria, Australia
A. With proper safety precautions use Easy Off ⇦ this on eBay or Amazon [affil links] Should be alkaline enough to dissolve Al.
Jon Quirt- Fridley, Minnesota
2002
Q. Does anyone know what concentration NaOH in a caustic/water solution results in the greatest rate of dissolution of aluminium?
We currently use 25% NaOH to dissolve aluminium from extrusion dies but I have heard of some extrusion companies using 20% and others using up to 30%. What is the optimum concentration?
Jim Pejoskialuminium - Canning Vale, Western Australia
2002
A. I think that you left out two very important parts, Temperature and Agitation. Typical with many chemical processes, a 20 °F or 10 °C temp increase will double the rate of reaction. Stripping aluminum forms a gel like hydroxide coating that must be removed for fresh lye solution to get to it. Outgassing does part of that. A 20 °F temp rise and a doubling of the agitation should allow the use of 20% lye. Cost effective and safer.
James Watts- Navarre, Florida
Where is all the NaOH going?
Q. We are an electroforming job shop. most of our parts are produced on 6061 aluminum mandrels which we dissolve with NaOH (caustic). For years and years we have done this in a 100 gal steel tank heated with a gas burner.
The concentration has been by "eye", starting with 2 5-gallon buckets of caustic beads [caustic soda beads in bulk on
Amazon [affil links]
and adding some more as we go depending on how much aluminum we've dissolved. We can typically dissolve about 50 lbs of aluminum this way before the bath is dumped and the sludge shoveled out. The problem is that now we have added a 300-gal tank for a specific job an we can't seem to dissolve more than a couple of pounds of aluminum without the bath going "dead".
I just put a part in that tank that typically would completely dissolve in the smaller tank over night. It was barely etched. We also are getting a white film on the parts and a thick white build up on the drive chain for the agitator (these parts are rotated on a frame under the solution).
We lose a lot of solution over night due to evaporation, (as much as 50 gal). The tank is refilled every morning and topped off at the end of the day (water only).
I guess my question is, is there an easy (we've got rid of our chemist) way to test for the amount of free caustic in the bath?
(please be very specific thanks).
Where is all the NaOH going. I would suspect that if it were getting carried out with the steam that the whole area would be white by now (it's not) Can a bath like this be run too hot?
- Brookfield, Connecticut
2006
A. Are you sure you thought of all the differences between the 100 and 300 tank? Come back to us with more information, and consider that Sodium Hydroxide heated (with steam) will turn to sodium carbonate.
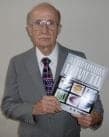
Robert H Probert
Robert H Probert Technical Services

Garner, North Carolina
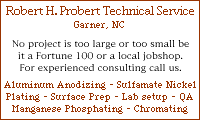
A. Tracy
It's a pity you got rid of your chemist as perhaps he could help you solve this problem. Was it a cost cutting program - if so perhaps you let go the wrong person. I am worried you are losing up to 50 gallons of bath each night - this must be costing a fortune in heating costs. What is wrong with covering the tank and adding insulation to preserve any heat you have in the tank? Such losses suggest to me you have a high tank surface area, which indicates there could be carbon dioxide absorption by your caustic tank - this will result in a loss of sodium hydroxide to sodium carbonate. Secondly, you do not say what your new tank is made from - if it reacts with sodium hydroxide, one day you will find the contents all over the floor. thirdly, to determine the amount of sodium hydroxide you have, just titrate the bath against a standard strength (say 0.5 or 1N HCl ⇦ this on
Amazon [affil links]
using methyl orange
⇦ this on
eBay or
Amazon [affil links]
indicator; this is basic schoolboy chemistry and isn't difficult. The math is simple; just remember that 1 mole of sodium hydroxide reacts with 1 mole of hydrochloric acid. Good luck and Merry Christmas
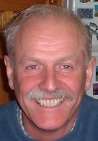
Trevor Crichton
R&D practical scientist
Chesham, Bucks, UK
Q. The tank is covered and insulated and made of cold rolled steel. The working theory based on the comments so far is that the burner we are using is heating too small an area and may be creating super heated steam at the bottom of the tank. I'm looking for another burner or a diffuser to spread out the heat. Thanks for the test info as well.
By the way. We we've been experiencing this problem since before we let our chemist go. I guess if it is so simple and he couldn't figure it out it's a good thing he's gone.
Tracy Yoho [returning]- Brookfield, Connecticut, USA
A. Tracy,
You did not mention about increased addition of caustic soda (Sodium Hydroxide) when you increased the volume to 300 gal. You do not have the same solution concentration or strength, you diluted your solution 3 times. Add more caustic bead at same ratio as the 100 gal tank.
If you use 2 x 5 gallon bucket for 100 gal tank, use 6 x 5 gallon bucket for 300 gal. tank for the same concentration.
good luck.
- Mays Landing, New Jersey
2006
Q. No, we scaled everything. The starting concentration should be the same (used 6 buckets/300gal)
We did use additional NaOH to keep the starting concentration the same.
- Brookfield, Connecticut, USA
2007
? Tracey, what is the surface area of your two tanks? I am not convinced about superheated steam because to get it, you need to use high pressure and I cannot see how steam will destroy sodium hydroxide, but perhaps I am missing something there. I am now very concerned that you are losing up to 50 gallons a night, despite the tank being covered. This is one sixth of the tank volume. Perhaps if you can find where this volume is going, you may find your missing sodium hydroxide. One thought -- do you make up the tank with water or fresh caustic solution? If you are losing solution by a leak, then making it up with water will dilute the caustic, but if it is purely evaporative losses, then it will be just water and the caustic concentration of the bath will increase overnight and before it is remade to the correct volume - check that out and get back to us. If it is evaporative loss, you are also potentially absorbing a lot of CO2, which will react with the caustic to form sodium carbonate.
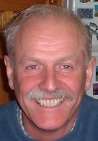
Trevor Crichton
R&D practical scientist
Chesham, Bucks, UK
A. Tracy,
That is baffling. In time like this, let us start from day one.
What are the inside dimensions of the 100 gal tank LxWxD.What is the height of the liquid.
Do the same thing with the 300 gal Tank. Include the height of the liquid.
I will double check the volumes, just in case.
- Mays Landing, New Jersey
A. Perhaps zinc contamination converted the etch to zincate solution. Was galvanized steel used for the tank? Any zinc mandrels used in electroforming?
Have a lab do an analysis.
Also, it seems temperature controls are lacking.
- Goleta, California

Rest in peace, Ken. Thank you for your hard work which the finishing world, and we at finishing.com, continue to benefit from.
Alternatives to caustic for removing aluminum from stainless steel
Q. Recently I have been put in charge of hazardous waste disposal at our facility where we coat plastic substrates with aluminum and stainless steel. Our engineering department has looked at, on and off again, a better method of removing aluminum build up from our tooling. Since we use a variety of technologies, all vacuum based, to apply the aluminum it coats everything. All of our systems are designed to break down so that cleaning can be performed.
Currently we are using a caustic soda bath to clean our stainless steel vacuum chamber components and stainless steel tooling fixtures. We run this bath at a pH of between 10 and 12, at a temperature of about 80 °C. This cleans most tooling in about 90 minutes depending on the thickness of coating and the freshness of our caustic solution. I've looked around and most everything I've found says this is the most effective way to attack this situation, but there has got to be another way. Dealing with this highly corrosive solution is a hazard in itself. We've tried neutralizing the solution, but this is expensive, and potentially volatile if not properly controlled. We've conceded to shipping the water out "as is" to our TSDF. Is there another method being used in the industry that would remove the aluminum build up, without damaging the stainless, that is less hazardous? I would be willing to sacrifice some of the efficiency for a safer, less hazardous solution.
Nicholas BoyceEnvironmental Tech. for coatings - London, Ohio
2007
A. While it might be interesting to investigate mechanical removal of the aluminum with a soda blast, dry ice, or other non aggressive blasting media, Nicholas, I don't think you'll find it practical. You're trying to remove a very adherent solid metal, so don't be disappointed that it requires strong chemistry. Alkali is safer for the stainless than acid, and is very widely used to dissolve aluminum, although proprietary etches might enable you to somewhat reduce the temperature or NaOH concentration.
Sure, caustic soda is a "hazardous chemical" to be handled with respect ... but let's not let chemophobia overwhelm common sense:
Drano, Liquid Plumber, and Red Devil Lye are essentially pure NaOH or KOH and enticingly displayed to the totally untrained consumer in every supermarket & every hardware store. Oven cleaner, a similar caustic, comes in aerosol spray cans and children, who might think it funny to spray it, are not even "proofed" to buy it. I do not believe that a properly trained & dressed employee, working with proper equipment for caustic dissolution, is facing any more danger than the average industrial employee :-)
Surely every doctor, nurse, dentist, and dental hygienist faces far graver dangers every single day. And the same can be said for countless other professions.
Good luck.
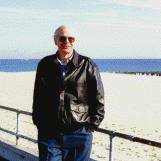
Ted Mooney, P.E.
Striving to live Aloha
finishing.com - Pine Beach, New Jersey
A. In the dark ages, we covered every part that we could with aluminum foil which we sold for scrap aluminum and recovered the parts. For the rest, caustic soda is the only affordable way to do the deed.
James Watts- Navarre, Florida
Caustic cleaning to remove aluminum from stainless steel
Q. I work for a company that uses vacuum metallizing to coat plastic substrate with aluminum. Aluminum books up on the tooling pretty fast, and the tooling then has to be placed in a NaOH bath at 135 °F. When all of the Al is removed from the steel, it has a brown residue on it which usually has to be scrubbed off using water and alcohol. Even after scrubbing to remove the residue, a white powder substance is still left on the steel. I'm thinking it is NaOH but I would think it should be removed when scrubbing with water. Anyone out there experience this issue? Would using a water softener for the rinse help? Maybe try using ethanol or methanol [affil links]?
Eric boydtooling technician - usa
August 22, 2015
Q. Question Eric? What did you find out? I have the same issue at times.
EC Cox- Flora, Illinois
September 14, 2023
A. Hi EC,
Eric's posting is from 8 years ago, but we'll try to contact him for an update.
Meanwhile, I think Eric was on generally the right track that the precipitate is from the NaOH either reacting with hard water or with the aluminum to create some insoluble aluminum reaction product. In either case I think the answer is probably to add a complexing agent like sodium gluconate to the mix. Proprietary etching agents, rather than straight NaOH, may solve the problem without requiring a lot of experimentation.
Luck & Regards,
Ted Mooney, P.E. RET
Striving to live Aloha
finishing.com - Pine Beach, New Jersey
I will try this for sure. I do hope that he will reply to his question. He's possibly retired as well.
Thank you sir and enjoy your retirement!
- Flora, Illinois
September 15, 2023
Q. Hi guys,
Stumbled onto this board and understand this is not strictly a "finishing" question. But I think the process may be similar enough to maybe steer me in a direction.
I work at a small aluminum manufacturing plant that produces seamless aluminum tubing. We use a site-made sodium hydroxide solution (10-15%) in a boil out tank to remove aluminum residue from our steel tooling and to do sample etching as well. We used to use a nitrate/nitrite based additive to extend the life of the caustic solution. That product has become unavailable. We are using straight sodium hydroxide now and only get about 3 weeks of usability per 100 gallon batch. We used to get almost 2 months with the additive.
My question is this: Is there an additive that will increase the efficacy and extend the life of our caustic for this tooling boil out process?
- Richland, Washington
March 28, 2022
A. If your problem is aluminum hydroxide precipitation in the pickling tank, then among the available ways to prevent its formation, there is a way to introduce additives such as sodium gluconate in an amount of 3% by weight of sodium hydroxide.
We also use commercial additives to the sodium hydroxide solution, which prevent the formation of sediment and do not require heating the solution and do not over-etch the products.
- Nizhniy Novgorod, Russia
A. Your last answer was correct. Use a chelate such as gluconate or EDTA. It should extend the life, but may add problems in the effluent to the drain.
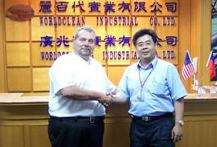
Drew Nosti, CEF
Anodize USA

Ladson, South Carolina
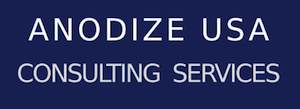
A. You must use sequestering agents in order to prevent precipitation of aluminium hydroxide such as sodium gluconate, sorbitol. Also you can add sodium nitrate ⇦ this on Amazon [affil link] /nitrite as well (nitrate/nitrite cause less slow reaction during etching).
Alaattin Tuna- Sakarya TURKEY
Q, A, or Comment on THIS thread -or- Start a NEW Thread