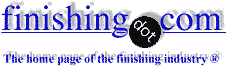
-----
Is stainless steel 18-8 passivation Rohs compliant?
Q. Rohs directive says that hexavalent chromium is prohibitied. This alloy has 18% chromium. I'm not a chemist but I need to know if my fasteners meet this directive. Please help.
Thanks
user - Milwaukee, WI
2007
A. "Hexavalent" means "in a +6 oxidation state", Richard. Metals, as metals, are at a zero oxidation state. Metals that are dissolved into acid can be at other oxidation states; salts of chromium can be at +6 or at some other oxidation states. At the trivalent state, +3, chromium is not restricted by RoHS.
It is very unlikely that a natural phenomena can convert the chromium in stainless steel into hexavalent chromium. chrome metal and stainless steel are not RoHS restricted.
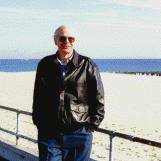
Ted Mooney, P.E.
Striving to live Aloha
finishing.com - Pine Beach, New Jersey
2007
2007
A. We may want to note that for some grades of stainless, a nitric passivation process requires the addition of hexavalent chrome in the form of sodium dichromate. I'm not entirely sure that RoHS applies even to that though since that chrome is used to oxidize the stainless surface, and does it itself form a coating on the parts.
However, citric acid passivation is completely free of hazardous chemicals.
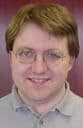
Ray Kremer
Stellar Solutions, Inc.

McHenry, Illinois
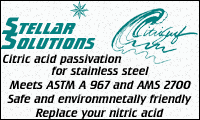
A. I agree that citric acid passivation is an environmentally friendly method of stainless steel passivation; however, with stainless steels (principally the austenitics) the passivation process is more of an aggressive clean to allow the self-healing protective oxide coating to form. Nitric and citric acid "passivation" does not form the passive layer itself and does not remain on the part so it is considered a manufacturing aid and not a finish coating.
Stainless steel will passivate just sitting on a shelf, but You need to a good clean surface for the SS to do this well. This is particularly necessary if the SS has come into contact with tool steel. Minute amounts of the iron/tool steel will transfer to the surface of the SS when in contact, and that iron contaminate will prevent the protective oxide from forming at that spot. The iron itself will either corrode away (creating a rainbow discoloration of Newtonian colors) or worse yet, allow that one spot to be a sacrificial cathode to the rest of the part, pitting aggressively. The acid bath removes the free iron from the surface.
- Carpentersville, Illinois, USA
September 4, 2013
Q, A, or Comment on THIS thread -or- Start a NEW Thread