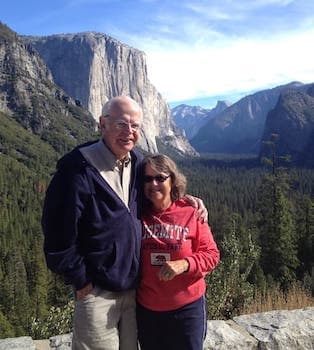
Curated with aloha by
Ted Mooney, P.E. RET
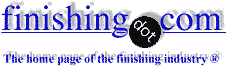
The authoritative public forum
for Metal Finishing 1989-2025
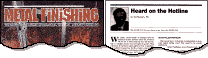
-----
De-wetting of Ni and Sn plating on electronic components
I am plating Sn, 150 microinches, over Ni, 100 microinches over a cured Ag paste, 0.001", on electronic components in a rotary flow through plater, RFT. I am experiencing a chronic de-wet problem. We use Solderon pure Sn over sulfamate Ni with no additives. We use Ti baskets with Sn balls and Ni s-rounds. All rinsing is done with DI water. I am looking for a theory that would explain why changing out the Ni bath resolves the de-wet problem even though hull cells and analyticals look good on the bath. I recently discovered that we lost some anode area and I am wondering if the increased anode current density, almost 25%, is slowly killing the chemistry. Let me explain how. The RFT uses the same cell for plating Ni and Sn and also for rinsing. The anode is lowered into the cell and chemistry is pumped through the anode. The cell fills and overflows with chemistry so the solution level is constant with respect to the anode. We recently changed the cell design and inadvertently reduced the height of the cell which in turn reduced the amount of anode submerged in solution. While one inch seems insignificant, the anode was only submersed about 4.5" before the change. The manufacturer tells me that the back pressure from the bag fills the entire anode with solution so we theoretically did not change the anode current density.
The baths are 25 gallons and they will last between 3 and 7 days after we replace the chemistry before we have de-wet again. If I am degrading or contaminating the chemistry how can I detect it? Anyone having similar problems? Any quality issues with Ni after the INCO strike? Will increased anode current density do this? Based on what I described above does it sound like I did in fact increase the anode current density? Here are a couple of things that muddy this up a little. We have four barrel plating lines with the same chemistry, DI water, and anodes and we do not have the failure on these lines. We have split groups between the RFT and the barrel line and will see de-wet at the RFT and good parts at the barrel line. We have one RFT that has lower anode current density as a result of its design. This machine has consistently produced better parts. We moved the chemistry from it to an RFT that had de-wet and the de-wet went away. We moved the chemistry from the RFT producing de-wet to the other and the de-wet eventually appeared, although it was not immediate and the first few batches looked good. After about 1.5 days of production we had de-wet on our once indestructible machine. Any insight or help would be appreciated.
Rich Reifenheiser- Monterrey, Mexico
2000
Hey Rich,
Yes, the sulfamate ion can break-down and increase the amount of sulfur that is in the plate. High anode current density is chiefly to blame. (This is a good thing in Electroforming.) More anode area would help and keep the temp low (120 degrees F)to prevent ammonia ⇦ this on eBay or Amazon [affil links] formation. Dummy plating also controls the tramp metals that can cause solder problems. At 100 microinches stress should be no problem, so why sulfamate over sulphate? sulphate has no break-down problems.
Regards, Fred
Fred Mueller, CEFWendt Dunnington - Royersford, Pennsylvania
2000
Q, A, or Comment on THIS thread -or- Start a NEW Thread