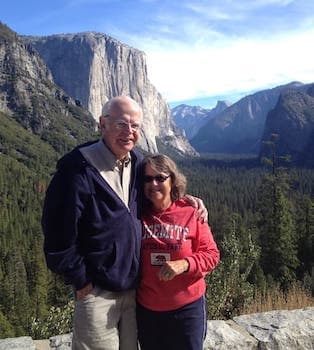
Curated with aloha by
Ted Mooney, P.E. RET
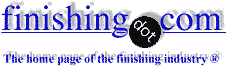
The authoritative public forum
for Metal Finishing 1989-2025
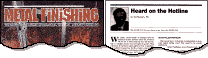
-----
Anodizing over nitrile
I have been trying to hardcoat anodize over a valve part made of 6051-T6511 aluminum that has a nitrile seal molded to the aluminum. 10 samples were sent to one anodizer and 4 returned (that seemed to be working fine). They said the other parts burned up. How can 4 parts come out ok and 6 parts burn up (they would not send me the burned parts). A second batch of smaller parts were sent to another anodizer and the nitrile seals fell out. This would usually happen if high heat was encountered. We are only putting on a very light skin .0002-.0008 and then a black finish to allow us to color code from non-anodized.
Norbert Kotvalve designer - Elm Grove, Wisconsin
2007
First of two simultaneous responses --
I've been anodizing for 4 decades and I'm not sure that I could take a unusual application that I haven't previously encountered, such as Nitrile seal molded in an aluminum part, and assure that it would come out with 100% success on the first try. Did your first anodizer try a conventional approach in which 6 burnt up or were otherwise destroyed? If so, the fact that he got 4 good ones might mean the next try he'd be a lot closer to 100%. Next, anodizing uses sulfuric acid which you can't escape but there are several options available in cleaning, deoxidizing and etching in preparing the part prior to anodizing. For instance, cleaners can be alkaline or acid, etches hot caustic or nitric acid or chromic acid based, etc. It may just be the pretreatment cycle itself that is attacking the seals. I looked up the chemical resistance of Nitrile and depending on the specific source of information, even sulfuric acid might be the cause of your troubles. If you're talking about 380 diecast molded parts, they really are difficult to hardcoat with or without Nitrile seals in them! It may have more to do with the alloy than with the fact that they have a seal molded into them!
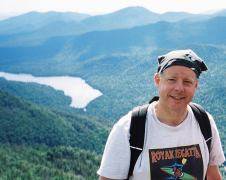
Milt Stevenson, Jr.
Syracuse, New York
2007
Second of two simultaneous responses --
The typical process conditions and chemicals involved should not attack the nitrile. Depending upon the design of the valve, thermal expansion differences between the Al and nitrile could have result in the nitrile separating from the Al. If the nitrile is molded around the Al thermal expansion differences would not have caused the problem. If the nitrile is in the shape of a washer inside of an Al cavity, thermal expansion differences could be the cause. I would have to see the design of the part to determine if the failures were caused by thermal expansion differences.
Along these lines, if a small amount of anodization solution can get behind the nitrile the contact area (adhesion) between the nitrile and Al would be decreased assisting a thermal expansion mechanism.
- Webster, Texas
2007
Q, A, or Comment on THIS thread -or- Start a NEW Thread