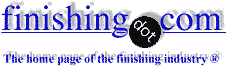
-----
Cracks when Grinding hard chromium plating
by George Dubpernell"
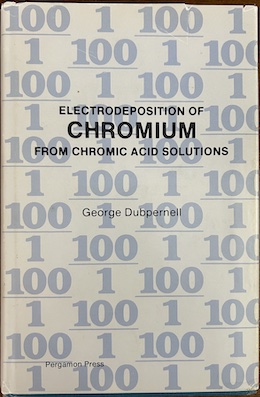
on eBay or Amazon
or AbeBooks
(affil link)
Q. I am searching for information about machine grinding hard chrome. How many number of revolution/minute and how much shall I grind/minute. I like also know which type of grindstone is best?
Regards,
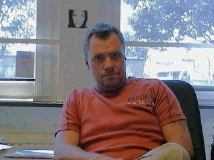
Anders Sundman
4th Generation Surface Engineering
Consultant - Arvika,
Sweden
2000
A. Dear Anders,
The most important thing about grinding hard chrome is not to develop any heat.
Use a grinding wheel with an open structure to make good cooling possible. Keep your grinding wheel sharp by dressing it more often than you normally would do.
The grinding speed should preferably be about 35 mtrs/sec.
Consequently, the number of r.p.m. depends on the diameter of the grinding wheel.
We have more detailed information on this subject available.
Kind regards,
Roel Jaarsma- Netherlands
At what temperature does "Mud-flat" cracking occur?
Q. Re: hard chrome plating/grinding: We get "rejected" parts from our grinding shop that must be stripped and re-plated due to "cracked chrome." We have read that when the base metal gets too hot during grinding, the chrome can crack and look like a dried up lake bed - which is referred to as mud-flat cracking.
Our question is - at what temperature this occurs? What is the "danger range" for how hot the basis metal needs to get for this to occur? Typical basis metals are high strength steels and stainless steels.
Nick Corteseairline - Atlanta, Georgia USA
2000
A. Not that simple. It is the tiny area under the grinding wheel where the chrome reaches a high temperature and then immediately cools off as soon as the wheel moves.
Causes:
- The grinders are taking too deep a cut per pass
- They are using the wrong resin in the wheel
- They are using the wrong grit size
- They are using too high a RPM for the size of the wheel or are using too slow a part speed.
- Or all of the above.
My experience is reason one and two, 99% of the time.
The machine shop gets paid for getting the parts out and they rush grinding. The fact that it recycles is the platers union problem, not the machinist union.
There is about 1 in a thousand chip cutter that will listen to a plater, even when presented articles stating fact. After all, machinists are highly talented and trained people. If you do not think so, just ask one.
Been there and done that. Talk with straight tongue. Every time we had a problem, I would check the grinders and sure enough, they forgot to order wheels and were using unsuitable substitutes. They also thought that a 0.005 grinding cut was fine, because it "worked" (for about 100 revolutions).
James Watts- Navarre, Florida
A. Excellent reply Mr. Watts! You've hit the nail squarely on the head. Improper grinding costs this country billions of dollars a year in excess tool wear and component failure, but woe to the engineer who tells the grinder operator that there is a problem.
A little additional information: I have personally measured temperature under a grinding wheel of up to 1200 °F, and suspect that my temperature measurements are low. These high temperatures can cause the metal to expand so much that it plastically deforms because it kept from expanding by the cool metal around it. Then when it cools, it tries to contract but cannot, and a tensile residual stress is the result. Since chrome is more brittle than most steels, it stands to reason that the chrome will crack long before the steel.
In the aircraft industry, great effort is often made to achieve low stress grinding. I know of one company that will deeply investigate for heat damage if they see a spark while grinding. Yes, that is "A" spark.
It might be worth your time to investigate CBN [cubic boron nitride] wheels in addition to taking Mr. Watts advice to heart very seriously. Good Luck
Frederick Diekman- Streamwood, Illinois, USA
A. Mr. Diekman,
You mentioned CBN wheels and it just rings the bell with me. We have had a very positive experience grinding Molybdenum plasma-sprayed component by a vitrified CBN wheel. We used to apply a set of two wheel for this operation - an electroplated one to remove the bulk of the material and alumina wheels for finishing. We have been able to replace them both by a single vitrified CBN wheel with induced porosity. It grinds very cool and puts mush less stress on the component. It does not inflict metal burns, that were common before.
Gennady Gurinovichabrasive wheel supplier - St. Peterburg
Multiple threads merged: please forgive chronology errors and repetition 🙂
Q. I'm working in a plating department of a helicopter rework company as a technician. Over past few years we have frequent problem with chrome cracking-flaking, some refer this as "mud-flat" cracking. This occurs during grinding on .002"-.005" to base material which is mainly inconel 718 but not always (happened on steel also). Parts are being stripped and replated. All chemicals, cleaners are on optimum level, rinse water ionized and clean, parts vapor degreased. After plating chrome looks good, no visible cracks or any marks not even after NDT. If somebody could enlighten us with any info or suggestion would be greatly appreciated.
Miro StankovicElectroplating technician - New Westminster, British Columbia, Canada
2004
A. In my experience the mud cracking is due to poor adhesion, If the grinder has a incorrect wheel or is taking to much off on his grinding passes, you can get mud cracking but there is often a discoloration along with the mud cracking.
Chris Snyderplater - Charlotte, North Carolina
A. Hard Chrome is under very high tensile stress for almost all plating conditions and chemistries and has less than 1% elongation. This is responsible for the tendency to alleviate by either cracking or spalling. The grinding adds more stresses through cutting forces and heat. Some substrates also differ too much from chrome in thermal expansion coefficient, which adds another factor.
Guillermo MarrufoMonterrey, NL, Mexico
A. I had many a war over this subject. The problem is in the machine shop management. The machinists are doing one or more things wrong.
1. The wrong wheel. I cannot count the times that they ran out of the correct wheel and put on a wrong type, and then bitched like mad because the plating failed. There is an optimum grit material, grit size and binder to be used!
2. The wrong feed or speed, Faster is not better!
3. Too deep a cut. They would literally crush the surface of the wheel and the plating by trying to take a 0.002" cut.
4. Inadequate or the wrong cutting fluid.
5. Not dressing the wheel often enough.
Besides, everyone knows that if plating fails, it has to be the platers fault. It certainly could not be an engineering, or management problem! If you do not believe that, just ask them. (just like it was the platers fault when the part had chrome on it, but was 0.020 smaller than it started out)
James Watts- Navarre, Florida
I loved the parenthetical comment, James; you created an entire colorful scene for me in 25 words or less.
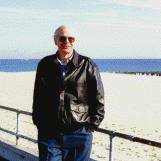
Ted Mooney, P.E.
Striving to live Aloha
finishing.com - Pine Beach, New Jersey
A. Miro,
Read thread 12398, "Hard Chromium Plating of Nickel-Based Alloys" and 25160 "Hard nickel won't adhere to Inconel" about plating on Inconel 718. Be very careful when starting grinding on the high current density areas on the part.
Regards,
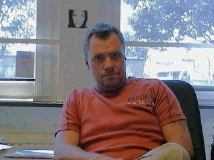
Anders Sundman
4th Generation Surface Engineering
Consultant - Arvika,
Sweden
A. I have to agree with all of the responses. Working in the plating field for close to thirty years, especially in hard chrome, I have yet to see any of the Machinist Foreman that I have to deal with, say it was their fault. I was even told by the Director of Operations, that I didn't know what I was doing, must of been absent during that course. Slow is better, and use a lot of coolant, best of luck.
Charles H. Collins- Watervliet, New York
2004
A. What activation process are you using for Inconel? Are you going in the bath live? What amps per square inch are you plating at? How much grind stock are you putting on part? How much chrome are you putting on per hour?
Greg Mcvay- Peoria Arizona United States
March 19, 2011
Q. I'm getting cracks on some of my batch of hard chromed steel shafts. The shafts are machined and stress relieved then chrome plated to DEF-STAN 03-14 and finished with a final grind. The cracking does not appear to be raising the surface profile but ruins the sealing capabilities of the sliding seals in the mating part. The base metal is S144 stainless steel and the diameter is approx. 8 mm.
Can anyone suggest a cause?
Best Regards,
Chris Elliott- Redditch, U.K.
2005
A. Hi Chris,
Have you measured the hardness on the part before the grinding?
How is your stress relive is that by baking in a oven or shoot peening? Or is it together in the same operation? (remember that it is different temperature in same operation or not).
How is the trivalent chrome content in your chrome solution.
How deep gets the grinding wheel for every cut? (remember when starting grinding that most take carefully not more than .0002 per cut.
Regards,
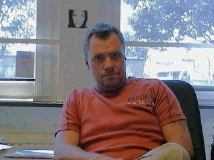
Anders Sundman
4th Generation Surface Engineering
Consultant - Arvika,
Sweden
Q. Those are all good questions. Unfortunately the part is made by a subcontractor who swears they are doing everything by the book.
I haven't measured the hardness. I understand that the hardness of the underlying steel can affect the de-embrittlement heat treat but I'm not sure what process indicator measuring the chrome would give.
The stress relief is by heat treatment as dictated DEF STAN 03-14.
I don't know the trivalent chrome content. I expect that to be kept within tolerance by the plating sub-contractor.
The depth of cut is set by the machining sub-contractor. There has been heavy 'blueing' of the visible steel on these parts so I suspect the final grind operation has to little coolant or is too brutal.
- Redditch, U.K.
A. I think you've answered your own question -- inappropriate grinding procedure.
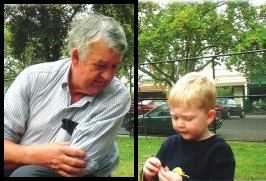
Bill Reynolds [deceased]
consultant metallurgist - Ballarat, Victoria, Australia
We sadly relate the news that Bill passed away on Jan. 29, 2010.
A. Chris,
I think you have your answer there by the grinding.
Regards,
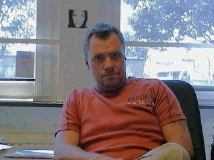
Anders Sundman
4th Generation Surface Engineering
Consultant - Arvika,
Sweden
Multiple threads merged: please forgive chronology errors and repetition 🙂
Q. Unlike the rest of you readers, I am a machinist who is having problems with chrome plating on aircraft parts. I have only been grinding these parts for about 10 weeks now. I have had no problem grinding .0005 per side or (.001 on diameter) at an RPM of 43 on a 4 inch diameter part. No cracking at all for 30 parts. Now all of a sudden the past 6 parts have all cracked on the surface. Using the same wheel the same dressing the same feed rates, etc. etc. Now what would cause this to happen? My plating engineer keeps saying I'm taking to much material per side. But this has worked just fine in the past... Any Answers?
Dan Smithaircraft repair - Arizona
2005
A. The chrome plating could have become more stressed, but that is not likely unless the plater made a huge change in parameters, really huge change.
Cracking in chrome during grinding is normally-virtually always- caused by the wrong wheel or the grinder taking off too much at a pass. 0.0005 is about the max that you should take on a pass. You might also look at the coolant. Did it change in any way-point of application or flow rate or?
- Navarre, Florida
A. Dan,
Ask the plating engineering how hard is the material. I suppose the hardness in the material is 40-55 HRC. Have the part shoots peening before chrome plating, heat treatments before chrome plating, the sulphate content's in the chrome solution. Many thing can gets cracks in a hard chrome layer in a grinding operation.
Regards,
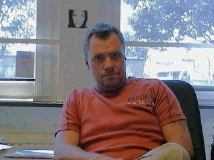
Anders Sundman
4th Generation Surface Engineering
Consultant - Arvika,
Sweden
Q. We are having issues with "High Background" in FPI after chrome grind. We have attempted numerous fixes that have not yielded the elimination of the problem. It is not necessarily a rejectable condition however it keeps the inspectors from inspecting for real defects.
Has anyone seen this and what was done to eliminate it?
Thanks,
- Cleveland, Ohio
2005
Q. I want to know some more about grinding hard chrome.
greg Alexander- six mile, South Carolina
June 16, 2008
A. Chromium is a very good conductor of heat and therefore it is possible to create grinding burns, Tempered or untempered Martensite (white layer) creates cracks in base material and also in the chromium layer.
Regards,
Jos
- Helmond, Noord Brabant, Netherlands
October 28, 2011
A. We use I to K grade wheels with 45 to 60 grit, and grind 0.0002" max cut per pass, and only feed on at one end usually at tail stock. We also dress at 0.001" above final size and have [ed. note: maybe "don't have"?] any problems with etch inspection.
Phill Morrislanding gears - Bolton, England
June 10, 2013
Q. Anybody consider it can be done by benchwork? Polishing using additive (Autosol) can cause peel off too?
Endro Endro- Bandung, Indonesia
December 14, 2012
Does BAC5032 allow 0.003" grinding depth per pass, or what does it mean?
Q. Dear All,
I have a question in regards to standard BAC5032.
"The grinding wheel shall be dressed frequently with a finish dress when the part surface is a maximum of 0.003 inch from the finish dimension."
Does this mean a maximum grinding depth of 0.003" per pass? Any insight would be greatly appreciated.
Thanks.
Landing Gears - Xiamen, Fujian, China
August 6, 2013
A. You absolutely cannot take 0.003 per pass on chrome, especially on aircraft parts.
What it is telling you is that when the grind dimension is within 0.003 of the final dimension that you must dress the wheel.
The correct grit and resin of the wheel makes a major difference in the finish. The wrong wheel and too aggressive grinding is begging for failed plating and it is not the plater's fault.
- Navarre, Florida
A. I haven't read the Specification, and the context of that paragraph could shed more light, but to my understanding it does not imply any specific amount of material removal but to treat the last 3 mils gently. Good luck,
Guillermo MarrufoMonterrey, NL, Mexico
A. Hi Tiger,
I am not going to second-guess Boeing's meaning, you need to talk to your Boeing technical representative to get a technical decision on interpretation.
Aerospace - Yeovil, Somerset, UK
Thank you all for your response.
Landing Gear - Xiamen, Fujian, China
August 12, 2013
A. The spec is saying that the wheel must be dressed .003" max above finished size. My company grinds chromed landing gear pistons and we dress .001" max above finished size, and we use .0002" max per cut.
Phill Morrislanding gear manufacturer - Runcorn England
August 28, 2013
Q. Hi, I'm new on this site but I got good references about it.
I am running a hard chrome process at a workshop and I have been having good results inside my working area; I mean we have to check every product we pass through the process with copper sulphate
⇦ on
eBay or
Amazon [affil links] to have an idea of the chrome layer we made over the product.
But we have the inconvenience that our clients are checking the product as well with the same substance (copper sulphate) when it arrives at their business. Sometimes there are some cracks in the surface of the chromed product. We believe that the molds we are chroming have a lot of pores. And our rectifier is working perfectly; the chrome temp. ranges are from 48 °C to 56 °C
Our chrome and sulphates in our tank are 445.43 and 3.5 (respectively)
We want to know what are the causes of the cracks?
And another question. What is the difference between the flake chrome presentation and the chromium granulate presentation? We have been working a lot better with granulated hard chrome than the flaked chrome.
Thanks for your responses.
- Matamoros, Tamaulipas, Mexico
November 29, 2013
Q. After chrome plating a certain part, there is an on-going issue with a certain area having linear cracks after grinding. What may cause these cracks. On my end, the plating chemistry is excellent, filters are changed frequently, tank de-slugged, etc. The plating appears excellent prior to grinding. The machinist claims to be performing the correct procedures but the issue has been ongoing for a few months now on a particular area. The other three plated surfaces do not crack, which are plated in the same bath. Any suggestions?
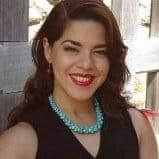
Claudine Meinhardt
Chemist - San Antonio, Texas USA
April 30, 2014
A. What is the parent metal? Hardness? Prebaked. Shot peened?
Plate thickness? Post plate bake cycle??
My cracking problems normally rested with the grinder operator. Their first passes were normally excessive. Feed and speed were sometimes cheated on. Depth of cut after the first pass normally was cheated on. Failure to true the wheel often enough.
The absolute biggest problem was the choice of the disk-grit size and resin. The last year, the failure was always related to using an unsuitable substitute wheel when they could not find the correct one.
Some companies allow a bit of mud flat cracking on certain areas.
- Navarre, Florida
⇦ Tip: Readers want to learn from your situation;
so some readers skip abstract questions.
Q. After hard Chrome plating the part is sent to grinding; after grinding the part is getting unclear. Tell me the reason behind this.
Sharath Gowda- Bangalore India
February 25, 2021
A. Hi cousin Sharath. The grinding process is not being done correctly. Please send good photos to mooney@finishing.com for posting here, describe what parameters are used in grinding, and give us some synonyms for "unclear" so we can understand exactly what the issue is. In the meanwhile, here is a huge amount of helpful info on this thread, and we have at least a dozen long threads on chrome grinding problems & solutions which you can review by searching the site. Good luck!
Regards,
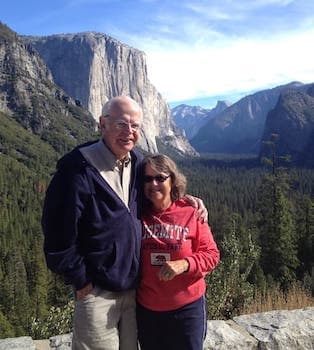
Ted Mooney, P.E. RET
Striving to live Aloha
finishing.com - Pine Beach, New Jersey
A. Hi Sharath,
Your question is not clear; I guess you are not able to finish grind to your required size, so it may be a problem of less/non uniform deposit. As Ted says ... a picture says a thousand words. If you want a clear detailed answer let your question be the same.
Wish you good luck mate..
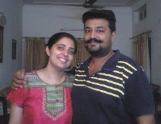
Vikram Dogra
Irusha India - Chandigarh, India
June 5, 2021
Cracks on hard chrome plated spools
Q. Hello,
We are manufacturer of hydraulic valves and valves components. For one of our customer, we produce spools with hard chrome plating. Turning and grinding are made in house, Chrome plating is outsourced.
There are grooves/notches on the spools, and we have crack problems on the sharp edges of grooves. After the plating process, there are few cracks on the edges but after the grinding process there are many cracks.
The chrome thickness is 0,060 mm (60 microns) on point and we remove a layer of 0,030 mm (30 microns) mm thickness during grinding process. As a solution, we make a chamfer 0,10 x45 mm on the sharp edges. The results will be available in next week.
We would be very pleased if you can give us some recommendations about how to get rid of these cracks.
Bulent Ozasciar- Izmir Turkey
May 12, 2021
A. Any parts hardened above 44RC need to be De-Hydrogen Embrittlement done by baking the part to 180 °C, for 4 hours after hard chrome plating.
Also, reduce the cathodic degreasing time by half,
- Belgaum Karnataka INDIA
May 1, 2023
⇦ Tip: Readers want to learn from your situation;
so some readers skip abstract questions.
Q. Anyone grinding hard Chrome with grinding oil vs water miscible?
Tom Cappadona- FREMONT, California
July 14, 2022
⇦ Tip: Readers want to learn from your situation;
so some readers skip abstract questions.
Q. If cracking in the chrome occurs but is not visible by eye, only showing up in NDT as deep cracks, is this caused by machining or by plating?
Paul PrinceShop employee - Florida
January 9, 2023
Q, A, or Comment on THIS thread -or- Start a NEW Thread