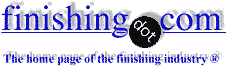
-----
To get mirror finish #1 / #2 finish in deep cavity
2007
Hello,
I am trying to achieve #1 / #2 finish. My company is producing Rubber V-Ring / O-ring parts.
Molds are manufactured from 4140 pre-hardened steel to 30 Rc. Our cavity are deep and narrow. All the parts are manufactured on lath.
It is very difficult to use stick because of problem of breaking edge and hard to reach areas. I have decided to use different compounds. So started with 320 grit Grease-based silicon carbide compound, followed by 600 grit Grease-based silicon carbide compound , followed by 1200 Grease-based silicon carbide compound.
Finally with diamond compound, green, orange & yellow. Unfortunately I am not able to remove some machining marks.
Can you tell me what is the best way to go for this?
Product Designer - Houston, Texas
First of four simultaneous responses --
Based on your vague description of the hole, I am going to assume that you can not get a hone that small. The next best operation would probably be a very careful grinding operation to get it to the point where you can polish it.
James Watts- Navarre, Florida
2007
Second of four simultaneous responses --
You need to start cutting in a different direction to the marks left by the lathe (preferably at a 90o angle). This means that you must not try to do it turning on the lathe. Make sure the first abrasive totally removes the machining marks. If not, maybe it's not coarse enough or you didn't give it enough time. Insist or go back and try with a coarser grain. Forget to go ahead. You will not remove them with the following finer abrasives. Then, proceed to the next abrasive cutting in another direction than just before. And so on with patience. What type of attachment and tools are you using to get into the grooves? What speed? Manual, rotary or reciprocating?
Guillermo MarrufoMonterrey, NL, Mexico
2007
Third of four simultaneous responses --
How deep is deep? There are some narrow non-woven sponge like pads out there that can be forced into narrow grooves and used like steel wool which another possibility.
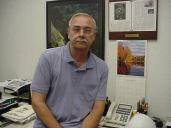
AF Kenton
retired business owner - Hatboro, Pennsylvania
2007
Fourth of four simultaneous responses -- 2007
Hello,
I cannot follow clear your system. It is well know that polishing is an "art" but also requires well-understanding of the mechanism. Several parameters affecting the right polishing. I would like to help you, but I would like to know more about your polishing method: rpm, time, shape, orientation, pressure.....
A solution as a function of your data: use only the YELLOW.
- Minneapolis, MN, USA
Q, A, or Comment on THIS thread -or- Start a NEW Thread