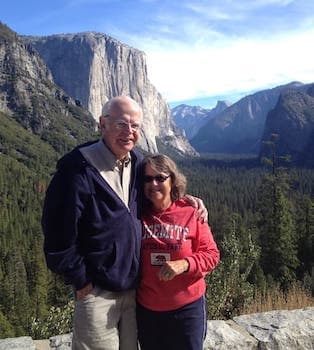
Curated with aloha by
Ted Mooney, P.E. RET
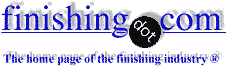
The authoritative public forum
for Metal Finishing 1989-2025
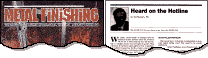
-----
I need salt spray data for MIL-A-8625F for all types
My customer is concerned with airborne contaminants that may reduce the performance of the finish, although he is specifying MIL-A-8625F type II with a powdercoat on top he is still concerned with the performance, especially salt spray. Does anyone have data for this?
My customer is also concerned with the Telecom standard GR-487 which calls out and environment of about 15 airborne contaminants and also concerned with any other contaminants. This application is for the traffic cabinet industry.
I am thinking of suggesting going with type III hard anodize just to eliminate the concern about the performance/wear. Should I specify with or without the seal?
One last question - how soon after applying the anodic coating do you suggest we should be powdercoating? The reason I ask this is that I don't have any source that anodizes and applies powder. I'm wondering if this will be an issue. We can probably ensure they get painted within 48 hours - is this soon enough?
Any comments/suggestions would be very welcome.
Quality Assurance Manager - Anaheim, California, USA
2007
Interesting question and probably too large for posting here to get a full response but here goes. Mil spec MIL-A-8625 requires chromic (Type I) and sulfuric (Type II) SEALED anodic films to pass 336 hours of salt spray performed on a monthly basis as a process control test. Hardcoat on the other hand has no such requirement as it is generally intended for wear applications and is seldom sealed. When it is sealed, it exhibits even far greater corrosion resistance. If you're sold on powder coating following anodize, you should be cautioned that some of the anodize seals, such as nickel acetate and sodium dichromate for example, have a negative impact on paint adhesion. For this reason many aerospace firms require use of dilute seals so that they can subsequently bond them with maximum T-peel strength.
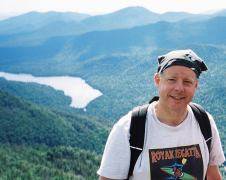
Milt Stevenson, Jr.
Syracuse, New York
2007
Q, A, or Comment on THIS thread -or- Start a NEW Thread