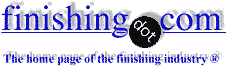
-----
Coating for fitting in very aggressive acid bath
2007
We are working on a product that extracts hot, acidic gasses mixed with air and water vapor from an oven to be analyzed. The gasses should not condense, but in actuality small amounts do. Most of the system holds up well, but we are having failures in the tube fitting that connects the Teflon tube to the main body and we are looking for help in specifying a coating to improve the life of the fitting.
We are currently using a 316 stainless pipe thread to tube fitting. Upon failure, the fittings appear to have been eaten through from the inside out.
The system operates at 150C (300oF).
The acids that the fitting may be exposed to are hydrochloric, hydrofluoric, nitric, sulfuric or a combination of two or more of these acids at any concentration level. Due to the air flow, the acids should be considered aerated.
Most of the time, the tube and fitting are under a mild vacuum, but there is a blow down feature that back flushes the filter. For a short period, the fitting may be exposed to as much as 150 psi.
The solid Teflon fittings that we have looked into are inert to the acids, and will stand the temperature, or the pressure, but not the combination of temperature and pressure.
I have looked at several commercial coatings and they look promising, but this is a very demanding application. Is there a coating that will stand up to this combination of temperature, acids, and pressure? Is there a coating that can be reliably applied to the interior of a 3/8" NPT to 3/8" tube fitting?
Product designer - Barltesville, Oklahoma
This is obviously a very difficult application, but teflon or PVDF coatings might be fine.
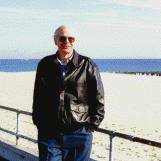
Ted Mooney, P.E.
Striving to live Aloha
finishing.com - Pine Beach, New Jersey
2007
Nasty! As soon as you combine hydrochloric and nitric acids particularly at elevated temeprature, you can rule out pretty well all metals.
If you have room for the fitting's external dimensions to be a bit larger, perhaps a ceramics expert can recommend a glazed, fired ceramic material for the whole fitting.
Or perhaps a smaller ceramic fitting with a metal safety cladding around it.
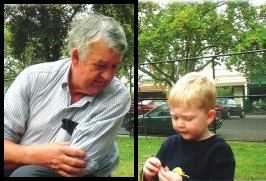
Bill Reynolds [deceased]
consultant metallurgist - Ballarat, Victoria, Australia
We sadly relate the news that Bill passed away on Jan. 29, 2010.
2007
2007
PTFE or PVDF are fine if thick enough to eliminate porosity, so not practical for threads. If threads need protection, proprietary, diamond-like coatings (DLC) are claimed to be highly corrosion resistant at extreme thinnesses.
Whether or not a coating is used, use a more corrosion resistant alloy. For more info, see 'Acidic Environments Containing Halides ˜ Flue Gas Condensates' in High-Performance Stainless Steels (available from the Nickel Institute http://www.nickelinstitute.org). Also,
'CORROSION PERFORMANCE AND FIELD EXPERIENCE WITH SUPER DUPLEX AND SUPER AUSTENITIC STAINLESS STEELS IN FGD SYSTEMS,' www.nationalmetaldistributors.com/download/NMDTM_FGD.pdf
Possibly, HASTELLOY® C-276 (UNS N10276), HASTELLOY® C-22
(N06022), Ni-Cr-Mo Alloy 59 (N06059), Alloy 686 (N06686), CARPENTER
20Mo-6® (N08026), 654 SMO (S32654), SR-50A (S32050) or URB66
(S31266).
- Goleta, California

Rest in peace, Ken. Thank you for your hard work which the finishing world, and we at finishing.com, continue to benefit from.
Q, A, or Comment on THIS thread -or- Start a NEW Thread