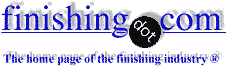
-----
Standards for Cyclic Corrosion Testing
2007
Q. Respected gentlemen,
We are one of the leading manufacturers of Automobile Electrical parts in India. We export our products to Europe and other Asian countries, and we are recommended higher corrosion resistant finish for our products and we do the same.
In order to evaluate the resistance to corrosion, we follow NSS [neutral salt spray] test according to ASTM B117 and that takes minimum 45 days to 60 days to verify the results according to our customer requirements. To reduce this evaluation period, we are interested in other methods.
1. Are there any other test methodologies to estimate corrosion with a shorter time?
2. How cyclic corrosion testing can be compared to NSS test?
3. Are there any standards available to conduct the tests? (As we understand each OEMs has their own test standards)
Can anyone clarify the above queries?
Chemist - Chennai, Tamilnadu, India
A. There are several other tests out there that will usually cause a test part to fail earlier than NSS. There's SWAAT [seawater acidified accelerated test], CASS [copper-accelerated salt spray], and others. I've seen parts that go thousands of hours in NSS fail in a day in SWAAT.
As for correlating to NSS, there is no general correlation out there in the form of X hours in (insert cyclical test) is equal to Y hours in NSS. Each test will induce a different type of corrosion mechanism, so general comparisons are not valid.
You could develop a correlation on your own by running tests side by side with the same types of parts. However, you'd need to develop a correlation for each substrate, pretreatment method, and coating (if any).
You could also look into some type of DC/EIS method [direct current / electrochemical impedance spectroscopy] for a rapid screening procedure. I know some have actually developed correlations between this and NSS. However, it's the same as for the others. You'd have to develop this correlation on your own for your specific system.
As for standards, you can find ASTM test procedures for most of the general tests. As I'm sure you know, many automotive companies have their own variations. You'd have to ask your customers for how they run their tests.
- Pittsburgh, Pennsylvania
2007
Is DI rinsing required mid-cycle in cyclic corrosion testing?
Q. Hi All,
I have a salt mist test with 2 hours salt spray (35 °C, 5% NaCl) and 22 hour humidity chamber (95% RH, 40 °C) for 3 cycles. And recovery method is wash with DI water.
My question will be is there any standard comment that the specimen needs to be wash with DI water before proceeding to the humidity chamber. Or there should be accumulated 3 cycles of test only preceded by DI water wash?
Please share your experience. Thank you.
- Singapore
April 21, 2014
A. Hi Hadson. As you can see from the previous response in the thread which we appended your inquiry to, there are many different cyclic corrosion tests. Try to obtain a copy of ASTM G85 "Standard Practice for Modified Salt Spray (Fog) Testing", which covers several of them and is usually the framework for further variations.
I believe that, in the old days, the test parts were manually shifted from one test cabinet to another for these tests; but test cabinets are available today with computerized controls which can run the whole cycle undisturbed. Because these cabinets don't, to my knowledge, have a DI rinsing feature, my guess is that DI rinsing mid-cycle is not intended. But you must quote the particular spec you are trying to comply with before people can tell you what it says. Good luck.
Regards,
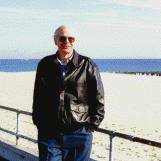
Ted Mooney, P.E.
Striving to live Aloha
finishing.com - Pine Beach, New Jersey
April 2014
Q, A, or Comment on THIS thread -or- Start a NEW Thread