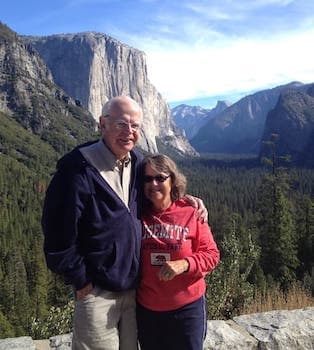
Curated with aloha by
Ted Mooney, P.E. RET
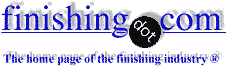
The authoritative public forum
for Metal Finishing 1989-2025
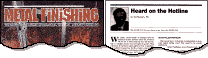
-----
Questioning the quality of galvanizing

Q. Hello forum members. I look forward to receiving your valuable feedback on this product and possible measures to improve it. I have a few pictures of the product after hot dip galvanizing as follows.
The Zn bath analysis result is as follows:
Fe: 0,07%
Al: 0,0035%
Ni: 0,0312%
for Engineers, Shops, Specifiers
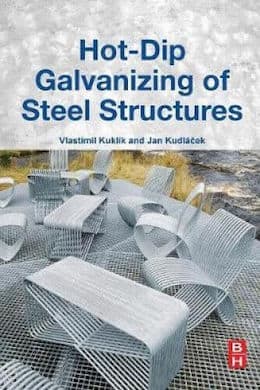
avail from eBay, AbeBooks, or Amazon
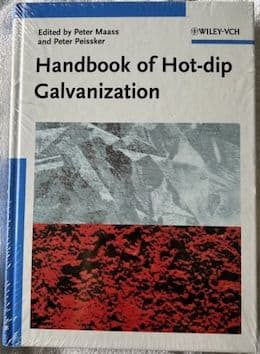
avail from eBay, AbeBooks, or Amazon
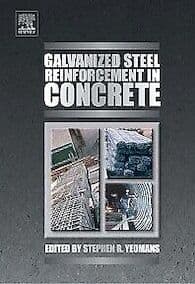
avail from eBay, AbeBooks, or Amazon
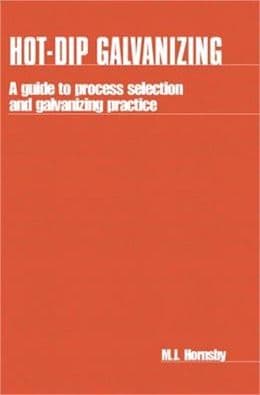
avail from eBay, AbeBooks, or Amazon
avail from Amazon
"User's Guide to Hot Dip Galvanizing for Corrosion Protection in Atmospheric Service" by NACE (1997 only rarely avail.)
avail from AbeBooks, or Amazon
(as an Amazon Associate & eBay Partner, we earn from qualifying purchases)
Is my zinc bath deficient in Nickel or other elements?
Thank you for your comments.
- Hochiminh, Vietnam
July 9, 2024
Tip: This forum was established to build camaraderie among enthusiasts through sharing of tips, opinions, pics & personalities.
The curator & some of the readers who publicly share their info are unlikely to engage with posters who don't.
A. Hi Doan,
I'm no galvanizer, but it looks quite bad to me, like the kettle was cold or the work didn't have time to heat up. The good news is I bet you'll cut your zinc usage in half when it's fixed :-)
Hopefully a knowledgable galvanizer can give you a direct route to quick improvement.
Luck & Regards,
Ted Mooney, P.E. RET
Striving to live Aloha
finishing.com - Pine Beach, New Jersey
![]() |
- Hochiminh A. Hi Doan - Doha, Qatar Comments on quality: ![]() Geoff Crowley, galvanizing consultant Crithwood Ltd. ![]() Bathgate, Scotland, UK ![]() |
⇩ Related postings, oldest first ⇩
Q. We are a sheet metal parts manufacturing company that has to supply hot dip galvanized parts to our customer. The parts are generally of 3 mm thickness and up to 250 mm long.The material is hot rolled steel Some are flat, others are in the form of a "U"-channel.Some parts have a weld
We have tried a few local galvanisers but are not satisfied with the finish. It is rough and has excess deposition near holes and sometimes even in flat areas where it seems that the zinc accumulates and solidifies.This has to be removed by filing , which leaves its own marks and results in poor aesthetics.
What can be done to improve the appearance? The thickness of galvanising is approx. 80 microns.One of the parties has a centrifuge but even these parts have problems. What should the rpm be?
Bomy DabhoiwalaOwner -sheet metal parts supplier - Mumbai, Maharashtra, India
2007
A. Sir,
this sort of surface defect is rather usual for hot dip galvanizing and is associated with both the quality of the steel surface and the process itself.
Unfortunately, hot dip galvanizing is mainly a corrosion protection system and shall not be intended as an aesthetic treatment. However, you could obtain better appearance by:
- making sure surface preparation is ok
- making sure the hot dip galvanizing line used is well kept, especially for iron levels in flux and subsequently in the zinc bath
The small particles seen in your picture indicate the presence of floating drosses that would be reduced by reducing Fe in flux and then with proper mechanical drossing in the zinc kettle.
Regards
- Brescia, Italy
A. As Mario says, Galvanizing is not an aesthetic finish, but there are things to do to improve this.
As you are not the galvanizer, you are not in control of these matters, but...
With the lower availability of GOB zinc in recent years, some zinc baths have ended up with lower Pb levels (down to 0.1%), and this can have the effect that dross is left in suspension rather than sinking. Pb at about 0.8% seems to cause the dross to increase density and sink to the bottom where it is periodically removed. SHG zinc, the more readily available, is very low in impurities, including Pb.
Dross is an undesirable alloy of Fe and Zn that forms in the zinc and in small crystals. These lumps might easioly be dross grains floating in the Zn, attaching to the steel part as its removed from the zinc.
Its quite normal to file these off.
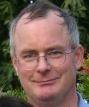
Geoff Crowley
Crithwood Ltd.
Westfield, Scotland, UK
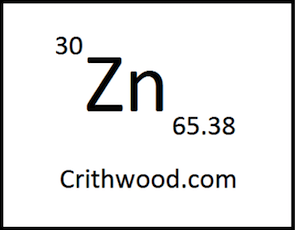
Q. Thanks for the suggestions.What is the correct level of Fe in flux. Geoff indicates that a PB content of at least 0.8% would be right. What is the max limit?
We have pretreatment line of 7 tanks for powder painting. I am just wondering whether we can add a "kettle" to do the galvanizing ourselves. We would need a capacity of 15 tons per month. The parts are all small 10 to 30 cms and all of 3 mm. In terms of number of parts it would be about 40,000.
We have small furnace for a die casting machine, so to some extent we are familiar with handling of molten zinc.
What is the kettle material? For the die cast furnace we use a cast irn pot, but it is quite small in size.
Would appreciate any comments you have on the above.
- Mumbai, Maharashtra, India
A. Starting your own Galvanizing plant for 15t/month is very unlikely to be economic. Even 15t / day might not be worthwhile!
There is no "correct" level of Fe in flux. You might say that none at all is an objective, but an unrealistic one!
Your Powdercoating pretreatment is unlikely to be at all useful in pretreating for galvanizing. For Galv you need degreaser, rinse, HCl (possibly several for capacity), rinse, flux, zinc, passivate (optional).
Zinc kettles are made from special steel (there was a question on this back a couple months). Use the right steel and it might last 10 years, use the wrong and you might get only months life from it.
Your material is only 3mm thick you say. Have you considered using pre-galvanized sheet then cut and form your articles? Do you need welding? If so, then this is not a good suggestion, but if you could press or fold from sheet, then you'd be able to get a mirror finish. It would not be so thick in Zn, but would be smooth. And far cheaper than building your own galv plant.
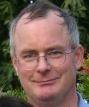
Geoff Crowley
Crithwood Ltd.
Westfield, Scotland, UK
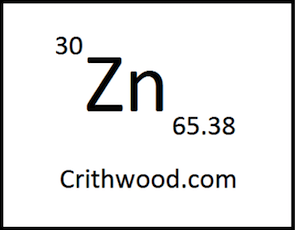
Q. Once again thanks. Starting a small unit was a shot in the dark -- obviously it's not a good idea!
We seem to have some luck in finding a few more galvanisers who are relatively better though not quite what we want. I guess we will have to work with them and improve the quality.
Regarding your suggestion of using pre-galvanized sheets we have thought about it. Unfortunately we make the parts for someone else who has to approve the change and that is not an easy job! These parts are for brackets used in antennae that are exposed to all sorts of environment. They would obviously have sheared edges and holes punched in them, which can cause rusting to start easily. Also some of the brackets are welded, so in those parts hot dip is the only answer.What is the normal thickness of galvanising for pre-galvanised sheets?
- Mumbai, Maharashtra, India
2007
![]() |
A. From you description of the use, pre-galv sheet is NOT for you. Its thickness of zinc is often only 1/4 of that from Hot Dip Galv. ![]() Geoff Crowley Crithwood Ltd. Westfield, Scotland, UK ![]() A. Sir: Galvanizing Consultant - Hot Springs, South Dakota, USA |
Q. Hi there. I am an architect and project manager on a high school remodel project which is receiving a new, 36' long ramp + galvanized railing. The railing has some defect that shows up looking like lumps of sand have been galvanized into place.
Apparently, much of the railing's surface was covered with this and the contractor sanded the surface smooth, which of course removes some of the protective zinc film. Can someone please explain what the defect is, its cause, and how it can be remedied?
Thank you.
- Palo Alto, California, USA
January 4, 2019
A. Sir: Perhaps this underside weld spattered out flux slag from welding the two members. After welding, a side grinder could have been used to remove the slag. Another possibility is that the galvanizers flux is poor and as the flux is released upward it was trapped under the rail. Still another possibility is that the steel was not properly pickled. At some galvanizing plants spattered zinc is scraped up off of the floor and then dirt is melted out into the zinc.
Regards,
Galvanizing Consultant - Hot Springs, South Dakota, USA
Thank you for your help Dr. Cook.
Project Mgmt - Palo Alto, California, USA
A. Dr. Cook has named the possibilities, but in the end it comes down to standards.
What did you specify? Did you get what you specified?
The standards most commonly used and specified are ISO 1461 (in most of the world except USA only sometimes) and ASTM A123 (mostly in USA and sometimes elsewhere).
If you specified this, did you get it?
From a galvanizers viewpoint, firstly let me say that the finish isn't acceptable, but all too often, we get comments like "I didn't get what I expected", but there'd been no definition of what was expected.
It's so simple to say up front... "Galvanize to ISO1461", or Galvanize to ASTM123" -- and then there's no doubt about what's expected, nor about whether it meets that standard. We all start from a known expectation, you on what you'll get, and the galvanizer on what to deliver (at minimum). The standard defines where and how this isn't acceptable.
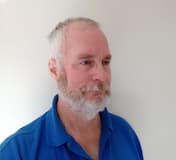
Geoff Crowley, galvanizing consultant
Crithwood Ltd.

Bathgate, Scotland, UK
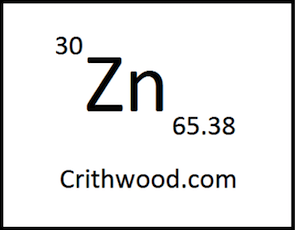
Galvanizing Appearance
Q. Dear Sir,
I am Gopinath, Head of Quality Dept.,
We are the one of the cable tray manufacturers in India. We are doing hot dip galvanising on HR sheets (After Fabrication). We are facing a problem of aesthetic look issue on galvanised material. Refer to the pictures of galvanised material.
Our customer rejected these materials for aesthetic look. We have explained to them this is not an issue of galvanising but customer not accepted. Please advice these materials are accepted or rejected.
Your reply will help us to convey our customer about the hot dip galvanising.
- THANE & India
February 22, 2020
A. Hi Gopinath. We appended your inquiry to a thread on similar issues. Please take Geoff's advice to heart regarding specifications. If you agreed to galvanize these cable trays to a spec, what spec?
I think your customer will find it impossible to sell this finish to their customer, so I think you will find it impossible to sell it to them. Although galvanizing is a 'functional' rather than 'decorative' finish, there are limits to everything, and you would never talk me into accepting these parts. Sorry. I suggest you focus on improving a poor finish rather than trying to talk customers into accepting it. Good luck.
Regards,
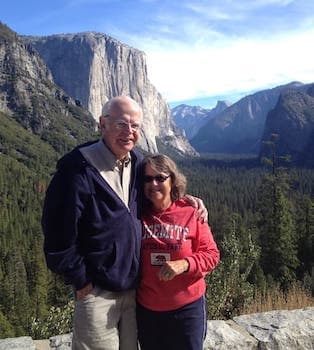
Ted Mooney, P.E. RET
Striving to live Aloha
finishing.com - Pine Beach, New Jersey
A. Yes, start with standards.
But even apart from the expectation and what was delivered, there are several problems noted in your good images here.
Numbering from top to bottom, and left to right (upper left, then upper right etc)
1. Poor fettling, but also poor drainage. Hang items more vertically if you can, if not as near as possible.I can tell from the drip angle that this was hung about about 30 degrees from horizontal, that's too flat unless you are working with a very shallow kettle?
2, 3, 4. You have some dross in suspension in your zinc. This grittiness looks like a dross laden bath. Do you have a good drossing practice? How often, how thorough?
5. Looks like poor skimming. Could be too much on the jig, or too few people at the kettle skimming, or poor technique.
6, 7. Poor angle, dross, skimming
8. Poor finish dues to all of the above. How did the sticker get there after galvanizing? Is it a mark that some one in your galvanizing plant thought the quality was good?
It's not surprising that your customer rejected these items, the finish is very poor, but read my post above about standards again.
You accepted the job from your customer. On what terms? What did you agree before the job started about quality? If you failed to agree anything, then who is to blame? Both you and the customer! Them for not clearly stating their expectation, and you for accepting a job where no-one agreed beforehand what the standard was to be.
We're none of us perfect in this business, but we can all do better than this, its a matter of doing the well accepted things that contribute to good galvanizing.
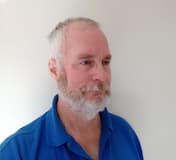
Geoff Crowley, galvanizing consultant
Crithwood Ltd.

Bathgate, Scotland, UK
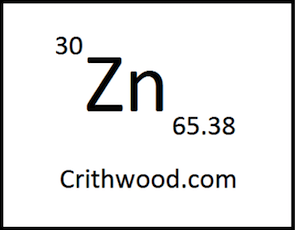
A. The galvanized product may suffer from: "Monday morning floating dross." Or perhaps the kettle is very full of dross from too hot and unsettled dross and trying to use a clam to take out the dross. The kettle should be "mapped" to determine how much dross is on the bottom and where the dross is.
Another possibility is "bad" flux-- meaning impurities like NaCl, KCl, MnCl2, MgCl2, and CaCl2 from "hard" water or just contaminated new flux which is common in India. Bad flux gives excessive skims. Flux formulation is likely wrong.
Regards,
Galvanizing Consultant - Hot Springs, South Dakota
Q. Hi all, I learned a lot from this forum already. I have this one project recently and need some additional help. White corrosion products are observed on the galvanized steel piles within a month, some minor and some more severe. The surface looks uneven, and some spots are not coated or the coating peeled off. My assessment is the storage condition may have contributed to the white storage stains, but I am afraid the quality of the galvanization may also play a role based on the issues I mentioned. I am not sure how to prove or disprove my feeling of the galvanization quality though. Any insight is appreciated.
- Baltimore, Maryland
October 2, 2020
A. Even the storage doesn't excuse this galvanizing. (and I admit that as a galvanizer!)
I see rough coating, some included dross, lack of proper fettling, spikes (sharp frozen part drips like stalactites), flux adhesions, chromate staining. These are all in the care (or lack of) from the galvanizer.
Also I see ... mud, chipping, white rust, and some damage. These are likely to have been caused in handling, and it's anyone's guess when that happened.
White rust is avoidable for a few weeks by chromate treatment. The yellow internal staining suggests that this was done -- it stained it yellow -- but this doesn't give eternal protection! This steel has been outdoors a while (see how red the rust stain on the chipped bit is, that would have still had a little zinc left, so looks to have been outdoors, or in a severe environment for many weeks) and quite likely the passivation has worn off and now white rust is forming. Store it either - dry (indoors) or where no two pieces can touch each other - to minimise this longer term.
In my opinion, you have good reason to talk again to the galvanizer, though perhaps it should have been done much earlier. This galvanizing doesn't meet (for example) ISO 1461. What standard did you ask for? If you didn't ask for any standard, that's what you got!
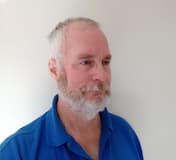
Geoff Crowley, galvanizing consultant
Crithwood Ltd.

Bathgate, Scotland, UK
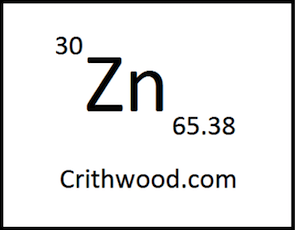
Q. I've got two products, one we supply and one our competitor supplies. The galvanizing on the competitor's product looks quite smoother than the ones we have and we are not able to figure out the reason for such difference.
- Melbourne Victoria
February 22, 2021
A. Hi Kripa. It's not clear to me whether you operate the galvanizing line or you buy the galvanizing service from galvanizing shops? And are you saying that this rusty item is brand new?
Luck & Regards,
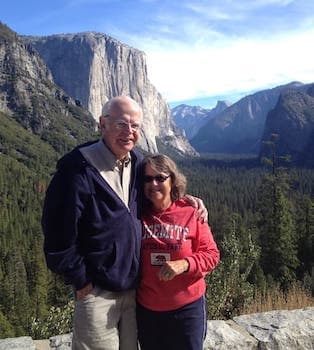
Ted Mooney, P.E. RET
Striving to live Aloha
finishing.com - Pine Beach, New Jersey
A. They look like trailer axle bearing caps?
There are several possible causes in the different appearance.
Steel chemistry has perhaps the biggest influence on surface finish. Check the %Si in the steel between the two if you have the means to do so. (The pimpling effect suggests this)
Next is flux chemistry. Flux in poor condition leaves rough galvanizing like this. (The colour differences suggest this.) Look at, for example, the ratio of ammonium chloride to zinc chloride, the total concentration, the %Fe, and residual other dissolved elements in the flux such as K, Na, Mg. (which should all be low).
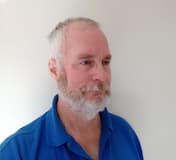
Geoff Crowley, galvanizing consultant
Crithwood Ltd.

Bathgate, Scotland, UK
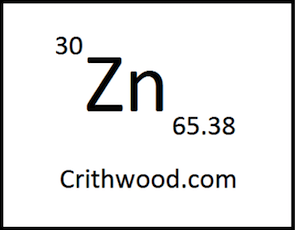
Q. Hi everyone,
We are an assembly factory in Turkey and we have lots of galvanizing parts to assemble. Our suppliers say below mistake or accumulations are normal for galvanizing process according to the EN 1461. The supplier reported us that if they repair the areas mechanically, the corrosion protection would be damaged and the products would be rusted.
But we have difficulties and HSE issues about that. Please give me advice?
Employee - Istanbul
October 15, 2021
? Hi. If you have photos or details, attach them to e-mail to mooney@finishing.com for posting here. We have no information from you yet which anyone could use to offer you an opinion on the acceptability of the parts.
I don't know what you mean by "HSE issues". Health & Safety issues? Please explain.
Luck & Regards,
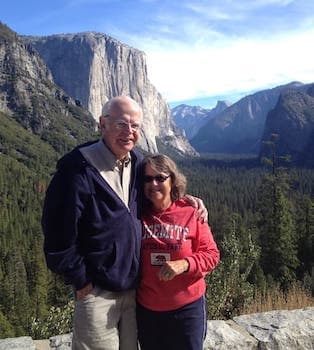
Ted Mooney, P.E. RET
Striving to live Aloha
finishing.com - Pine Beach, New Jersey
Q, A, or Comment on THIS thread -or- Start a NEW Thread