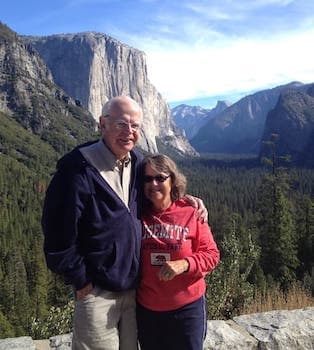
Curated with aloha by
Ted Mooney, P.E. RET
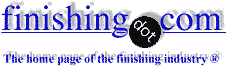
The authoritative public forum
for Metal Finishing 1989-2025
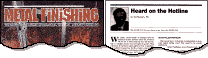
-----
Need a finish for 480 hour salt spray requirement
We have a standard from a prospective customer for a 480 hour salt spray. We have a couple of mild steel stampings that are currently plated Zn with yellow chromate for a 72 hour salt spray. We are looking for finish recommendations that will allow us to attain the 480 hours with no red rust. The parts will be used on the outside of trucks in Europe. Thanks.
Dick Winterproduct designer - Grand Rapids, Michigan
2007
First of three simultaneous responses --
High P electroless nickel should work as would a proper powder coat over a zinc phosphate undercoat.
James Watts- Navarre, Florida
2007
Second of three simultaneous responses -- 2007
Good afternoon:
With all the RoHS/ELV directives that came from Europe, the manufacturer may have specific approved suppliers of chemicals and/or applicators for the finish you're looking for. You may need to call the customer back and ask.
If not, several of the supporters of this website offer chemicals that will meet this salt spray requirement. Many of them use a silicate based seal over trivalent chromate.
- St Louis, Missouri
Third of three simultaneous responses --
Dear Dick,
My suggestion would be for you to send your untreated MS stampings out to a local powder coating shop. Check that they have zinc phosphating facilities and can bake your items so that the powder is fully cured to the correct gloss requirements. The specification you should ask for is - degrease; zinc phosphate; rinse etc; apply three mils polyester powder - colour to your specification (do not specify a colour that contains aluminium) and bake. The baking temperature should be in the order of 200 °C for the length of time for adequate curing takes place i.e. passes a cross hatch test. If handled correctly your items should pass 750 - 1000 hours ASTM B117.
Birmingham, United Kingdom
2007
Back in the mid-90's we were getting 500 hours on cast iron transmission parts, zinc plated, yellow chromate, then topped off with a proprietary silicate coating. We tested each batch with copper sulphate ⇦ this on eBay or Amazon [affil links] and when we found occasional failures it was due to low thickness in the low current density areas.
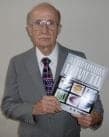
Robert H Probert
Robert H Probert Technical Services

Garner, North Carolina
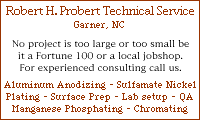
2007
2007
Howdy,
We are currently plating zinc on 1215 using trivalent chromate and an organic topcoat.
We also have Bob Probert's coating and it also works well. It's not impossible to do. Just requires a good process control
- Denver, Colorado
Q, A, or Comment on THIS thread -or- Start a NEW Thread