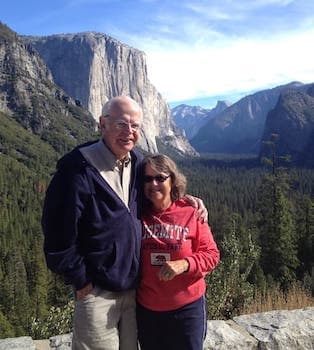
Curated with aloha by
Ted Mooney, P.E. RET
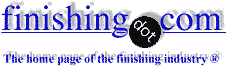
The authoritative public forum
for Metal Finishing 1989-2025
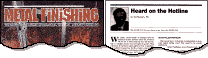
-----
Hard anodizing plus powder coating as a marine finish
Current question and answers:
PVDF over 25 micron anodising
Q. It has been considered that lesser micron anodising could be taken as a base for powder, however, for liquid PVDF, mill finish is the most suited. A customer now wants 2-coat PVDF over 25 micron anodising for the product to be used high-seas. For him looks are not important, corrosion prevention is. We suggested a three coat instead of this.
We performed some short term tests like cross hatch/ impact and conical mandrel, and found some problems.
Please suggest how would the bonding and compatibility go.
Thanks
- JAIPUR, Rajasthan, India
October 18, 2020
A. Hi Sanjay. I can almost never improve on the answers that Ken Vlach offered, and this time is no exception. Conical mandrel testing doesn't seem appropriate for 0.001" anodizing though. Did you opt for sealing or no sealing for the short term tests you ran?
Luck & Regards,
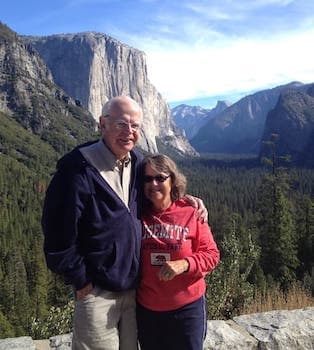
Ted Mooney, P.E. RET
Striving to live Aloha
finishing.com - Pine Beach, New Jersey
November 2020
⇩ Related postings, oldest first ⇩
Q. We need to decide the surface treatment for some 6061-T6 AL parts. The parts are intended to be used in a marine environment for more than 6 years. (Generally above the waterline)
My questions are:
1. Is Type III hard anodizing plus powder coating a good practice to achieve excellent corrosion resistance?
2. Should the hard anodizing be sealed considering the effect of paint adhesion and corrosion resistance?
3. What is most preferred surface finish on 6000 aluminum alloy for marine application? Any literature or reference?
Thanks,
product designer - Newark, Delaware, USA
2007
A. 1. Don't know; there are potential problems.
2. Yes, dichromate sealed. Test marine grade primers for adhesion.
3. Micro arc oxide (MAO) aka Plasma Electrolytic Oxidation (PEO) + PTFE copolymer + PTFE. See also alternative below.
Anodizing as a paint pretreatment isn't common due to the good performance of less expensive chromating.
The Surface Treatment and Finishing of Aluminum and Its Alloys (pages 1193-5, & 1244 in the 6th Edn.) mentions conventional anodizing as an acceptable substitute for chromate pretreatment in some European standards. ASTM D1730, 'Standard Practices for Preparation of Aluminum and Aluminum-Alloy Surfaces for Painting,' includes dichromate sealed Type II as well as chromic acid anodizing. I don't have any experience with hard anodizing plus powder coating, but suggest that the high temperature curing may cause detrimental cracking of the hard anodize. The cure temperature could also affect the 6061-T6 strength although the time is relatively brief cf. the T6 aging (18 hours at 320 °F or 8 hours at 350 °F). I also don't know whether the high electrical resistance of hard anodize may affect powder adhesion.
Hard anodizing is only used as a paint pretreatment when abrasive conditions are expected. I have seen dichromate sealed hard anodize + zinc chromate epoxy primer + polyurethane* topcoat used for deep-sea devices. To eliminate the crazing observed from immersing hard anodize in hot sealing solution, parts were placed into the dichromate seal at ambient temperature, then heated to and sealed at 160 °F (crazing occurred above 165° F). The alloy was 7075-T6; 6061-T6 may behave differently.
footnote: * High performance PVDF-containing wet paints are available, but high solvent contents may limit use.
- Goleta, California

Rest in peace, Ken. Thank you for your hard work which the finishing world, and we at finishing.com, continue to benefit from.
Q, A, or Comment on THIS thread -or- Start a NEW Thread