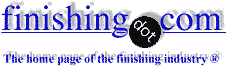
-----
Pull off problem while cobalt zinc plating
2007
Hi everyone,
We are processing a conical shape flange in cobalt zinc bath, the thickness requirement for outer diameter is min. 20 microns and for inside dia. it is 10-20 microns. The component needs to be olive green passivated. We observed pilling in outer diameter after a day or so. Is it the excess thickness, causing the problem? Electroplating time for the above component is half an hour.
Expecting valuable suggestions.
Thanking you.
Plating shop - Pune, India
2007
Hi Pawar,
Firstly I quote the portion of your query "the thickness requirement for outer diameter is min. 20 microns and for inside dia. it is 10-20 microns."
Generally Zinc plating required thickness is 8-12 microns. So I assume that inside dia. of your component is critical and need 10 Microns and by virtue of that you are bound to get 20 microns on the outer dia. in a standard Acid Chloride Zinc plating process.Boric acid based chemistry of Acid Chloride have the tendency to give less percentage of Cobalt in the deposit distributed all over and interestingly almost all being deposited on the High Current Density areas resulting in chip off beyond say 20 Microns.Also you need more of costly cobalt in ppm/ltr (up to 2000)in the bath.
There are options you may choose:
1.Why not a total chloride Acid chloride cobalt process! The advantage is that cobalt in the deposit will increase but that will be co deposited with Zinc uniformly and evenly all over in LCD and HCD and will have no Chip off problem. You may have less conc. of cobalt in the bath say 400-500ppm/ltr. I have experienced thickness up to 40 microns in HCD and still does not give chip off problem.
2.I do not know your customer requirement.If I was in your place I will ask my buyer and find out the possibility of processing this product in Alkaline cyanide Free Cobalt bath which may give you 10 microns in the inside dia. and up to 14-15 microns on the outside dia. and will not give a problem of chip off. Pawar, just imagine and work out the costly Zinc you sell if you adopt alkaline Zinc plating! But please sit with your buyer before doing So.
3.I read an article recently that some supply house is marketing an acid chloride Zinc plating process with a special additive which can give more or less even thickness in LCD:HCD.But may be this may take a while to be seen in working!
Try to post in more detailes..May be I can help you better.
Regards
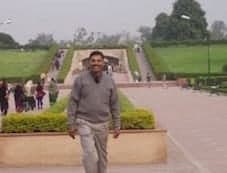
T.K. Mohan
plating process supplier - Mumbai, India
2007
Thank you Mr.Mohan,
Sir, we have already tried the component in alkaline zinc process, but the customer requirement of 20 microns thickness on the outer dia. and 10-15 microns thickness on the I.D. restrict us, as we got the uniform thickness between 12 to 17 microns on I.D. and O.D. by alkaline zinc process,which fails the requirement of 20 microns on O.D.
Sir, can you tell me more about Total chloride Acid Chloride Cobalt process ?
Will reducing the brighteners or etching with sulfuric acid
help me? I will try to explain what I have done so far;
Inner dia of the component is in three stages and to achieve the required thickness we introduced an auxilliary anode, which shows positive effect for thickness specifications on the first two inner diameters. During the process Third Inner Dia. shows thickness about
6-9 microns ,which is not acceptable. So, we mounted an extra ring anode to the zinc plate by reducing the distance between cathode and anode. Thus the required thickness achieved at the required areas, but the problem of pill up on outer dia. is consistent resulting in the rework of about 30%. Am I on the right track
Thanking you again and expecting your suggestions.
- Pune, Maharashtra, India
Rajendra,
A few more details on your process may help get a response. What are your pre-cleaning steps? When peeling from a base is a problem it can often be found to be something to do with the pre-cleaning.
What are your processing parameters for the plating (concentrations, temperature, current density etc.)? It may be that the chemistry is out of balance or that you are not operating at the optimum temperature.
And finally, if you can, can you provide any pictures of the problem? As they say "A picture speaks a thousand words".
Hopefully, if you provide this sort of information someone will be able to help you.
Aerospace - Yeovil, Somerset, UK
2007
2007
Hi Pawar,
30% rejection is really bad and do you still make profit or does your buyer give share of your loss!
Total chloride(no boric acid) chemistry gives you a more uniform cobalt distribution and may help you from flaking off from HCD as there will not be over build up of Cobalt in HSD.
As you have given more details about auxilliary anodes, is it inert anode like Ti wire or it Zinc metal itself?
Regards
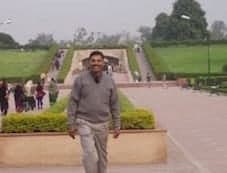
T.K. Mohan
plating process supplier - Mumbai, India
2007
Mr. Mohan,
We are using zinc wire of 4 mm. diameter.As per your advice consulting with the local suppliers about boric free chemistry.
Thanks.
- Pune
Q, A, or Comment on THIS thread -or- Start a NEW Thread