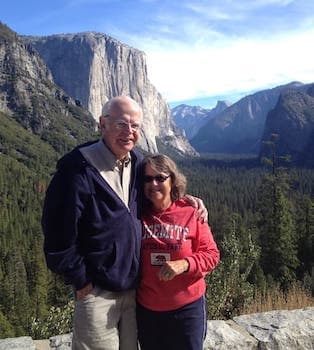
Curated with aloha by
Ted Mooney, P.E. RET
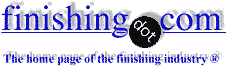
The authoritative public forum
for Metal Finishing 1989-2025
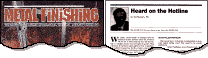
-----
Nickel acetate sealed part "weeping" yellow like liquid when heated to 250 degrees
We make parts that are anodized blue they are then sealed with Nickel Acetate. My customer glues something to the part and has recently been having trouble with adhesion. Their research has shown something odd. When the parts are heated in a 250 degree oven(no glue yet) a yellow substance "weeps" from the part. Parts that are cleaned with rubbing alcohol prior to the heating of the parts are okay and do not display this problem. Our anodizer suggests that they reduce the time in the seal bath from 10 minutes to 1. My customer wonders if we should avoid the seal altogether. Any thoughts on what the yellow is and how to avoid it.
John G. Smithscrew machine products manufacturer - Chicago, Illinois, USA
2007
First of three simultaneous responses --
Don't reduce sealing time - maybe even increase the sealing time or temperature. Properly sealed parts should be fine at 250 °F; in fact, most blue dyes (nickel acetate-sealed) are OK for 1 hour at
250 °C (482 °F) according to testing by Sandoz.
Use pH (litmus) paper to check the yellow liquid for acidity. Any welds, joints, casting porosity or cavities where anodizing electrolyte may be entrapped and then forced out by heating?
Look for contamination sources during shipping and storage. Also, check the furnace for organic contamination which may be condensing on the parts.
- Goleta, California

Rest in peace, Ken. Thank you for your hard work which the finishing world, and we at finishing.com, continue to benefit from.
2007
Second of three simultaneous responses --
What is the alloy? What is the iron contamination level in the anodizing solution? Do you use an "iron based" deox? Then how many rinses before anodizing? Was the commodity sulfuric acid brownish colored (Iron?)? Thickness? Sulfuric Acid strength in the anodizing solution? Dissolved aluminum? pH of Nickel Acetate Seal?
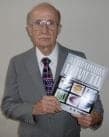
Robert H Probert
Robert H Probert Technical Services

Garner, North Carolina
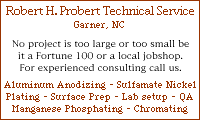
2007
Third of three simultaneous responses --
Couple of thoughts come to mind: (1) material comes off upon rubbing with organic solvent thus organic contaminant such as cutting oil from boxes or post-anodize contact or oil slick on final hot water following sealing and (2) yellow is chromate from dichromate seal contamination of rinse that nickel acetate seal is also common rinsed in or that chromate from deox prior to anodize is weeping from porosity in casting or out of poorly rinsed blind holes. Quick thoughts - don't suspect it's the nickel acetate seal and beware cutting sealing time from back to 1 minute - your parts will fade fast and your customer will be right back at you charging you to disassemble and replace formerly blue parts! Any anodizer who suggests cutting back a seal time this much, I'd worry about them!
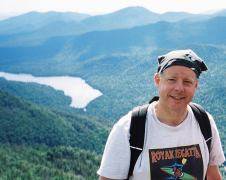
Milt Stevenson, Jr.
Syracuse, New York
2007
WE manufacture aluminum valve bodies, that are currently anodized clear then sealed with nickel acetate.
We are having problems with our O-rings sticking shut at low pressures on this sealed surface.
Any suggestions would be Greatly appreciated ASAP
best regards,
- St. Petersburg, Florida
2007
First - there are no yellow salts of nickel.
The fact that alcohol removes the weeping indicates that the material is probably organic. I would suspect a component of the dye.
Milt is quite right about the possibility of the dye fading if you do not seal. On the other hand, in the aerospace industry, where anodising before bonding or painting is common, parts are not usually sealed and a strict time limit is imposed between anodising and paint or bond.
In this case someone will have to decide which is the more important, dye sealing or adhesion.
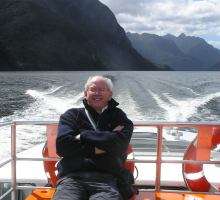
Geoff Smith
Hampshire, England
2007
Q, A, or Comment on THIS thread -or- Start a NEW Thread