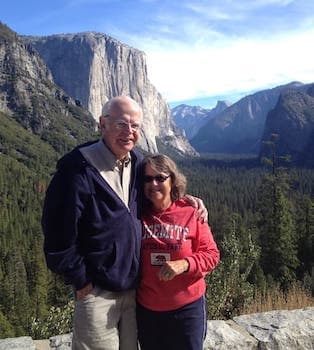
Curated with aloha by
Ted Mooney, P.E. RET
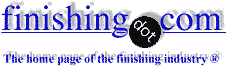
The authoritative public forum
for Metal Finishing 1989-2025
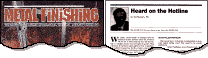
-----
Nickel Plating of Cast Iron Brake Rotor
I have a pair of old and out of production brake rotors that are worn. Replacements are not available. Is it possible to nickel plate 0.020 /side to restore these rotors? They are subject to pad wear and high temperatures in use of course.
Pat McGuireHobbyist - St Paul, MN, USA
2007
Yes, it's possible, although the plating will not be uniform and will require machining to bring the sides back to parallel. It won't be cheap. The coefficient of friction will be different too. Would it not be simpler to just have a machine shop replace the worn section?
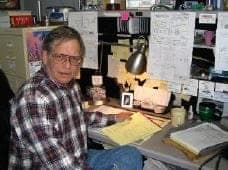
Jeffrey Holmes, CEF
Spartanburg, South Carolina
2007
In my opinion it's better, safer and less expensive to have them argon welded (incidentally, almost pure nickel rods are used for welding cast iron). Then machine back to whatever size is best (more than 0.020" if desired). This is the method used to restore broken or worn engine blocks. The friction coefficient will change somewhat. It may prove to be difficult to compensate this, but perhaps combining a different set of suitable pads in the other wheels or welding all four discs will help.
Guillermo MarrufoMonterrey, NL, Mexico
2007
On a brake rotor, I strongly advise against any welding of any kind. And I cannot see how part of a brake rotor could be replaced.
If they are old, they are probably flake graphite (grey) iron, which for that application is now almost entirely superseded by compacted graphite iron (well proven for many years in the extreme service conditions of railway disc brakes and truck drum and disc brakes). Some brake rotors were also made in spheroidal graphite iron, although that has been shown not to be a good choice for this application.
You need to locate a small, technically competent iron foundry (I am led to believe by the trade press that the larger USA foundries will only handle production runs of hundreds or thousands and are not interested in jobbing work, only production-line stuff). Depending on the geometry of your rotor, it might be able to be padded to use directly as a pattern, or a new wooden pattern might have to be made. You can then have new rotors cast.
Either have the foundry determine the type of iron in your old rotors and duplicate it, or else have the new ones cast in pearlitic compacted graphite iron so that it doesn't matter what the old ones are because the material of the new ones will be as good as, or better than, the old ones.
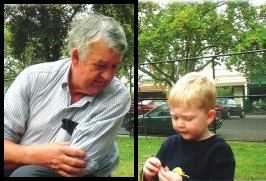
Bill Reynolds [deceased]
consultant metallurgist - Ballarat, Victoria, Australia
We sadly relate the news that Bill passed away on Jan. 29, 2010.
2007
First of two simultaneous responses -- 2007
Bill Reynolds -
"On a brake rotor, I strongly advise against any welding of any kind. And I cannot see how part of a brake rotor could be replaced."
If it's a old rotor, I'm guessing it's a simple solid, unvented rotor.
The worn portion of a rotor is the simple flat disc area. Certainly that could be machined off, saving the hub, and a new flat disc could be fabricated, possibly by machining the hub out of a new, similarly sized and inexpensive available rotor. I've done this sort of salvage for unavailable sprockets, salvaging the old and NLA hub, welded into the center of a generic sprocket.
No, they weren't cast iron, and maybe you know something I haven't thought of, but I don't see any reason the new disc section couldn't be welded to the old hub.
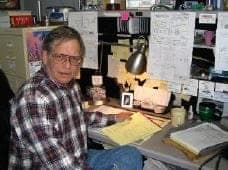
Jeffrey Holmes, CEF
Spartanburg, South Carolina
Second of two simultaneous responses --
Mr. Reynolds,
I understand your point. The welding process is plagued of stories of dismal failures and, indeed, things can go wrong. But on the other hand, things can go wrong with castings too, can't they? Extensive and expensive quality assurement and control practices applied by OEM's assists this. I used to work buying castings for one of the world's largest tractor manufacturers and I remember the specifications and testing to be mind boggling. The lot sampling was the highest and so were the rejects. An important percentage of parts that had already passed QC broke during our processing before being put into service.
I guess bottom line is low volume and budget and a critical item are a bad combination for safety.
Regards,
Monterrey, NL, Mexico
2007
Q, A, or Comment on THIS thread -or- Start a NEW Thread