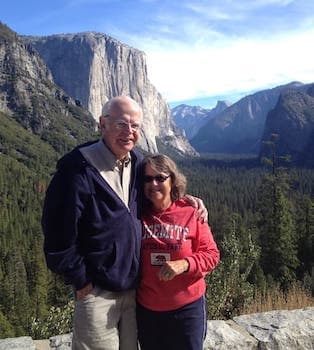
Curated with aloha by
Ted Mooney, P.E. RET
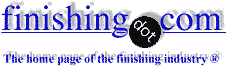
The authoritative public forum
for Metal Finishing 1989-2025
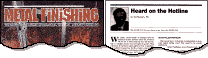
-----
Hot dip galvanizing adhesion superior to electroplate?
Q. I am being asked to comment on an article on hot dip galvanizing. The writer claims that the adhesion of hot dip coatings is superior to electroplated coatings and refers to hot dip following metallurgical laws that make it superior. Electroplated coatings are dismissed as having "surface adhesion" only, whatever that may be. I was taught that the adhesion of electroplated deposits relies on the principle of diffusion with some of the deposit diffusing into the substrate and vice-versa. How does this differ from the "metallurgical" bonding that hot-dippers cite as one of the reasons for their superior product and should this give platers an inferiority complex?
Tony van der SpuyConsultant - Training - Cape Town, South Africa
2007
A. There is a lot to be said for galvanizing but "superior adhesion" over electroplating is not one of those things :-)
Although there may be adhesion problems with specific lots from either technology, the adhesion can also be fabulous. Many electroplated coatings exhibit "perfect adhesion", i.e., it is impossible to separate them at the interface even with a carefully engineered tensile "pull" test like the Ollard test (described in letter 18002); instead, the object fails by either the coating or the substrate ripping apart in tension. This is obviously not "surface adhesion".
Maybe your writer meant to say that "galvanizing is superior to painting because painting offers only 'surface adhesion' " :-)
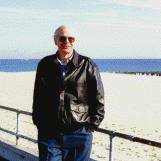
Ted Mooney, P.E.
Striving to live Aloha
finishing.com - Pine Beach, New Jersey
2007
A. The adhesion of HDG to steel is not such a common subject. Mostly as it's rarely a problem.
The zinc in HDG alloys to the steel, with, yes, a diffusion of the zinc into the iron and vice versa.
This is a strong adhesion, but the zinc layer is actually several layers, of differing composition. There are several alloys of Zn/Fe, with varying contents of Zn. On the surface usually pure Zn, and the substrate "pure" Fe (actually a mixture containing Fe, C, Si, Mn etc). In between these layers, the alloy layers, but these can sometimes, under certain conditions, be pulled apart.
I'd guess there would not be much to compare in the adhesion of electroplated and HDG - about the same.
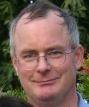
Geoff Crowley
Crithwood Ltd.
Westfield, Scotland, UK
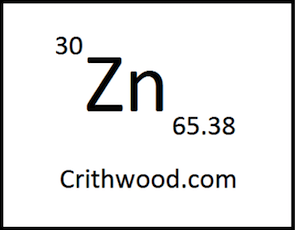
2007
2007
Q. In response to my query on adhesion Geoff Crowley confirms that the zinc in HDG alloys to the steel with a diffusion of the zinc into the iron and vice versa.
I need confirmation that diffusion is responsible for the good bond achieved in electroplated zinc finishes as well, unless this is not the case.
- Cape Town, South Africa
A. There are some electroplated coatings on some substrates which are heated for interdiffusion (like nickel plating on titanium). There are also some electroplated coatings that may eventually diffuse into some substrates (typically copper and the precious metals), but that's not generally the adhesion mechanism for electroplating. Rather, if I understand right, the plated metal is reduced right onto the substrate and therefore electrochemically grows onto it. This accounts both for the plating adhering to the substrate and for it adhering to itself. It also accounts for the internal stress that is found in most electroplating as the plated atoms unsuccessfully attempt to fit into the crystal lattice shape of the different metal of the substrate.
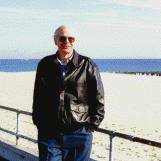
Ted Mooney, P.E.
Striving to live Aloha
finishing.com - Pine Beach, New Jersey
2007

Q, A, or Comment on THIS thread -or- Start a NEW Thread