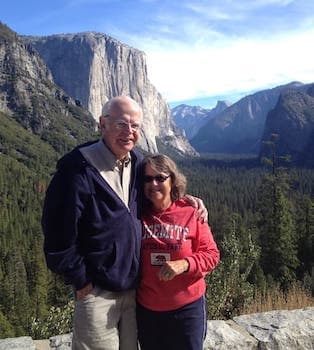
Curated with aloha by
Ted Mooney, P.E. RET
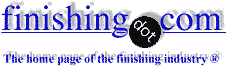
The authoritative public forum
for Metal Finishing 1989-2025
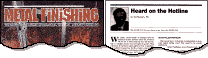
-----
Mill Finish Part 2
Can the "mill finish" of aluminium from the mills be a black oxidation which will not come off without resorting to mechanical means? We have aluminium pieces that were received by a metal fabrication subcontractor of ours. This subcontractor fabricated the pieces to drawings and shipped the pieces to our project site. Upon receipt, the pieces were examined by both our personnel and a clients representative. They expected that the pieces would be shiny aluminium.
The specifications call for the pieces to have a "mill finish". What should they expect to see?
Quality Control on Project Sites - Louisville, Kentucky, USA
2007
2007
Mill finish isn't precisely defined; it will vary with alloy, temper, product form and final mill operation. Cold rolled sheet or plate and cold drawn rod or wire will have a bright surface. Extruded material, quenched and age-hardened, is somewhat less bright. Structural material covered by solutionizing (high temperature) oxide will be duller, and some discoloration is allowed. See also Letters
#26772 and
44570.
Fabricated material has an as-fabricated surface defined only by blueprint and contract language. I've never seen an unspecified black color (other than mistakenly dyed clear anodize).
Black 'oxidation' might be burned-on lubricant or from heating in a sulfurous, fuel oil combustion atmosphere. A wild guess is that the fabricator annealed and oiled parts to aid in forming, then did an entire heat treatment to recreate a T6 temper. Or perhaps, lubricated and then annealed. ASTM B918, 'Standard Practice for Heat Treatment of Wrought Aluminum Alloys,' requires cleaning of heavy lubricants prior to solutionizing heat treatment (light oils may burn off cleanly). Also, porosity due to high temperature oxidation is cause for rejection.
AMS2770, 'Heat Treatment of Wrought Aluminum Alloy Parts,' is perhaps more rigorous regarding finish [I don't have a copy], as it covers heat treatment of fabricated parts.
- Goleta, California

Rest in peace, Ken. Thank you for your hard work which the finishing world, and we at finishing.com, continue to benefit from.
Q, A, or Comment on THIS thread -or- Start a NEW Thread