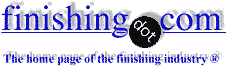
-----
Coating of aluminum injection mold tool
Is there a coating or finish which can be applied to an aluminum injection mold tool which is producing Class A paintable TPO components so to maintain the surface finish of the tool?
J Ritchieplastic process - Bracebridge, Canada
2007
There are at least four options, but in my opinion, because of its availability, safety, moderate cost and uniformity, the coating of choice would be electroless nickel (EN), medium or high phosphorous, 0.002-0.003" thick (measured after polishing). Its hardness would be around 46-48Rc as plated. If desired and permisible by the type of alloy and its metallurgical condition, it could be further hardened by a low temp bake to gain another 10 or more points. Another possibility would be a low phos EN which has a higher as plated hardness of around 64Rc (more expensive, less available, no bake needed). Hard anodizing though also possible, would require a thorough review of pros and cons because it will dissolve a certain amount of aluminum from the tool (0.001-0.002"). It also is not totally safe against processing errors and not too easy to bring to a bright mirror finish. In this case, every insert, plug, bolt or attached part made of a different metal would absolutely have to be removed before anodizing. Finnally, I would definitely not recommend hard chrome unless the geometry of your mold is very simple (no cavities, entrant angles and curves, slots, ribs, blind holes, etc.)
Guillermo MarrufoMonterrey, NL, Mexico
2007
Q, A, or Comment on THIS thread -or- Start a NEW Thread