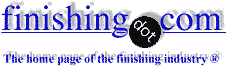
-----
Electro Nickel Plating Process -- or Electroless?
2000
Hi All,
I have a question about nickel plating. We have a nickel plating process using tubs to plate our stainless steel car lighters. In the current process the drum (which contains the lighters) should stay approximately 2.5 hour in the nickel plating tub. I was wondering if there is a new technology out there in which anyone knows that would reduce the time of electro nickel plating. I must add also that we are using the maximum current possible for the weight put in the drums.
Thank you all,
Adel ...
Adel Yahya- West Haven, Connecticut
2000
Hi, Adel. I'm not confident that I'm reading your posting correctly, so --
You are electrolytically nickel plating these lighters and they are in the plating barrel for 2-1/2 hours? That's much too long; you're doing something wrong!
Why do you say you are using the maximum current possible for the weight in the drums? Do you actually mean to say that the rectifier is maxed out, and your barrels are so full that they take 2-1/2 hours to plate with the current you have available?
Switching to electroless nickel (if that's what you meant to say), or substituting some different brand of electrolytic nickel will probably be ineffective until you have achieved better control over what you are trying to do.
You need to know: 1). what thickness of nickel plating you are seeking; 2). the approximate surface area in the barrel; 3). that your rectifier can deliver the required amperage for that size load.
I have this strange feeling (if what I think I am reading is what you are actually trying to say) that years ago your shop decided to try to increase production by putting more parts in the barrel without upsizing the rectifier, which meant that you had to plate a little longer, which meant you had to put more parts in the barrel to keep up with production demands, which meant you had to plate a little longer, which meant you had to put more parts in the barrel ...
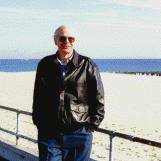
Ted Mooney, P.E.
Striving to live Aloha
finishing.com - Pine Beach, New Jersey
2002
Hello Sir,
I'm an QA manager of a backend semiconductor machine manufacturer. Lately, we encountered E.N. plated base plates surface peeling problem. The E.N. plater claimed that it is due to :
1. High Relative humidity % of our production area.
2. Frequent touch on parts especially "wet palm"
3. Tiny holes on raw materials.
FYI, these base plate are of Aluminium 6061 material, prior plating, they are undergo polishing using superfine sandpaper.
It will be very much appreciated if you advise us the process improvement recommendations.
Best regards,
Roy Loi Peng Lim- Malim Jaya, Malacca, Malaysia
June 6, 2011
E.N. plated base plates surface peeling problem.
whatever E.N. plater claimed is one of reasons but ask them to check degreasing cleaning tank; acid pickling tanks within their specification or to increase their concentration to reduce surface peeling problem.
with regards
bharat
- vizag; a.p; India
Q, A, or Comment on THIS thread -or- Start a NEW Thread