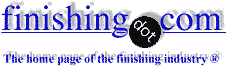
-----
Inconel 718 Hysteresis
2007
Q. We form bourdon tubes from Inconel 718 where we have found hysteresis differences in performance between different lots of material. Lots meaning from a different supplier/melt source. Chemical compositions appear roughly the same and meet the standard specified by AMS5589.
I am hoping someone can possibly steer us in the right direction as possible sources for the hysteresis differences. The hysteresis characteristics appear to track raw material lots based on multiple tests conducted with both sets of material.
Process background (generalized):
1) Purchased material: Inconel 718, bourdon quality, solution annealed per AMS5589.
2) EBW (for sealing) and forming into bourdon tubes
3) Heat treatment: 1750 for 30 minutes in argon or vacuum. Atmospheric cool in retort. Age at 1325 °F for 8 hours, furnace cool at 1150 °F. Hold for total aging time of 18 hours.
4) Brazing operations after heat treatment, in certain local areas, liquidus temperature ~1300 °F.
Mfg. Engineer - Redmond, Washington, USA
A. A 1979 DOE study 'Influence of heat treatment on the microstructure and mechanical properties of Alloy 718 base metal and weldments' mentions "Light microscopy, thin foil, and surface replica electron microscopy revealed that the microstructure of this superalloy was sensitive to heat treatment and heat-to-heat variations." http://www.osti.gov/energycitations/product.biblio.jsp?osti_id=6016371
Note, however, that solutionizing was at 1700-1850 °F for a minimum time far more variable than the AMS spec.
I presume you've already checked hardness (Rc 36 or equivalent) and tensile properties. Probably, next is microscopy to check the grain size (which affects yield stress and work hardening). Expect some variation with alloy chemistry (constituents & impurities), amount of cold or hot working prior to solutionizing, and the solutionizing time and temperature. Perhaps consult with a metallurgist from a supplier or Special Metals. Download their 'INCONEL® alloy 718' bulletin (if you haven't already done so).
- Goleta, California

Rest in peace, Ken. Thank you for your hard work which the finishing world, and we at finishing.com, continue to benefit from.
2007
2007
A. "3) Heat treatment: 1750 for 30 minutes in argon or vacuum. Atmospheric cool in retort. Age at 1325 °F for 8 hours, furnace cool at 1150 °F. Hold for total aging time of 18 hours.">>
The cooling rate after solution treatment is very critical. In aircraft engine component manufacturing, where consistency is also highly important, the cooling rate after solution treatment (annealing) is at least 40 °F per minute down to 1000 degrees. Cooling continues to below 400 degrees before the precipitation hardening cycle (aging) commences.
The temperature uniformity of the furnace should be surveyed in accordance with MIL-H-6875H [link is to free spec at Defense Logistics Agency, dla.mil]
. A load thermocouple should be used for monitoring and certifying temperature throughout the cycle.
Using the cycle you describe, you should expect a hardness range of 40-44 Rc. All else being equal, the width of this range is largely due to variations in chemistry and processing in manufacture of the tubing, and cannot be improved upon.
I would not advise heat treating in a flowing Argon- purged/filled retort. The quality level you are seeking requires the use of a vacuum furnace with pressure-controlled gas back-fill and an internal circulator fan, and a large external water-air fan-cooled heat exchanger cooling system, or a water-evaporation system.
I hope this information is helpful. If you have other, related questions please let me know.
- Durham, Connecticut, USA
Equilibrium diagram of Inconel 718
Q. Sir,
I am doing a project on Inconel 718. I have to see effect of work hardening. So that I am in need of equilibrium diagram of Inconel 718. So please tell me about this.
b.tech mechanical engineering student - Chiplun, Maharashtra, India
2004
A. Special Metals, the producer of Inconel alloys, has a great deal of technical information available on their website. I suggest you start there, and if the product literature does not have what you need, then perform a keyword search of scientific journal articles using Cambridge Scientific Abstracts, Scirus, or something similar.
Toby PadfieldAutomotive module supplier - Michigan
2004
Q, A, or Comment on THIS thread -or- Start a NEW Thread