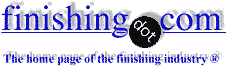
-----
Pits in Nickel/Gold Plating
Q. I recently purchased a rather expensive Gretsch guitar. It had all gold-plated hardware on it, i.e., tuning heads, pick-ups, knobs and a vibrato unit by a company called "Bigsby".
After a few weeks I started to notice some small tarnishing or pitting on the Bigsby. Then after I had the guitar for just 6 weeks I took it back to the shop where the guitar technician said this is quite common. The shop sent the guitar to the manufacturer's UK technicians at Fender UK who also said this is quite common and "perfectly natural" and that they wouldn't change the Bigsby or the guitar. What astonished me is that everybody seems to just accept that these Bigsby units pit and tarnish, but after just 6 weeks, this can't be right. Can you tell me if this is perfectly natural and common or is the gold-plating of the Bigsby flawed. Let me add that I did not put any polish on the guitar but cleaned it after every use with a very soft cloth.
hobbyist - Port Glasgow, Scotland
2005
2005
A. Certainly gold plating which does not deteriorate in a short time is something which is commonly done. Typically this might be a thin nickel underplate and 0.00005" or more gold.
The condition you describe may be typical for this manufacturer's work, but you can see gold plated costume jewelry everywhere which lasts for years.
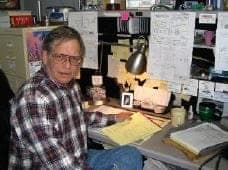
Jeffrey Holmes, CEF
Spartanburg, South Carolina
A. Usually those parts are nickel plated before the gold plating. Naturally the gold is thin and soft. But for it to start pitting makes me think there is little or no nickel underneath the gold. I have worked on guitar parts before and have found this to be the problem described. Take your parts to a reputable plater and get them done correctly.
Best regards, Frank
- St. Louis, Missouri, USA
2005
A. Thanks, Jeffrey & Frank.
Gordon, I bought a Gretsch Anniversary Model way back in college in the late 60's. Everything was all nickel plated and I kept it for 25 years with no tarnishing, and indeed there is nearly always nickel plating under the gold plating. If your complaint was that the gold was wearing off too fast, well, people do keep reducing the thickness of gold plating on things ... but if it was properly nickel plated (as Frank notes) it wouldn't pit regardless. The pitting indicates porosity in the nickel plating because it was improperly done (was probably too thin).
opinion ! Consumers: you have friends & supporters here rather than adversaries; we don't like it at all when shops cut corners and the plating is unsatisfactory. When plating is defective, it's defective regardless of what the manufacturer feels or claims! They get to choose whether to call what they sell you a 'manufacturing defect' vs. a 'design defect' or whatever -- but they don't get to decide that crappy plating is "perfectly natural" -- it absolutely is not :-)
Luck & Regards,
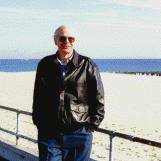
Ted Mooney, P.E.
Striving to live Aloha
finishing.com - Pine Beach, New Jersey
Multiple threads merged: please forgive chronology errors and repetition 🙂
Q. Hi to All,
We encountered PITS AND NODULES here in our plant although all the parameters are in the target range. We change our carbon filter every other day; we have air agitation in the line; we performed dummy plating before the production; we add wetting agent regularly (as per TDS); the bath concentrations are all in the target range (as per supplier or TDS specification) before the production proceeds.
The Hull Cell
⇦ huh?
test appearance has pits in the High Current Density. If we make some Hull Cell test labscales by adding wetting agent, the pits in the Hull Cell test was eliminated but when the production qualifies, the parts or the circuits HAD PITS.
Can anyone give some idea or suggestions how to eliminate or get free from the pits? How and where do the pits occur? Do pits and nodules have a relationship? Is there any prevention you can suggest to eliminate the pits aside from the above mentioned?
Regards,
engineer - Philippines
2007
A. Have you considered ditching the carbon filters? They'll remove the wetters, and may be a source of nodules if the filter quality is poor. You might try going to a plain polypropylene filter with no or removed sizing. Make sure that the filter is suitably fine for your operation ... I never used filters coarser than 10 micron absolute.
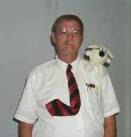
James Totter, CEF
- Tallahassee, Florida
2007
2007
A. Hello Joy,
Pitting can be caused by different factors. Usually caused by hydrogen gassing or oil / grease introduced to the solution, or poor cleaning. If it is a hydrogen gas bubble, the pit will usually have a tail (from the gassing). This is most noticeable in the high current density area. Certain measures can be taken.
1) Use an air blower, not compressed air for agitation. If compressed air, it should be oil free.
2) Check above the tank, make sure no grease or oil can drop into tank. Be sure no oil is floating on pre - plate tanks (drag-in possible).
3) Be sure anode bags are clean, come up above the solution level, and tied around the anode hooks.
4) If you are still using air agitation, check with your supplier to be sure you are using the proper wetting agent. The wetter varies from air agitation to solution agitation.
5) Investigate your cleaning cycle, do a water break test after cleaning.
Nodules are normally caused by poor filtration whereby particulate matter is suspended in solution. Nodules and pitting are not related.
It sounds like you are running a lot of carbon packs in the bath. Carbon polishing should only be done periodically. You could be filtering out an additive that you need. Good Luck!
Process Engineer - Syracuse, New York USA
A. Hi. Mark's advice is better than any I could give; I'd just add that 'gas pits' he mentions are invariably hemispherical and bright, which helps distinguish this problem from other causes.
Luck & Regards,
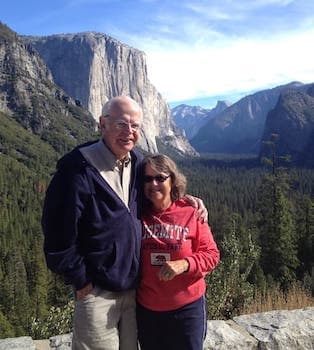
Ted Mooney, P.E. RET
Striving to live Aloha
finishing.com - Pine Beach, New Jersey
October 2020
Q. Hi Mark/James,
I have some follow up comments or conditions about this pits in nickel sulfamate plating line. What is the effect in the bath if addition of anti-pitting agent is in excess of required amount? Because during our lab-scale the amount required as per TDS is not enough to eliminate the pits in the line.
Do organic contaminants cause the pits? If any, what is the major one?
Regards and thank you,
- Philippines
2007
A. Joy,
The main cause of pitting is hydrogen gas adhering to the surface during plating.
Make sure you have adequate bath agitation, and are employing the proper current density. Also make sure the boric acid concentration is within range. Organic contamination generally is not the cause of pitting. Is your supplier helping you with this problem?
Process Engineer - Syracuse, New York
2007
2007
Q. Hi Mark
Thank you for the immediate response.
Yes, our supplier helps us in this pits issue.
Our boric acid concentration is on control range (43- 47 g/L), this was based on the supplier specs. Right now, we minimize the pits in the line, the adjustment we've done we've increased the agitation (FYI, we use mechanical agitation), increased the addition of anti-pitting agent (based on lab-scale) due to continuous carbon filtration.
Mark, as the result of our mapping, we have more pits on the bottom of the bath compare to the top (this was done without adding anti-pitting agents). By the way, the appearance of the pits is like shiny small circle.
We don't have acid cleaner because we're processing flextronics black cover coat ... is this ok? Continuous carbon filtration is our preventive action in cracking issue. What can you suggest?
- Philippines
![]() |
A. Joy, Process Engineer - Syracuse, New York 2007 A. Hi, - Mexico City, Mexico 2007 |
2007
Q. Hi Mark/James,
Until now we don't have any problem on the line and we already control the pits although sometimes it appears but we don't take it risk before we make action. We use 7 microns of carbon filter and the carbon polishing is now periodical (3x per week).
The big factor that I think was a big help for us your advice. Thank you for that!
What do you mean by adequate solution agitation? What particulate matter do you pointing out? Is there any way to determine the particulate matter? How does it occur?
In mechanical agitation, Can you please give me some advice, what required parameters can we use to improve our plating line (ex. Flowrate, power pump, etc.)
Again, thank you for your response.
Regards,
- Philippines
2007
A. Specific recommendations on filtration/mechanical agitation depend upon the physical plant as much as the process and parts involved. I still kind of think 3/week carbon polish is somewhat excessive, but that would depend upon exactly how you do it and how big the tank is, etc.
Some small rules of thumb I've used: You need to size pumps to provide about 4 tank turnovers per hour. I've generally used about a 3 cm stroke for mechanical part agitation, and sufficient air to raise the solution level 3 cm (air might/might not be appropriate, depends on the wetters).
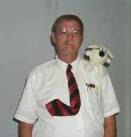
James Totter, CEF
- Tallahassee, Florida
A. I understand that without the Carbon filter, the plating parts will have crack issue which normally result from organic contamination. However, doing Carbon treatment will not only remove the contamination but also the wetting agent as well.
However, there is a carbon filter that removes organics selectively. It will only remove the contamination while still retain your wetting agent and brightener. This product is from Japan.
You can try to use the special carbon filter continuously to remove the organic contamination while still maintaining the additive and wetting agent. This filter works well with some products but you will need to test it out with yours.
Note that wetting agent only helps to prevent the pit issue, you will still need to consider the agitation and other factors too.
chemical supplier - Singapore
February 1, 2008
Skip to next posting on special carbon filters
Customer's gold plated wheels are pitting
Q. Hi,
I was wondering if somebody could please help. I have gold plated a set of car aluminium wheels for a customer. The customer is saying that they are starting to pit. The wheels came to me in chrome direct from the manufacturer. I took the chrome off to reveal the underlaying nickel, activated the nickel and plated them with 24kt gold. Now we believe the customer has used a caustic based chemical often used at car washes, on the car, but cannot prove this. I am just trying to find out if there is anything that could be wrong that I may have done to cause this problem. I have spoken to someone at the local plating shop who says gold does not pit and thinks it may be from the original plating from the manufacturer. Any advice would be greatly appreciated.
Many thanks
Lee
plating company director - Bolton, UK
March 20, 2009
![]() |
A. FLASH GOLD HAS NO PITS. ![]() Ajay Raina Ludhiana, Punjab, India March 21, 2009 A. The obvious question is - How thick is the gold? ![]() Geoff Smith Hampshire, England March 21, 2009 |
![]() |
A. It sounds as though the original nickel plating was not done well, probably too thin. Gold over nickel should last as well as the original chrome over nickel. ![]() Jeffrey Holmes, CEF Spartanburg, South Carolina March 22, 2009 A. Hey Geoff, - Mexico City, Mexico March 24, 2009 |
Back to previous postings on special carbon filters
Q. Hello.
This response (inquiry) is a bit late but here it is anyway.
Sir Robin Chua: Do you happen to know the maker of that carbon filter that selectively removes organic contamination only, and not the additives?
We're planning to set a frequency of carbon filtering our plating solution - was looking for ideas and found this thread.
All the best.
Semiconductors - Laguna, Philippines
December 10, 2009
December 11, 2009
Hi, Robin; hi, Melchor. Even better would be to get a patent number or an explanation of what they are claiming. Some brighteners are removed by conventional carbon filtration, some are not; some breakdown products are removed, some are not. It would be great to get a technical handle on what Robin is talking about here. Thanks!
Regards,
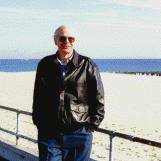
Ted Mooney, P.E.
Striving to live Aloha
finishing.com - Pine Beach, New Jersey
A. Hi Melchor,
This product is manufactured by Japan.
I am not too familiar of the theory of this specific cartridge but it is supposed to remove a specific range of organics. Although this product is designed to selectively remove organic contaminants, it will still remove some good organics (brightener) in your solution. This product is normally used only in the Nickel plating process.
Good Luck.
freelance advisor - Singapore
December 13, 2009
Q. Hi all,
Could anyone advise what is the defect and root cause for the pits found in Gold and Nickel plating, SEM images attached?
- Penang, Malaysia
October 9, 2020
A. Hi BC. I suppose that on some occasions SEM images can be helpful in diagnosing the cause of a plating problem, but my personal opinion of them is (as we say in the US idiom), often "you can't see the forest for the trees".
I don't know what the magnification is here because the photos are too small and low resolution to read the text, but I'm not even sure that what we see in the plan view indicates anything wrong. The cross-sectioned micrograph does seem to indicate that the top layer of plating has not filled all the crevices in the metal below it, but again, not knowing the magnification or what I'm looking at, it's hard for me to comment at all :-)
Hopefully, someone who spends a lot of time studying SEM images might be able to make more of them than I am able to, but what is the evidence that the plating is even defective? And if it is, I don't see how the SEMs tell us whether the problem was poor mechanical finishing, cleaning, activation, or what -- sorry.
What are you plating and why? What is the specified thickness of the nickel plating and of the gold? Thanks!
Luck & Regards,
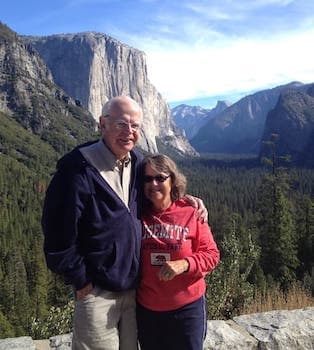
Ted Mooney, P.E. RET
Striving to live Aloha
finishing.com - Pine Beach, New Jersey
October 2020
Q, A, or Comment on THIS thread -or- Start a NEW Thread