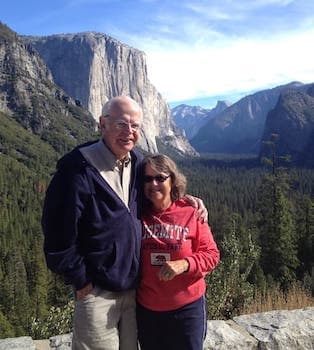
Curated with aloha by
Ted Mooney, P.E. RET
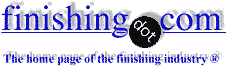
The authoritative public forum
for Metal Finishing 1989-2025
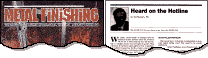
-----
Need suggestion for non-Magnetic steel
Q. Hello all, I'm working on a project and need some guidance. I am searching for a non-magnetic metal to replace 304 stainless. The application environment is 120 C, in 70w-140 oil, and the ID of the piece sit on a shaft rotating at 150 RPM (most have good wear resistance). Any ideas for a replacement material. Thanks
Brunno Covolanengineer - Wylie, Texas
2007
![]() |
304 is normally non magnetic unless cold worked. Heat treatment will lower the magnetic level. Have you tried a professional degaussing unit? James Watts- Navarre, Florida 2007 If you want similar strength and hardness to 304 stainless, aluminium bronze C95400 is a good match. ![]() Bill Reynolds [deceased] consultant metallurgist - Ballarat, Victoria, Australia We sadly relate the news that Bill passed away on Jan. 29, 2010. 2007 |
Q. Bill
You say Phosphor Bronze for bearing bushes etc; did you mean cast or wrought PBr. I'm asking since we have had material availability problems on items for actuator components; bearing bushes, thrust washers etc, which our suppliers are recommending a change from cast Leaded Bronze and Leaded Gunmetal to cast Phoshor Bronze. Also on offer, (and cheaper) is wrought Phosphor Bronze.
Could you advise on the relative wear resistance for these applications.
Regards
Martin Rich
Ship Repair - Plymouth, UK
2007
Q. Cast/Wrought Bronze/Gunmetal equivalents and material availability problems.
We have had material availability problems on items for actuator components; bearing bushes, thrust washers etc, for which our suppliers are recommending a change from cast Leaded Bronze and Leaded Gunmetal to cast Phosphor Bronze. Also on offer,(and cheaper I suppose) is wrought Phosphor Bronze.
Could you advise on the relative wear resistances and suitability for these applications.
Regards,
Technician - Plymouth UK
2007
Non-magnetic Material for Bearing Slot
Q. I have a new product to market and need suggestions for best material for the bearing holder/sleeve. I have a 3/4" diam shaft and a standard bronze bushing over that and have placed that bronze through a SS washer pressed into the wall plate of 1/4" Al. It works but I am curious about the lifetime due to potential wear. This product is a magnetic separator for sands so these components must be non-magnetic but may be subject to dusty conditions and wear becomes an issue. What would be the best material to use for this application? The bronze can be easily replaced but the "pressed washer" needs to have a long wear life?
Mike Robinsonnew manufacturer - Odessa Texas USA
September 18, 2017
A. `Hello,
I think a teflon coating should work;
Molycoat is another option.
Regards,
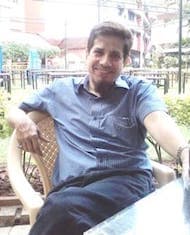
Khozem Vahaanwala
Saify Ind

Bengaluru, India
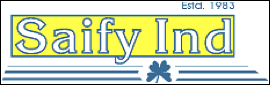
December 14, 2017
Q, A, or Comment on THIS thread -or- Start a NEW Thread