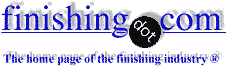
-----
What is most accurate "referee" method for composition analysis of aluminum alloys?
2007
Dear All,
I am looking for an authentic statement or any references which can be utilised when there will be any dispute among any analytical findings of the elemental contents of any alloy. As we know, there are several analytical procedures used in metal analysis - which method has higher level of confidence? In other words which method can be used as a referee test? Will it be wrong to say WET ANALYTICAL method?
I would appreciate if anybody can give some answers to it or any authentic references.
Thank you,
Extrusion Specialist [Marketing]. - Dubai, UAE
2007
The specifications to which the aluminum alloy is ordered should refer to acceptable analytical methods. For example, ASTM B209 for wrought aluminum alloys mentions ASTM E34 (includes a wide variety of wet chemistry methods & spectroscopy) and E1251 (emission spectroscopy in argon). E34 & E1251 each list measurable composition ranges for various alloying elements. Choice of analytical method will depend upon alloy.
The E34 methods are generally more accurate within given alloy concentration ranges. The E1251 method can quickly measure the various elements from a single sample and can generally detect lower concentrations of most alloying elements. However, the precision is poorer (e.g., fewer significant digits). E1251 can analyze 4 elements (Ca, P, Na, Sr) not in E34. However, E1251 cannot measure high concentrations of Si,* which is important in many cast alloys. Wet chemistry is better for average alloy composition since it uses dissolved samples. The emission methods are less accurate on heterogeneous alloys (especially castings) since conducted using solid samples; special splat quenched samples or multiple analyses can compensate.
For each specification, measurable elemental ranges, analytical procedures and referenced specifications can be viewed at www.astm.org
ASTM E34-94(2002), 'Standard Test Methods for Chemical Analysis of Aluminum and Aluminum-Base Alloys.' 35 pages.
ASTM E1251-07, 'Standard Test Method for Analysis of Aluminum and Aluminum Alloys by Atomic Emission Spectrometry.' 10 pages.
ASTM E1251-94(1999), 'Standard Test Method for Optical Emission Spectrometric Analysis of Aluminum and Aluminum Alloys by the Argon Atmosphere, Point-to-Plane, Unipolar Self-Initiating Capacitor Discharge,' 11 pages, may be better than the newer E1251 specification for some alloys,
particularly if analysis for Ag, Cd, or Sb is required, or for cast alloys of higher Si.*
The emission spectroscopy methods E227 & E607 are also commonly used, but generally ASTM E1251-94 (conducted in argon) is better than E607 (in nitrogen) is better than E227 (in air).
- Goleta, California

Rest in peace, Ken. Thank you for your hard work which the finishing world, and we at finishing.com, continue to benefit from.
Ed. note: ASTM E34 has been superceded by ASTM E3061
Dear Mr. Ken Vlach,
Thank you so much for your answer. Perhaps Wet Chemistry method would be ideal as a referee test.
Thank you once again.
Best regards,
Basu
- Dubai, UAE
2007
2007
You're welcome.
As ASTM E34 involves separate analysis of each metal, it's rather slow and costly. First use a fast, multi-element analysis technique to identify elements possibly out-of-spec. This could be an emission spectroscopy method mentioned above or EDS (Energy Dispersive Spectroscopy) within an SEM (scanning electron microscope).
- Goleta, California

Rest in peace, Ken. Thank you for your hard work which the finishing world, and we at finishing.com, continue to benefit from.
2007
Thanks. A great help.
Regards,
Basu
- Dubai, UAE
Q, A, or Comment on THIS thread -or- Start a NEW Thread