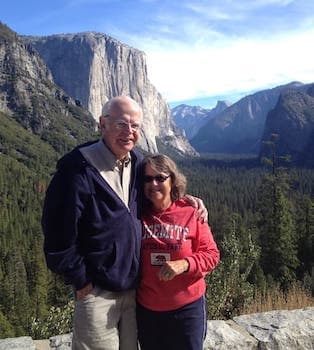
Curated with aloha by
Ted Mooney, P.E. RET
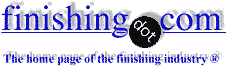
The authoritative public forum
for Metal Finishing 1989-2025
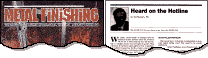
-----
Choosing between Phosphating methods
2007
We are manufacturers of machine tools. We are setting up a pretreatment and powder coating plant for processing of our machine guards made of 3mm mild steel sheets.
I would like to know , which phosphating methods out of the three should we design our pretreatment system for:
1. Hot di-cationic process(70 degC)
2. Low di-cationic process (25-30 deg C)
3. Tri-cationinc process (30 deg C)
Regards
Kapil Dhand
Own factory - Ghaziabad, UP & India
Dear Mr. Dhand
Go for Tri-cation Zinc Phosphate, this is the best process and is widely used in India.
It has less processing time and saves energy.
Best Regards,
- New Delhi
2007
2007
Dear Mr. Kanaujia,
thanks for the reply,
In case we go for tri-cationic zinc phosphate,
1.At what temperature should we do the phosphating?
2. What kind of agitation should we do
a) air agitation, or
b) recirculation using pumps
- India
Good Day
My Dear the suitable way for your application the third one you will take Excellent Quality
- U.A.E, Ajman
February 11, 2008
Q, A, or Comment on THIS thread -or- Start a NEW Thread