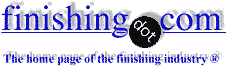
-----
Latest equipments and methods for cleaning drill debris in high aspect ratio holes
What are the latest equipments and methods for cleaning drill debris in high aspect ratio holes?
Robin JohnEngineer - West Chicago, Illinois, USA
2007
With modern and high tech drilling methods available, drill debris should be a thing of the past, or at least greatly minimized. Plasma etch works well, vapor honing/ blasting machines for the PCB industry have improved over the years as well. A search for "cleaning of high aspect ratio holes" is a good start.
Mark BakerProcess Engineer - Syracuse, New York
2007
2007
The answers you get are only as good as the question.
It would help to have some idea of the size and depth of the hole. Are we discussing thous or feet? The material has a bearing too.
Mark is right, mostly we see very little drill debris these days but PCB drilling is very specialised in composite material.
For metals, the gun drill is very old established technology. ECM and EDM are self cleaning.
Thinking on ... the oil industry go in for very high aspect ratio holes..
It also matters what you want to use the hole for. If you want to plate down there removing debris is only the start of your problems.
Please tell us what you want
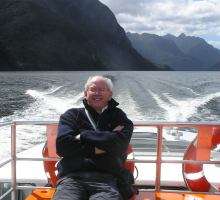
Geoff Smith
Hampshire, England
The size of the holes are .008"-.012" on .125"-.150" thick 10-16 layer printed circuit boards with polyimide material construction. The drilled holes are then metallized by desmear/electroless Cu process.
Robin John- West Chicago, Illinois, USA
2007
Robin,
I am very familiar with the board thickness and hole diameter you are referring to. I used to build 28 layer backplanes in the mid 80's, so I can sympathize with you. This was before drilling technology improved to what it is today. We had a vertical vapor blast machine that held 5 panels at a time and did a good job removing drill hole debris. If the problem can't be solved in your drill room by adjusting drill speed, stack height, drill bit quality, vacuum capacity, try using a high pressure water spray on the boards after drill, similar to the solder mask screen and frame cleaning method. You will have to build a jig to keep the board steady of course, and pressure spray each side of the board. The other alternative is to buy a machine to clean the holes as mentioned in my first response. Good Luck!
Process Engineer - Syracuse, New York
2007
Q, A, or Comment on THIS thread -or- Start a NEW Thread