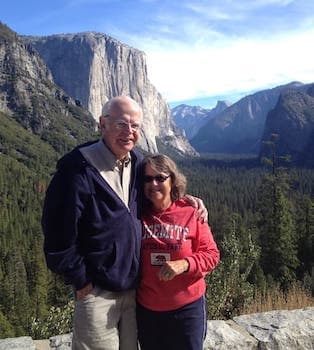
Curated with aloha by
Ted Mooney, P.E. RET
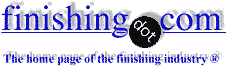
The authoritative public forum
for Metal Finishing 1989-2025
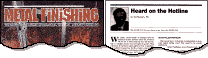
-----
Deburring ID of Niobium Sheet 14"x 4" x .013" thick
We make jewelry out of 99% pure Niobium Sheet. We make about 1000 pieces per day. We recently purchased an abrasive waterjet cutting machine to cut out intricate filigree shapes out of .015" thick material. We leave a "snap tab" on the part so it doesn't sink into the machine. Because the material is relatively thin, the waterjet leaves a burr around the entire edge, both inside and out. What I need is a recommendation on the best way to deburr an entire 14"x4"x.013 niobium sheet before we snap the parts out. The parts range in size from 1/4" across to 1.5" across. So far, centrifugal barrel finishing seems to give the best results. Any suggestions? Thanks
Holly Yashiproduct designer - Arcata, California, USA
2007
First of two simultaneous responses --
Work with the Mfg of your unit. Changing parameters and probably grit/size should give you a fairly good edge. Burs normally result by trying to go too fast.
James Watts- Navarre, Florida
2007
Second of two simultaneous responses --
I'm surprised that you are not getting distortion with the centrifugal system. Personally, I'd recommend you take the parts out of the strip and use a vibratory machine system. Set the eccentric weight to minimum aggressiveness and use our dry abrasive organic product called 6A. Time maybe 2-4 hrs or longer. If you need a polished finish you can do a second step.
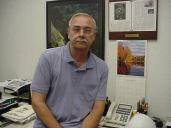
AF Kenton
retired business owner - Hatboro, Pennsylvania
2007
Q, A, or Comment on THIS thread -or- Start a NEW Thread