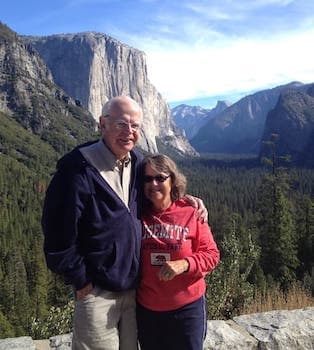
Curated with aloha by
Ted Mooney, P.E. RET
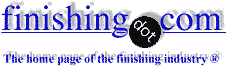
The authoritative public forum
for Metal Finishing 1989-2025
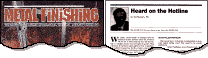
-----
How to eliminate powdery condition of Alodine 1200S
Quickstart:
Aluminum is often 'chromate conversion coated' as a corrosion resistant final finish or as a pretreatment for painting or powder coating. The process actually involves many steps, usually including alkaline cleaning, etching, deox/desmut, the chromate conversion step per se, and water rinses between each step.
MIL-C-5541 / MIL-DTL-5541 / MIL PRF-5541 is the most commonly cited spec. "Alodine" and "Iridite" are trade names. "Chem film" is a slang term for the process.
Q. Hello!
I have chemical conversion coating process with Alodine 1200S.
I want to correct of powdery coating condition on my parts since a month ago (at that time I¡¯ve dumped and recharged my Alodine bath totally).
In my processing, small parts are free from powder and show very beautiful appearance, but unusually, big skins (which is aluminum 2524-T3 Clad, 4.8 by 1.8 m big) show powdery condition.
At this time the pH is 1.44 (1.3~1.8 control) and the concentration is 2.12 oz/gal (1.2~2.8 control).
I want to make sure what kinds of variables are affected to powdery condition and how can I solve this problem.
Thanks in advance.
ENGINEER - BUSAN, KOREA
2007
![]() |
A. Get the 'Technical Process Bulletin' for Alodine® 1200S, available from its manufacturer, Henkel. Your concentration is 2x the usual upper limit. From page 3: - Goleta, California ![]() Rest in peace, Ken. Thank you for your hard work which the finishing world, and we at finishing.com, continue to benefit from. A. Do not know your process, just talk in general: - Singapore A. First be sure you are using a mixed acid deoxidizer on that high copper alloy. ![]() Robert H Probert Robert H Probert Technical Services ![]() Garner, North Carolina ![]() |
Q. Dear Sir,
How come aluminum parts sometimes come out with powder presence when Alodine 1200s is applied (immersion process)? Does it have to do with the immersion duration time?
Regards!
- Chihuahua, Mexico
August 5, 2012
A. Hi Beatriz.
As you can see, a similar question was asked and answered in the past, so we appended your inquiry to that thread. If you have remaining issues after reviewing this, I'd bet that Robert Probert [a finishing.com supporting advertiser] can help. Good luck.
Regards,
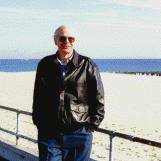
Ted Mooney, P.E.
Striving to live Aloha
finishing.com - Pine Beach, New Jersey
Q. Alodine 1200S is running 1.08 oz/gal. and 1.55 pH and 6061-T6 test panels are coming out a little powdery (parts are looking good). Could it be because of the test panels or is my concentration and pH off?
Clay Cheatham- Magnolia, Arkansas, USA
October 9, 2017
A. Try a new deox in a bucket AND review the calibration of the pH meter, especially at that low pH.
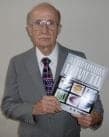
Robert H Probert
Robert H Probert Technical Services

Garner, North Carolina
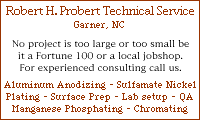
A. Clay
I believe your pH may be the cause. Take a bucket of the Alodine and incrementally bump the pH to see what works. We have found better results at the higher end of the pH limit.
- Green Mountain Falls, Colorado
Troubles with Alodine 1200s
Q. Good Morning!
Summary of Problems: Inconsistent coating, Salt Spray Failure, Powdery Finish, Clear Finish, Finish bouncing back and forth between extremes when troubleshooting or changing parameters.
I have read as many discussions on this topic as I could, tried everything I could, to no avail. Here I am, please bear with me as this will be a long post with many details!
As a history, our company moved into a new facility in February, and switched proprietary brands from Iridite 14-2 to Alodine 1200S at that time, to open doors for Boeing Accreditation on Chemical Conversion coating. I had the Iridite 14-2 dialed in perfectly at the last shop. Perfect Salt Spray results (on 2024-T3), and a stable composition/maintenance schedule.
From day 1 of Alodine, we have experienced issues all over the board.
-10/26/17: Initial Bath makeup of 2.058 oz/Gal (Boeing guidelines recommend 1-3 oz/Gal for Alodine 1200s immersion, Henkel recommends 1.0 oz/Gal for immersion, 2.0 for brush application) (Bath sat unused until January 2018)
Initial Salt Spray results qualified us at a 15 second immersion for Class 3 coatings (electrical conductivity) and a 45 second immersion for Class 1A (maximum corrosion protection).
Coatings were spotty with runs/sagging colors, non-uniform appearance, some alloys powdered or didn't take coating at all, etc... pH fluctuated between 1.4-1.7.
We tried etching, no etching, deox, no deox, short immersions, long immersions, higher temperatures, lower temperatures, high pH, lower pH, etc...
Re-read the technical data sheet and decided to cut the concentration of the bath.
-2/26/2018: Bath Cut to reduce concentration to 1.33 oz/Gal. pH of 1.6, set point of 75 °F.
-3/5/2018: Initial Salt Spray Failure @ 1 minute processing. (pH of 1.8 that day)
We seemed to dial in the visual appearance for a few weeks, though Salt Spray had failed.
Panels and parts looked pretty good for a while, but still issues with inconsistent visual coating. Very spotty, some areas look clear, others are iridescent gold/orange/pink.
Then slowly the coating lost coloration until all parts ran were almost clear (including our Salt Spray panels).
-4/3/2018: Replacement Salt Spray Failure @ 3 minutes processing. pH of 1.5, 1.29 oz/Gal.
-4/3/2018: April Salt Spray panels Failed at the same parameters as the replacement test.
-5/3/2018: Upon receipt of the April failure notification, we immediately dumped the bath and rebuilt @ 1.28oz/Gal. 1.6 pH, and management mandated constant air agitation in the gold chem tank, unless parts were being ran. We proved with our previous proprietary gold chem that that was incredibly detrimental to coatings, but if we didn't agitate at all, we would slowly lose color in the gold chem coatings. We ran tests and narrowed down an air agitation schedule that worked to retain the color of the coating, but did not cause dark powdery coatings. This schedule was Monday, Wednesday, and Friday mornings for 1 hour.
Since management mandated the constant agitation, we have since had dark powdery coatings that wipe off or are removed with tape during the masking process.
(I would also like to note here that we do not wait 24 hours for the gel to cure prior to masking parts)
-5/17/2018: I provided Management with my failure investigations, which discussed Silica contamination in our tank. Between finding silicone plugs in the tank during the rebuild, we have been etching/deoxing a lot of Cast Aluminum parts lately. Testing showed 44 ppm of SiO2 in our Chemfilm bath. (I sent out a sample of the original bath alongside the new bath built on 5/3. New bath tested at 33 ppm of SiO2.) After this information we scheduled an immediate rebuild of the brand new tank...
-5/19/2018: Dump of tank, scrubbed out the tank with dilute NaOH & red abrasive pads, much rinsing, and rebuild.
-5/21/2018: Powdery coatings rubbing off, tape pulling coating off, etc... Waiting on results from SiO2 testing of this new New bath, plus our incoming tap water.
-5/22/2018: The panels ran last night by our swing shift that the coating was 'wiping off' of, and are now set, and will not wipe off.
Our Process:
Alkaline Clean: ~140 °F, ≥ 9.5pH, 17oz/Gal
Spray Rinse (pulled from Immersion Rinse next to it)
Immersion Rinse
Alkaline Etch (used only when required): 4.0 oz/Gal, Pre-penetrant/Boeing regulated parameters. 99 ° F.
Spray Rinse (pulled from Immersion Rinse next to it)
Immersion Rinse
Nitric/Iron based Deoxidizer: <1.0 pH, 50 g/L Fe2SO4 content, 34 g/L Nitric content. Cu content of <0.4 g/L (Usually sits at 0.026 g/L) 80 °F
Spray Rinse (pulled from Immersion Rinse next to it)
Stage 2 Counter flow Immersion Rinse
Stage 1 Counter flow Immersion Rinse
Alodine 1200s: 2-4 minute immersion, 1.6-1.7pH, 1.3 oz/Gal, 80 °F.
Spray Rinse (pulled from immersion next to it)
Ambient Immersion rinse: 3-5 minute immersion
I am about to drop the temperature, raise the pH, stop agitating the tank constantly, and see where that gets us.
Any insight or suggestions on what else I can do would be very much welcome!!
Lab Manager - Arlington, Washington, USA
May 22, 2018
A. 1. Look at the panels with a 10X loop before you process.
2. Review the reliability of your pH measurements, sounds like you are constantly too low - causes wipe off.
3. Be sure the ferric sulphate deox is air agitated to keep it re-oxed back up from ferrous to ferric.
4. Has the soil changed, is it waxy, parafinic, maybe you are not cleaning.
There should be no difference in results Alodine versus Iridite.
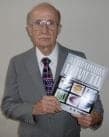
Robert H Probert
Robert H Probert Technical Services

Garner, North Carolina
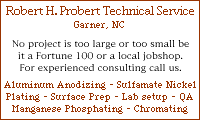
![]() |
Aero Finishing, LLC - Arlington, Washington, USA A. Good Morning Kai Drip Dry-Dab the bottom of the panel-No Compressed Air is used to Dry the Coupon panels. - Lexington, Massachusetts |
A. Good, some progress has been made. If it was good at 60 seconds and bad at 90 seconds, that tells me the pH is still a tad low. Go back and standardize ONLY on the pH 1.02 which is closer to where we want to measure, do not set the 4 and 10. And we need some "moderate" agitation in the tank. Now, regarding the final rinse, it does not have to be squeeky clean and perfect - just dry on a little yellow water and that will enhance the protection.
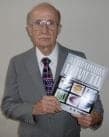
Robert H Probert
Robert H Probert Technical Services

Garner, North Carolina
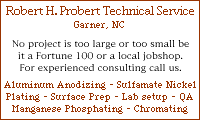
Good Afternoon and Happy Friday!
Mr. Krueger,
Your referenced post is actually the one that helped me discover our Silicate contamination problem!
Mr. Probert,
This morning, our tank read at 1.7 pH with our normal calibration.
I just re-calibrated the meter to a single point, with our 1.07 buffer. Sure enough, our pH now reads at 1.56 . I am issuing a change request to bring it up to an actual 1.8!
I will be changing our tank monitoring process for anything under 2.0 from now on. Thank you!
Yesterday I added an electric filter unit (sans filter) into the bath to provide mild manual circulation into the tank.
You recommended to leave a slight chem residue on the parts to dry (please correct me if I am misunderstanding) to aid in corrosion protection...
Our processors currently spray rinse and then 'soak' the Gold Chem in an ambient temperature immersion rinse for 3-5 minutes immediately post chemfilm. Is this something that will harm our coating? Right after that, parts come off the line and they are blow dried with compressed air nozzles, and stored in our "Dry Room" which is controlled to rise no higher than 120 °F. (My validation panels do not get compressed air, nor are they placed in the heated room. They are air dried in the Lab where I can keep my eye on them.)
I want to thank both of you, and this entire forum, for the help and resources provided. Absolutely invaluable.
Aero Finishing, LLC - Arlington, Washington, USA
A. Just let the final rinse be slightly yellow, and that will not violate many specs and will help enhance the protection. Always standardize the pH meter as close to the level you want to measure. When I do my bi-weekly service in a local NadCap shop, we use 7 for the water and nickel seal, then 4 for the tri-V chromate, then 1.63 for the 14-2 and the type I Chromic Acid Anodizing. I am glad you are making progress.
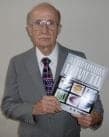
Robert H Probert
Robert H Probert Technical Services

Garner, North Carolina
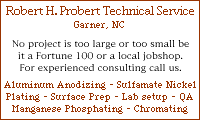
Q. How much pressure should be applied to detect the powdery condition tested in Alodine 1200S (yellow - brown)with 2024 aluminum?
When we run this material 2024, it has some powdery if the cloth is pressed a little bit, other alloys does not show powder even if the cloth is applied "hard" - rubbed to the surface.
Is there an "appropriate" level or specification of pressure to be applied?
Consultant - Mexicali, BC, Mexico
August 17, 2018
Q, A, or Comment on THIS thread -or- Start a NEW Thread