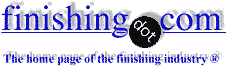
-----
Hard chrome plating of different size diameters in one visit to chrome vat
2007
Hi. I'm Alan. An engineering student from Liverpool University.
My current project involves minimising the vat time for piston type components. This particular piston requires chrome plating on both the head & shaft areas of the part.
A 6 hr plating cycle gives me different depositions. The large diameter gets the required amount but the shaft gets hardly any chrome on it. I think the head diameter is "robbing" the chrome destined for the shaft. All I want is an equal deposition on both large & small diameters.
Please help!
Student - Liverpool, England
The distance from the anode is affecting your plate rate. If possible, start using conforming anodes as you can tweak the anode to control where the plate goes. Look up Hard Chrome Consultants in Cleaveland, Ohio. The author is dead, but they sell a very good notebook on chrome plating fixturing. Lots of selfserving (__) but is an excellent resource if you overlook the (__). Fringe benefit is a much higher plating rate while still maintaining a hard bright chrome plate.
James Watts- Navarre, Florida
2007
2007
Therefore,would shaped anodes help? ie. to maintain a constant distance between anode and component.(The anode shape could mirror the component perhaps?)
Are anode "sleeves" in common use? (i.e., held very close to the component,but insulated from it,to ensure chrome gets to the required area.)
Cheers,
Alan.
- Liverpool, England
Yes, shaped anodes can be used and very commonly are -- that's what James Watts was referring to, Alan. The overall issue of fixturing (racks to hold the parts, plus conforming anodes) is one of the most vital concerns in many specialty hard chrome shops.
It is probably possible to put a sleeve or sock on the conforming anode but, no, they are not in common use.
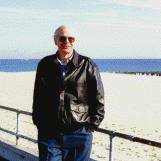
Ted Mooney, P.E.
Striving to live Aloha
finishing.com - Pine Beach, New Jersey
2007
1/2 inch to 1 inch anode to cathode spacing along with removing some of the anode in some of the areas and adding to it in others (knowledge + trial and error) can come decently close to minimizing the after plate grind time and eliminate wasted chrome plate, handling, time and money. For a GOOD shop or for one that is willing to learn.
James Watts- Navarre, Florida
2007
Q, A, or Comment on THIS thread -or- Start a NEW Thread