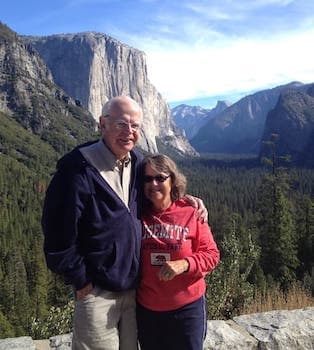
Curated with aloha by
Ted Mooney, P.E. RET
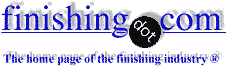
The authoritative public forum
for Metal Finishing 1989-2025
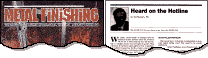
-----
Inconsistent adhesion of electroplated nickel to electroless nickel
We have a supplier plating 6061 aluminum forgings with an electroless nickel strike followed by electroplated nickel/chrome. we test the adhesion by cutting the component and checking for delamination. However we are now experiencing a percentage of product where the electroplated Nickel is coming away from the electroless. our supplier suggest this may be down to contamination of swill in between the baths and that introducing a copper cyanide layer will prevent this.
Can anyone shed any more light on this issue.
Design engineer, - Bournemouth, England
2007
You have any number of possibilities and since you say nothing about your process, all we can do is guess. My nickel goes to the nickel strike passivating because you are taking too long to get it into the regular nickel operation.
James Watts- Navarre, Florida
2007
No, do not add a copper CN strike. Instead put a Nickel chloride strike in between the two nickels. Two pounds per gallon Nickel Chloride with one quart per gallon Hydrochloric Acid, R D Anodes (take out when not in use and leep the metal low),room temp, 100 amps per square foot - it will not chisel off !1.
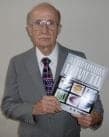
Robert H Probert
Robert H Probert Technical Services

Garner, North Carolina
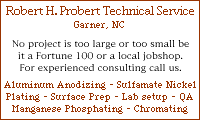
2007
Simon
I cannot disagree with Robert Probert.
Just remember he is speaking of US gallons (3.8 litres) not UK gallons (4.6Litres)
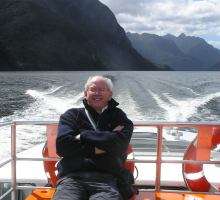
Geoff Smith
Hampshire, England
2007
First off, I don't want to take away from my presentation at the Electroless Nickel 2007 conference sponsored by "Products Finishing" (www.pfonline.com/en) at the end of the month but I've experienced and I've heard EN suppliers state that these new cad-free / lead-free RoHS compliant EN baths are difficult to reactivate meaning that subsequent layers don't want to stick to them. This may be what your experiencing especially if all the parts were good a year or so ago and now you've seen some increased fallout. Secondly, what's this "swill" terminology? Why can't you Brits just call it a "rinse" which is what it is!
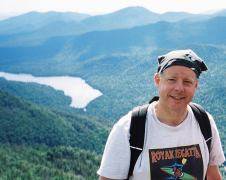
Milt Stevenson, Jr.
Syracuse, New York
2007
My vote goes with James, it sounds so much like a passive nickel layer, in which case nickel strike isn't going to help a lot. Make sure that the minimum time is taken transferring from the two nickel processes, with proper swilling of course, or rinsing if you are in the USA!
Brian TerryAerospace - Yeovil, Somerset, UK
2007
2007
It does sound like passivation to me as well. Adding a strike ought to fix it.
Mr. Stevenson brings up an interesting point - if it's the alternate bath stabilizer that's causing the trouble (that is the role Pb or Cd played in EN formulations, eh?) why is this? Do they need to add whatever it is in a much higher concentration? My recollection is that Pb was in these solutions at ppm levels, and not a major constituent of the deposit.
Sadly, what they ARE using is proprietary information, like so many things these days. That makes it hard to devise a remedy.
As for our British friends, and UK usage, we do have to admire the multi-meaninged word...
Cheers!
Which I'd like to see as current usage in the USA, too. However, I still spell it 'sulfuric' and not 'sulfuric'.
:)
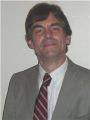
Dave Wichern
Consultant - The Bronx, New York
I was reading the Electroplating Engineering Handbook ⇦ this on
eBay,
AbeBooks, or
Amazon [affil links]
the other day, and a number of propietary bath stabilizers are mentioned. I don't have the book in front of me, but I recall thiocyanate was one of them.
If a goodly amount of NiS codeposits with the Ni-P, as it does in a black nickel bath (which also contains thiocyanate) acid treatment or a nickel strike might leave a layer of sulfurous schmutz on the surface. That would account for the difficulty.
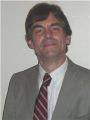
Dave Wichern
Consultant - The Bronx, New York
2007
Q, A, or Comment on THIS thread -or- Start a NEW Thread