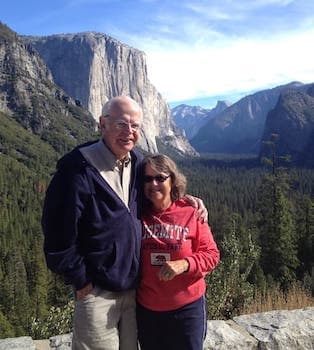
Curated with aloha by
Ted Mooney, P.E. RET
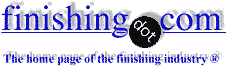
The authoritative public forum
for Metal Finishing 1989-2025
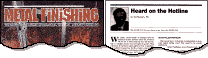
-----
Electroformed (nickel sulphamate) record stampers are breaking
2007
Q. Hi everyone,
'got some problems with electroplating process...
I have to develop stampers for record pressing plants.the problem is that now, all the stampers after having been detached from the
"mother stamper" break before putting it on presses...
Or just after having pressed a hundred discs, about 7-10 times less than in normal conditions....
I don't have any idea about what's happening with theses baths...
I've "cleaned" & filtered up the bathes with active carbon, during 48 hours in order to eliminate potentially metallic pollutions... without consequences...
Need your help guys...
Thanks by advance,
Nickel plating employee - Mouscron, Belgium
A. Either the nickel is too brittle or too stressed. What are your plating conditions and parameters?
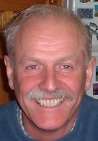
Trevor Crichton
R&D practical scientist
Chesham, Bucks, UK
2007
A. What's your chloride level?
High chlorides are a common source of stress in sulfamate nickels.
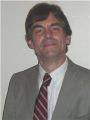
Dave Wichern
Consultant - The Bronx, New York
2007
Q. Hey guys, sorry for being late...
Since the first post, there was a change here.
In fact, the cause of broken stampers seemed to be chloride level...
So, we change our bath, and we replaced it to have "normal" conditions.
H3BO3 : 30g/L
NiCl2 : 4g/L
Sulfamate : 300 g/L
And the fact is that stampers are still breaking ! :s
No problems in traction/compression stresses, but problems with ductility... the extra-electroplated nickel we cut before forming our matrix breaks easily (after having bent 1-2 times)
Need you guys...
Thanks by advance
- Mouscron, BELGIUM
First of two simultaneous responses -- 2007
A. The chloride level looks reasonable to me - you don't want too much with sulphamate or it becomes brittle. The only good job chloride does is promote anodic dissolution, and if you use S-nickel, you don't need it at all (in theory!). What is your nickel hardness and full bath composition? What are the plating conditions (temperature, current density, pH etc)? Have you done a Hull Cell test for impurities? The problem could be due to hydrogen embrittlement, co-deposition of another metal or numerous other factors. The more detail we have, the easier we can help you.
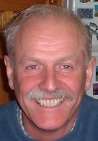
Trevor Crichton
R&D practical scientist
Chesham, Bucks, UK
Second of two simultaneous responses --
Stress and Ductility are two different things. If you suspect ductility as the problem, then get an ammonia ⇦ this on eBay or Amazon [affil links] ion analysis of the solution. ammonia comes in with low quality sulfamic acid, so check the incoming sulfamic acid for ammonia. ammonia is formed by too high temperature,and/or too high anode current density.
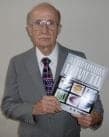
Robert H Probert
Robert H Probert Technical Services

Garner, North Carolina
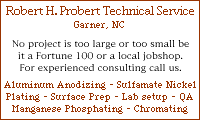
2007
A. It is a balancing act between hardness and brittleness. Hardness is desired to reduce wear on the stamper and if the hardness is too high the stamper becomes brittle.
you did not mention pH. Too high a pH can make the stamper brittle. Typically a pH near 4 is used as this keeps the stress near zero. You can also be incorporating a lot of sulfur from the stress reducer into the stamper. High current density dummying will reduce the amount of stress reducer in the bath.
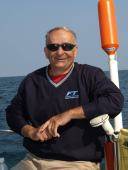
Pat Mentone
St Paul, Minnesota
Hi guys, thanks for your answers...
We finally found a solution for this problem of ductility...
First of all, when I answered back, telling the bath was changed, there was less than 2 days of homogenation of the products... 2 days after, ductility was better, but not satisfying yet.
And in another hand, the "moistening" (I'm not sure of the word) was not so good...
So we increased the Sodium laurylate (Duponol) Level, and this was the reason why matrix were breaking ! (lack of duponol)
It seems that this kind of chemical product is added in order to reduce hydrogen pits AND to increase ductility...thing we ignored...
So, thanks a lot for all your ideas and advices, but our problem is now resolved... :)
I wanted to mention here that Finishing.com is a very good website, trying to help everybody's problems, giving some advices by experimented professionals and not "students" pseudo-professionals as we can see in other websites. It must be noticed !
Thanks everybody, and keep up the good work!
DERNAUCOURT Jonathan- Mouscron, Belgium
Thanks for the feedback and the compliment, Jonathan. We do not discourage responses from students or pseudo-professionals, but we do hope that the questions receive enough exposure that someone can offer a really good answer. In this case you did receive responses from four true professionals and we thank them!
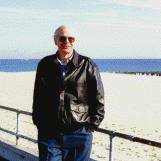
Ted Mooney, P.E.
Striving to live Aloha
finishing.com - Pine Beach, New Jersey
2007
A. I do not believe that adding more wetting agent increases ductility or reduces brittleness. This is most likely not the root cause of the problem.
Johnathon, What else did you do during the 2 days before the stampers became less brittle.
Was the bath just maintained at operating temp with filtration?
Did you carbon treat the bath?
Did you keep plating stampers and the quality gradually improved?
Were any chemistry changes made?
Did you dummy the bath?
What do the nickel plating experts think solved the problem?
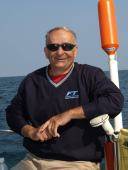
Pat Mentone
St Paul, Minnesota
A. Hi guys,
To answer your questions :
Was the bath just maintained at operating temp with filtration?
-> Yes, temperature maintained at 50°C and always filtered
Did you carbon treat the bath?
-> Active carbon was placed on filters during these two days
Did you keep plating stampers and the quality gradually improved?
-> We just let the bath filtering, no stampers were developed during 2 days
Were any chemistry changes made?
-> No changes were done in the chemical electrolyte, unless adding boric acid till obtain the pH desired
Did you dummy the bath?
-> Sorry I don't understand what dummy stands for... But I think I didn't... ;)
All we've done was simply let the bath filtered itself and keep the temperature about 50°C...I'm sure increase Laurylate sodium level had a benefic result on ductility, and this "idea" was confirmed by aplating specialist located here in Belgium...
Hope these answers to be helpful
Thanks,
- Mouscron, Belgium
A. Johnathon
thanks for the clarification. Just a couple of items
1. Boric acid is not used to adjust pH. The pH should be lowered with sulfamic acid and raised with either nickel carbonate or KOH.
2. Dummy plating is plating onto a sheet of metal that is folded to look like a washboard. it is folded so that there are both high and low current density areas on the same panel. The valleys will look dark if there is metallic contamination and the peaks will have pits if there is organic contamination. If the peaks and valleys on the dummy are identical then the bath is in good condition.
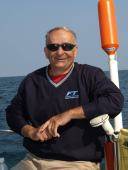
Pat Mentone
St Paul, Minnesota
2007
Q. Hi Guys,
I am looking for Nickel Sulphamate solution 11% for our new glass mastering system to make CD/DVD stampers.
Could anybody please inform what is the reliable source or supplier of this material?
Jonathan
Where do you get your Nickel Sulphamate from for your galvanics?
Thanks for your info.
- Jakarta, Indonesia
May 2, 2012
A. Hi Cokro.
We can't recommend specific brands. For one thing it sometimes results in a race to the bottom, with salespeople even posting with fictitious names, posing as satisfied customers :-)
If you are sure that simple nickel sulphamate will meet your needs, you can pick a reliable local commodity chemical supplier, but most platers are more comfortable getting the product from the established plating process suppliers. You can look in our Chemicals directory for these international suppliers, or you can simply look in your city for "Plating Chemical Distributors". Good luck.
Regards,
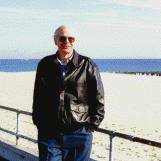
Ted Mooney, P.E.
Striving to live Aloha
finishing.com - Pine Beach, New Jersey
May 3, 2012
April 24, 2013
Q. Dear Sir,
we are making sugar sieves on S.S. Matrix. Our chemistry is Nickel Sulphamate--420 GPL
Nickel Chloride ---3.5 GPL
Boric Acid ---50 GPL
Surface tension ---27 Dyne/Cm
pH-----3.94
Since last two weeks we are facing the problem of foil peeloff from the panel before plating cycle. We have taken the given below actions but the problem is reming the same.
1. Already given the treatment with H2O2 & Carbon
2. Check the concentration of chemical and it is ok
3. Check the sulphate and remove by adding sulphate reducer & given the treatment
Now what may be the another reason for that ?
Kindly give your valuable suggestion
Best Regards,
Ajay
- Ahmedabad, Gujarat, India
Q, A, or Comment on THIS thread -or- Start a NEW Thread