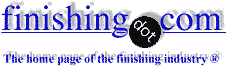
-----
Can corrosion pit be created in Zinc Phosphated springs?
We are experiencing fatigue failure of springs used in Booster Assembly. By SEM analysis we observe it is due to pit corrosion. The springs are zinc phosphated, de embrittled at 110°C for 1 Hr, Oiled (Transit) and then degreased with Tri Choloro Ethylene and then used for assembly in Booster. Request to provide us the areas where we have to concentrate to prevent pit corrosion. In this we have not considering Hydrogen embrittlement since we use phosphoric acid in our phosphating process.
G SriramDeputy Manager - Quality Assurance - Chennai, Tamilnadu, India
2007
110C does not even start to begin de-embrittlement, That takes about 200C. One hour is a bit short also.
If you have visible pits, that is probably the true source of your failures. Address that problem first.
- Navarre, Florida
2007
We do not use Hydro Choloric acid in our phosphating process. Pickling is done using Phosphoric acid. Can this lead to embrittlement?. Can tri choloro ethylene create a corrosion pit?
G Sriram- Chennai, India
2007
TCE absolutely can contribute to pits, if the parts are damp or wet. The TCE breaks down into HCl in the presence of water and it is at a high enough temperature to cause rapid pitting which will continue to grow with time.
James Watts- Navarre, Florida
2007
Q, A, or Comment on THIS thread -or- Start a NEW Thread