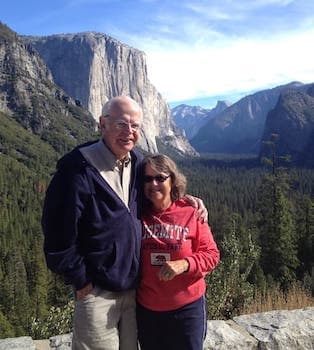
Curated with aloha by
Ted Mooney, P.E. RET
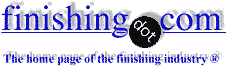
The authoritative public forum
for Metal Finishing 1989-2025
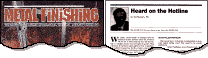
-----
Need a practical way to deburr lens barrel before Hard Anodize
I am having trouble with the surface finish of some lens barrels. They are 6061 T651 and are hardcoated with 8625 Type III with teflon impregnation. Lapping the parts is solving the problem but is not practical for production. Is anyone familiar with typical deburr operations that could help?
Bill MapelMechanical Engineer - Austin, Texas
2007
The burrs are at the ends of the tube and result from cut-off operations? It would seem to me that a typical reaming operation could be practical.
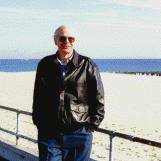
Ted Mooney, P.E.
Striving to live Aloha
finishing.com - Pine Beach, New Jersey
2007
Ted,
We are carefully machining the cells at the ends with small radii to avoid buildup at the corners. The problem I am fighting is on bores of approximately 2 inches. A surface finish of 8 microinch prior to anodize becomes 32 microinch after anodize. I was wondering if anyone tumbled the parts (or some other deburr type operation) post anodizing to improve this type of situation or had a similar situation for which they came up with an acceptable solution.
- Austin, Texas
2007
Information is incomplete to answer. It sounds as if you are talking about a small I.D. which is somewhat difficult to surface finish using mechanical methods. If it is a I.D. problem I suggest you look into some kind of bush system.
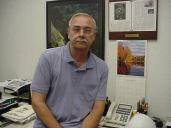
AF Kenton
retired business owner - Hatboro, Pennsylvania
2007
Bill,
If you are starting with 8 micro and ending up with 32 micro, your anodizer needs to consider going to a low etch cleaner. At the end of the bore, consider a tiny increase in the radius that you are using now. Is it a chamfer or a radius?
- Navarre, Florida
2007
I am having trouble with the ID and OD of mating anodized parts of approximately 2 inches in diameter. The ends are broken with .010 to .020 inch radii. Can someone tell me more about the low etch cleaner?
Bill Mapel- Austin, Texas
2007
Bill
I still do not have a good grasp on what your problem is based on what you have told us, but...
If you refer to the mil spec, a radius of .063 is recommended for .002" thick anodic coatings. As the coating builds up perpendicular to the surface, a sharp edge can promote a burr (or edge defect) after anodize. Depending on your source of material, not necessarily alloy or temper, you will get varied results, some much worse than others, particularly if you have a coating thicker than .002".
As far as surface finish after anodize, you should expect to see some degradation in the surface finish, even if the part is not etched. Starting at an 8 microinch finish, you should be able to end up with a 24 finish after .002" thick anodize. Again, material source will affect the end result. Anodize thickness will affect surface finish, with more degradation with thicker coating.
Anodizers typically use an etch as part their cleaning process. The etch will dissolve the aluminum present at the surface. This etching roughens the surface, and the longer a part is etched, the rougher the surface. A reputable anodizer would not etch an 8 finish part very long- just long enough to ensure a clean surface.
Perhaps you could explain your problem in detail.
- Colorado Springs, Colorado
2007
Q, A, or Comment on THIS thread -or- Start a NEW Thread