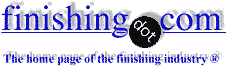
-----
Measurement of Acid Etch Coupons
2007
Many aerospace standards require the determination of acid etch of removal rate by the use of a test coupon. One standard states
"0.00004" ± 0.00001" of material per surface is removed as determined by a representative coupon".
My question is "What methods and equipment are required to measure such small increments on the test coupons? Is there a standard method?"
shop employee investigating acid etch processes - Statesville, North Carolina
First of three simultaneous responses --
It is normally done by weight loss. A panel is cleaned and dried, weighed at room temp, then processed as a part and then cleaned and dried and re-weighed. It normally requires a short bake at 110 °C and then cooled in a dessicator to have a reliable weight. I no longer have access to "industry" specs for the exact times and conversion factors.
James Watts- Navarre, Florida
2007
Second of three simultaneous responses --
Etch coupons long enough to get an accurate etch rate via micrometer.
If 20 minutes etching results in 0.0016" removal (both sides), then the etch rate is 0.0016" /20 minutes/2 sides = 0.00004" /minute/side. Adjust etch time accordingly for slower or faster rates. A relatively large etching solution volume helps ensure that the etch rate remains
~constant. Periodically, run additional test coupons, adding etching agent as necessary.
Rinse, dry & preserve test coupons as documentation.
- Goleta, California

Rest in peace, Ken. Thank you for your hard work which the finishing world, and we at finishing.com, continue to benefit from.
2007
Third of three simultaneous responses --
Sure. You weigh the coupons on an analytical balance. Metal is pretty heavy.
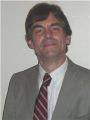
Dave Wichern
Consultant - The Bronx, New York
2007
First of two simultaneous responses -- 2007
Hi Brian,
You can start looking into
SAE ARP1755 document, which details the stock loss method.
- Mississauga, Canada
Second of two simultaneous responses -- 2007
Brian
Are you sure you have the correct number of decimal places? 0.000004" is 0.1 microns in real money. That is about a fifth of a wavelength of light.
When you have cleared that up; first forget micrometers. They are not acceptable to aerospace standards. At this accuracy, a micrometer bridges across the microscopic imperfections on the surface.
Take a piece of the same alloy as the job, you need C of C traceability. It should be flat, square and thin so that you can accurately get the surface area (both sides). If it is thick you must allow for the area of the sides. Clean and dry the part at 110 C. Weigh it accurately. You will need a lab balance accurate to at least
4 decimal places and calibrated. Raise a route card and process and record parameters exactly as you do for a part. Dry again at 110 °C and weigh. If you know the density of the alloy you can calculate the stock loss. Record all results and calculations. Most specs require a measurement at least each shift or before work is processed.
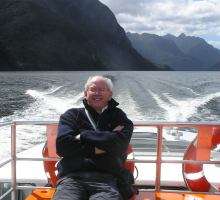
Geoff Smith
Hampshire, England
Yes, I am sure of my decimal places; I believe you added one more than I posted. Since I cleared this up per your request, I thank you for your input.
Brian Schoolcraft- Statesville, North Carolina
2007
2007
Brian
Quite right. I put it down to old age and a complete inability to count.
But
1/ It is a general principle of metrology that an instrument should have 10x better accuracy than the parameter measured.
2/ It shows the problem of using inches to measure very small dimensions.
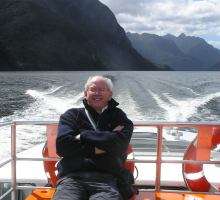
Geoff Smith
Hampshire, England
Welcome to the world of thin films! First thing that needs to be done is to have a coupon with a surface finish of < 2 microinches or 508 Angtroms or 0.0508 uM. This would be a surface that was specular or reflects light like a microscope slide or very polished metal.
Next, mask of a portion of the test coupon and proceed with your etching as usual which will produce a step. This step can then be measured using a surface profilometer such as the Sloan Dektak or KLA Tencor. These come in various models and can be found at semiconductor surplus shops or at thin film job shops. Many thin film vacuum plating shops use them as well for measuring electroplated microelectronic circuit traces. They are accurate down to about 50 Angtroms or 0.005 uM.
- Lompoc, California
2007
Q, A, or Comment on THIS thread -or- Start a NEW Thread