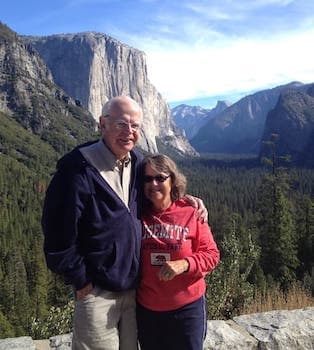
Curated with aloha by
Ted Mooney, P.E. RET
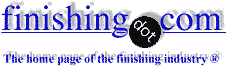
The authoritative public forum
for Metal Finishing 1989-2025
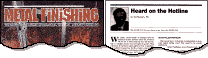
-----
Double sealing anodizing to stop DI water corrosion in fuel cells
2007
We hard anodize to MIL-A-8625, Type III, Class 1 to prevent both corrosion of the aluminum parts but more importantly to prevent the aluminum and its alloys from leaching into the DI water or wet hydrogen as contaminants. (as I mentioned previously in letter
46000)
It has been recommended by the suplier of our DI filters to do a
"dual" sealant of nickel acetate followed by potassium dichromate for maximum corrosion resistance.
Logically I understand that 2 "layers" of sealant would be better than 1. I'm not all that concerned about dimensional stack up on the parts we are doing now but I was wondering if anyone had any insight into how sealant affects part size, what kind of relative cost I'm looking at for a second bath and any other general thoughts on the subject.
I've never heard of anyone doing a "dual" seal, but it is critical to prevent contaminants from reaching the fuel cell stack as it could contribute to premature failures.
Thanks in advance for your input.
Manufacturing Engineer - Richmond, BC, Canada
First of two simultaneous responses --
Hi Ari,
Saying DI is not specific enough. If your limit is 10 K ohm water, it is not going to make much difference. If you are working with 10 to
15 Meg ohm water, I seriously doubt if either single or double seal is up to the task. Really pure DI will leach out the seal material and then literally attack the aluminum oxide hard anodize film.
You might be able to apply one of the teflon family products and get a non porous film, but quality will typically vary.
PS, this is NOT a quote teflon impregnated anodize, which has been argued about at this site many times with my vote going that the teflon is larger that the anodize pore, therefore it is a surface phenomenon and not impregnation. Typical it is a teflon dispersion in a silica matrix, which is great for some applications , but not yours.
- Navarre, Florida
2007
Second of two simultaneous responses -- 2007
Try it in a bucket first to be sure that the dichromate does not leach back into your prodcut and cause more damage than just corrosion. Also try Nickel Acetate for the first stage and water with
1 gm/L ammonium acetate as the second stage.
I do not knwo if Ted can print the following as it comes from my book, but here goes:
Process I
Stage One: Standard NIckel Acetate, 150 to 170 F, 20 minutes
Stage 2: D.I.Water, with 1 gm/L Ammonium Acetate pH adjusted to 5.7
± 0.3 with acetic acid
⇦ this on
eBay
or
Amazon [affil links] .For 20 minutes
Process II, which you asked abnout and I am afraid will leach.
Stage 1: Nickel Acetate as above 10 minutes
Stage 2: Sodium or Potassium Dichromate 50 gm/L, 10 min
Try all of this in a bucket and test the parts.
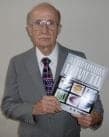
Robert H Probert
Robert H Probert Technical Services

Garner, North Carolina
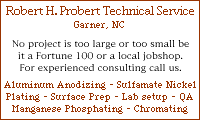
2007
Thank you both for your response. It has given us a lot to think about. Our part is not very well suited for Teflon w/o some pretty specialized tooling because of its geometry. The section that we are concerned about sees 500K ohm water if that any difference to either of you. We understand that none of these sealants are bullet proof; we are looking for improved life of our system and will try what the vendor recommended and do some testing.
Thanks again for your input.
-Avi
- Richmond, BC Canada
Q, A, or Comment on THIS thread -or- Start a NEW Thread