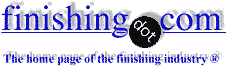
-----
Lamp designer needs to use aluminum/stainless for conductivity
2007
Hello, I am a product designer working on an LED table lamp to be manufactured in mid to high volumes. The lamp design utilizes an aluminum/plastic/aluminum composite panel material. The AL skins are approx. .032" thick and are anodized prior to lamination. We want to use the AL skins as the conductors through the body of the lamp. To complicate this we have pivoting joints where the lamp articulates. At each joint there is a 5/8" diameter hole which is cut after laminating so it exposes the raw edge of the aluminum. This is where we make electrical contact. The contact is made through a stainless steel stamping (lipped washer) which presses into the hole. A wave washer spring pushes against the flange of the stamping. so each joint has one spring with a stainless stamping on either side.
My question is basically about the stainless to aluminum connection and how the conductivity may degrade over time. Can we use a conductive lubricant to protect the raw aluminum? Is there some other coating we can add to the edge of the aluminum hole? is stainless a bad idea? any other thoughts anyone might have would be greatly appreciated.
I understand this question is not exactly a finishing one but it is rather a mechanical/assembly one. I am posting my question here because I have been impressed with the depth of answers and knowledge about these issues I have seen in other posts.
Best Regards,
product designer - San Francsico
I'm not an expert in this area but my first thought is that aluminum itself is not a very good candidate for an electrical moving contact. More so if the other side is made of SS. This will aggravate the potential for galvanic corrosion in presence of humidity or salt (sweat). I wouldn't dare to recommend alternatives.
Guillermo MarrufoMonterrey, NL, Mexico
2007
First of two simultaneous responses -- 2007
Thanks Guillermo for your response.
it may have not been clear in my description of the joint. the aluminum will not move relative to the stainless. the stainless stamping is pressed into the aluminum for the purpose of removing the aluminum from potential wear. so the aluminum to stainless contact is a press fit and is static. the pivoting of the mechanism only moves the stainless stamping against the wave spring. this was originally designed this way because the aluminum would wear too quickly against the hardened spring.
That being the case: if the press fit is tight enough will this protect the aluminum from oxidation? if we press the two components together (essentially a shaft into hole type press fit) will this prevent the aluminum from oxidizing? if stainless is a ad idea what other metal would provide better wear resistance and better conductivity and be compatible with aluminum?
thanks again,
- San Francsico, California, USA
Second of two simultaneous responses --
We burned down many houses during the period the aluminum industry promoted aluminum for home wiring. The stainless to bare aluminum will work a few days, then as the aluminum oxidizes the contact area will heat up and eventually start a fire. Do not do it.
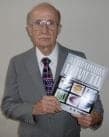
Robert H Probert
Robert H Probert Technical Services

Garner, North Carolina
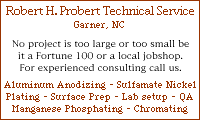
2007
Q, A, or Comment on THIS thread -or- Start a NEW Thread