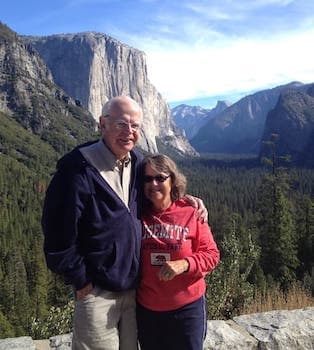
Curated with aloha by
Ted Mooney, P.E. RET
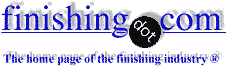
The authoritative public forum
for Metal Finishing 1989-2025
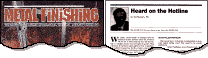
Thread 462/62
Our problem is anodizing aluminum sheet
2007
Hi,
Our Company does coating of surfaces of nonferrous materials and ferrous materials. We have a problem. One of our Customers requested
0,4 mm(0,015') thickness aluminum sheet (2024 alloy) type 2 of MIL
8625. Accordingly we had coated that material( dimensions : 76 mm*250 mm (3'*10')) under the below listed conditions.
Free Acid :220 g/l H2SO4
Current : 1 A/dm2
Temperature : 17-18 C ( 63-65 F)
Time of Coating : 1 hour
Total Thickness :10-12 µm Objective thickness : 17-18
µm
Hanger material : titanium
Dye : Sanodal Black W bath 50 °C 10 g/l pH : 4,5-5,0
It should be elegiac and difference of film thickness on aluminium sheet.
What can we do of this problem ? I hope explained this matter.
quality assurance - Ankara, TURKEY
publicly reply to Dicle Dinler
You did provide a lot of detail, Dicle, and we appreciate it. But I apologize that I do not understand what your question is asking, and I can only take a guess. Generally, anodized films consume about 50 percent of their thickness in aluminum. That is to say, if what you call your "objective thickness" is 17-18 microns, the thickness of the coated sheet will be increased only by what you call "total thickness" because of the consumption of aluminum from the sheet (assuming anodizing on only one side of the sheet).
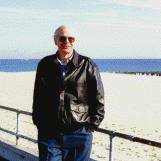
Ted Mooney, P.E.
Striving to live Aloha
finishing.com - Pine Beach, New Jersey
2007
publicly reply to Ted Mooney
2007
As Ted said, we really do not understand what you asked.
let me guess, what you mean is that under your operation condition, you can not get your target(objective) thickness---17-18um but
12um.
you could tackle the problem either
1. lower H2SO4 concentration to 160--180g/l
or
2. put current density at 1.2--1.4A/dm2
- Singapore
publicly reply to John Hu
2007
Dear Authority,
I have try again my inquirys about anodizing for 2024 alloy of alummium sheet(0,4mm thicknees).Last Our work conditions are in order to :
Free Acid Concentration : 190 g/l
Al Concentration : 9,5 g/l
Current density : 1,2 A/dm2
Temperature : 17-19 degree of centigrate
Hanger material : titanium
Anod : Lead
time of coating :70'
coating thickness : 20 µm
black dye bath time :20'
5 pieces of plate are hangered. It is formed burne and flux in contact points of sheet surface. What will we do prevent of this problem? Is Titanium hanger material possibly wrong choise for this alloy?
Other problem is atmospheric corrosion of 2024 sheet. We applied methods of brushing scotch and emery treatment with number 800.Can we eliminate with this method of corrosion stains?
Thanks a lot
quality assurance - Ankara, TURKEY
publicly reply to Dicle Dinler
First of two simultaneous responses --
Titanium surely has side effect for the burning, but in your case, it is not detrimental. Under your condition, if you keep constant current density---1.2A/dm2, what is the ending voltage?
trial run at keeping constant voltage which is 2 volts lowerer than what your ending voltage is now(let's say, at constant current density 1.2A/dm2, your ending voltage is 19V, then you trial run at constant voltage 17V). The plating time would be different to get the same thickness but not so much.
- Singapore
2007
publicly reply to John Hu
Second of two simultaneous responses --
We still do not understand. My best guess is that you are not distributing the current on the thin plate. Use an inverted "V-block" (notched V on the bottom) of ALUMINUM, Then use the titanium clips ONLY to mechanically hold the panel in place. The aluminum will distrubute the current evenly and you may get more uniformity. Tiny titanium clips wilo NOT deliver enough current to thin aluminum plates.
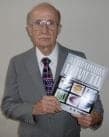
Robert H Probert
Robert H Probert Technical Services

Garner, North Carolina
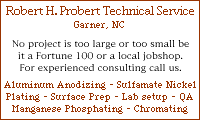
2007
publicly reply to Robert H Probert
Dear Authority
Thanks a lot all of knowledge about my inquiry.
The problem is solved.I have used aluminium clips.There was no burning.The aluminum clips distrubuted the current evenly all of surface.I took 22 µm thickness in 70 minutes.
Second problem goes on.I wouldn't prevent tracks of atmospheric corrosion.Abrasion methods released unwanted striate on surface.Can you suggestion about this subject?
Again thanks.
quality assurance - Ankara, TURKEY
2007
publicly reply to Dicle Dinler
Q, A, or Comment on THIS thread -or- Start a NEW Thread