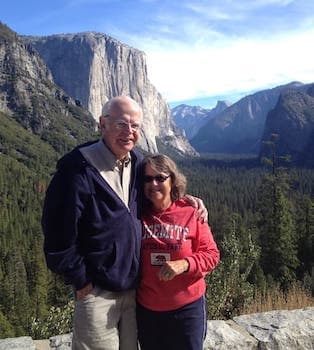
Curated with aloha by
Ted Mooney, P.E. RET
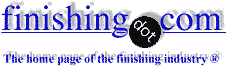
The authoritative public forum
for Metal Finishing 1989-2025
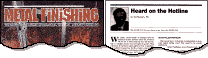
-----
Hot dip galvanizing: what is reasonable dross & ash material loss?

estimados consultores, es la primera vez que hago una pregunta , tengan paciencia
en la planta se procesan solo tuberias, mi escoria esta al rededor de 1.14 y cenizas 3.1
aunque sea de otros tiempos, aclaro no uso fluxado
respecto a las cenizas hay superficial y la de soplado interno de la caƱeria, como considerar la del soplado interno?
les pediria por favor el calculo que estiman para generacion de cenizas por superficie del tubo, muchas gracias
ah la batea es de 7000x500x500 saludos !
gerente planta galvanizado tuberia - buenos aires, argentina
August 19, 2022
![]() |
Hi Andres. Please use translate.google.com or some other service and post in English. Luck & Regards, ![]() Ted Mooney, P.E. RET Striving to live Aloha finishing.com - Pine Beach, New Jersey |
⇩ Related postings, oldest first ⇩
Q. What is the normal ratio of the Zinc ash and bottom dross compared with the consumed Zinc in hot dip galvanization and how can I recover pure Zinc from the ash & dross effectively. I am a manager and producing galvanized wire by hot dip process, and the Zinc lost through dross and ash is really bothering me. So far, I remelted the ash (big sizes) in a crucible and recovered metallic Zinc. I have also used ammonium chloride but not found it very effective. How can I increase the effectiveness? Are there other additives to mix with the ash and dross?
If you could give me some recommendation it will be very appreciated.
- ISTANBUL, TURKEY
2007
Q. I as a Management consultant am validating a project that is being set up to undertake hot dip galvanising works for channels, angles, cable trays, etc.
Tank size 8 * 1 * 1.4 meters
If zinc consumption is 5%, I want to know what are the losses - dross and ash. What is the composition of these losses?
If the tank is in sleep mode, what are the losses?
- Hyderabad, AP, India
2007
A. Consumption of zinc in a galvanizing plant are several:
To the job: The coating will consume perhaps 5% by weight of zinc (weight of item increases by 5%, this increase coming from zinc coating).
To dross: Dross is an alloy of zinc and iron formed free (unattached) in the zinc melt. It sinks by gravity to the bottom. The source of Fe to form dross, including the work, residual chemicals dripping off, and importantly, the kettle walls. The latter means it continues all the time, production or not. This material is a salable commodity. It is removed periodically by mechanical means. It could be 96% Zn by weight.
To ash: Molten Zinc in air will always oxidize and the oxides form on the surface. This happens during production and also at idle time. This is also a salable commodity and removed by skimming off the surface of the molten zinc.
This could be 70% metallic Zn, and much of the rest is Zn Oxide.
In "sleep mode", ash formation is reduced by placing covers on the kettle (also saves heat).
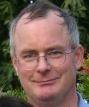
Geoff Crowley
Crithwood Ltd.
Westfield, Scotland, UK
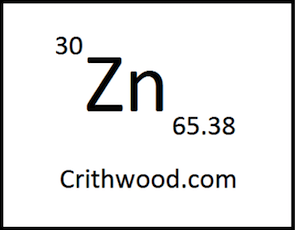
A. Sir:
For "Dry Kettle" galvanizing: Dross above 0.6% of production shows a problem. Dry ash above 0.8% of production (no ash box), above 0.4% of production (manual ash box) or above 0.2% of production (motorized ash box) is not acceptable.
The amount of zinc on the product can easily vary from 2% to 10% depending on the thickness of the steel (surface area) and the reactivity of the steel. Also the technology and skill of the workers is critical. Since you are doing thinner steels which are likely to be reactive (likely under the Sandlin curve), I expect the zinc on the product will be in the range 5% to 8%. You have other problems, which I will refer to later if you continue to ask questions.
Regards,
Galvanizing Consultant - Hot Springs, South Dakota, USA
A. Dear Mr Sachidanandan
Your Consumption 5% is Net or Gross? The process is Dry or Wet?
Refer to the tips given by Dr, Cook: the second point, i.e., "technology & skill" -- if you put you can reduce the consumption by another 1% easily for structural steels.
Please write your actual problem instead of giving overall Zn consumption. The platform is extremely useful for gaining wisdom.
REGARDS,
- BHILAI, Chhattisgarh, INDIA
A Guide to process Selection & Galvanizing Practice"
by M. J. Hornsby
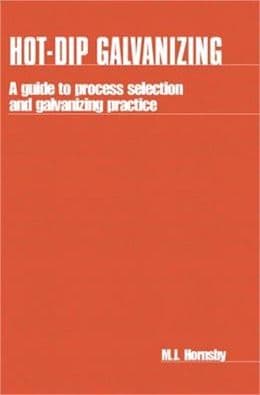
on AbeBooks
or eBay or
Amazon
(affil links)
Q. What should be the ideal Ash & Dross formation in Hot Dip Galvanizing (Manual) of Transmission Tower components For Both Dry & wet galvanizing?
Ramesh PonnathapurPart of galvanizing industry - Mumbai, Maharashtra, India
July 19, 2013
A. Hi Ramesh. As you see, we appended your inquiry to an existing thread which answers it in good detail. If you have additional questions regarding your own particular situation please detail them. Thanks.
Regards,
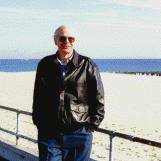
Ted Mooney, P.E.
Striving to live Aloha
finishing.com - Pine Beach, New Jersey
by NACE
[only rarely available]
on AbeBooks
or eBay or
Amazon
(affil links)
Q. Good day Sir,
I have more Ash coming; please advise me how to reduce this loss.
NOTE:
I use caustic soda to neutralize Rinsing; is there any effect?
- Saudi arabia
December 12, 2016
A. Sir:
On the dross side-- Usually dross is 0.4% to 0.6% of production. I am working to lower this. I have evidence that NaCl in the flux causes more dross. Thus your use of NaOH to neutralize acid rinse is not acceptable.
On the ash (dry skims) side I now know ways to reduce this to 0.1% of production and I am currently writing this up.
Galvanizing Consultant - Hot Springs, South Dakota USA
A. Dear,
Ash formation is directly related to what process you have adopted for Galvanizing and quantum of material you Galvanize. And some what it related to Pre-Flux used. To get the right answer explain your process
Galvanizers & Consultants - Delhi, India
Q. Dear Dr. Cook,
Thanks for your reply, but I want to ask why caustic soda ⇦liquid caustic soda in bulk on
Amazon [affil link]
not accepted in neutralization of rinsing where
NaOH + HCl --> H2O + NaCl (ppt)
and what chemicals are used to neutralize Rinsing?
- Saudi arabia
December 20, 2016
A. Hello MR. aly elsokkary,
Neutralize your rinsing with NH4OH instead of NaOH...
You are requested to heat flux and observe the result.
Heated flux will reduce your flux consumption also.
It will reduce your Dross formation also.
- Vadodara, India
Q. Thanks a lot Mr. Rajesh Patel
What is the alternative that can be used instead of Ammonium Chloride in Zinc bath?
- Saudi arabia
March 19, 2017
A. Dear Mr. Aly Elsokkary,
You are requested to mention purpose of Ammonium Chloride in Zinc bath. Are you using WET process or to increase fluidity of zinc?
If you are using DRY process, then you're not required to add Ammonium Chloride in Zinc bath.
Please feel free for further information if required.
Rajesh
- Vadodara, India
What factors influence galvanizing ash production?
Q. Hi everyone. Refer to previous discussion, dross is mainly related to the pretreatment process before the hot dip. What about the ash generated? is it solely on the skimming method. Currently having about 1.3% of ash. Any suggestion to reduce it?
Ken Wong- Selangor, Malaysia
August 26, 2017
A. Dear All.
Ash formation also depends on top open surface of zinc bath.. more surface area open then the Ash formation would be more, also surrounding air circulation of plant cause more Ash formation.
Here in India we are considering maximum 1.0 % which include zinc ash and Zinc Dross (Hard Zinc )
Gunatit Builders

Manjalpur, Vadodara, Gujarat
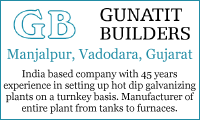
Q. What would be a relationship of dross regarding zinc produced in the hot galvanizing process, I appreciate your comments.
Thank you.
MPI - Juarez, Chih. Mex.
January 26, 2018
A. Sir:
For a dry kettle, a dross production of 0.4% to 0.6% of production is good.
Regards,
Galvanizing Consultant - Hot Springs, South Dakota 57747
Q. I am currently working as an intern, mechanical engineer. I need to calculate the volume of the top dross, estimated 0.5 tonne per 8 hours.For both GI(zinc) and GL(zinc-aluminium) continuous galvanizing plant.To calculate the volume of 0.5 tonne of top dross, I need the density of the final top dross. What formula should I use to get density of top dross for both GI and GL pot? What is the mass fraction of top dross?
Aye Myat- Yangon, Myanmar
January 18, 2019
Q. Requesting reference article /document for Dross produced per ton of galvanized steel
Sir, my questions are:
a) what is percentage of Dross expected or acceptable for one of galvanized steel. (Standard parameter followed: 450 °C Temp., Flux D salt good concentration with 2g/lit iron )
b) what is percentage of Ash expected or acceptable for one of galvanized steel. (Standard parameter followed: 450 °Temp., Flux D salt good concentration with 2g/lit iron )
c) VERY IMPORTANT: Provide official Reference document details where I can verify the answers.
- Surat Gujarat, India
April 12, 2022
A. There isn't enough information in the question to be definitive.
But, you should be able to get ash to 0.2 to 0.5% (defined as weight of ash divided by weight of steel after galvanizing)
And dross: 0.5 to 0.9%.
Where you get to in the range depends on your material type, whether you haver a drier or not, what temp your flux runs at, what ratio of ZnCl2 to NH4Cl, and density of flux solution. You gave %Fe in flux as 2g/l. Aim to get this under 1 g/l, as the more Fe in flux, the more ash.
You ask for some official reference document. I do not think you will find one!
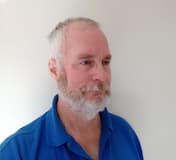
Geoff Crowley, galvanizing consultant
Crithwood Ltd.

Bathgate, Scotland, UK
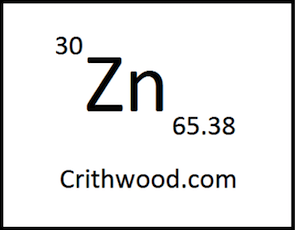
Q. Speaking of that the dross formation is from the reaction between the molten zinc and the loose iron particles in the kettle ... are we getting more dross generated if we have more surface area of products with the same weight?
In general, dross formation is ok with range 0.4-0.6% of zinc used.
If I am dipping 1000 mt of solid shafts which generates about 5 ton of dross, will I get more dross formation if I dip 1000 mt of hollow steel tubes? (i.e. more surface area to come into contact with the reactive molten zinc because we have outer surface and inner surface since it is a hollow tube)
Very appreciated if someone could explain this situation.
- Rawang, Malaysia
July 4, 2022
You asked.. "are we getting more dross generated if we have more surface area of products with the same weight?"
Yes, you will.
There are several ways of expressing dross and ash production. As a % of zinc consumed and as a % of steel weight galvanized. The most common is as % of steel galvanized, weighed after galvanizing.
A reasonable dross production rate is 0.3-0.9% of the weight of steel galvanized. Your figure of 0.4-0.6% of weight of zinc consumed is very high, but possibly you meant as % of steel weight?
Yes, the amount of dross is proportional to the area of steel exposed to the liquid zinc. In many aspects of galvanizing compromises are made, and in such measurements the same applies. Many people relate matters to tonnes, and perhaps should be using m2, but as tonnes are so much easier data to gather they use that. So 1000t of solid will make less dross than 1000t of pipes, as the pipes have more m2.
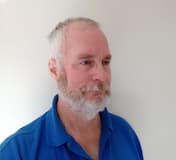
Geoff Crowley, galvanizing consultant
Crithwood Ltd.

Bathgate, Scotland, UK
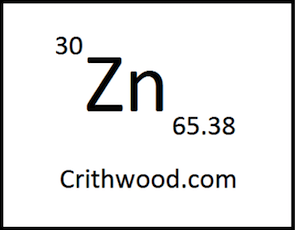
Hi, Mr. Geoff, it was my mistake on the statement. It is actually dross rate at 0.4-0.6% of steel galvanised. So far our rate falls between 0.4-0.6% but in July we have 0.75% of dross removed from the kettle. We drossed with the same method as the month of April and May. After going through the details, found that the quantity in ton of hollow pipes dipped in July is 1.7 times of May and 2.4 times of April. Thus, it brings up the idea of dross formation related more to the area of goods galvanized. As you mentioned, generally people only relate the dross formation to total goods galvanised.
Anyway, Thank you for explaining and clearing my confusion.
- Rawang, Malaysia
July 13, 2022
Q. Hi, we are galvanizing different kinds of items like tower, structure and solar materials. Also we galvanize a variety of thickness ranging from 1 mm to 50 mm in hot dip dry process of batch galvanizing.
My question is are there any ratios to estimate formation of ash, dross with respect to thickness of material (i.e. surface area per MT).
As I know that increase in surface area per Mt will increase both ash and dross generation but how actually the theoretical calculation done, as we getting difficulty in cost calculation for client.
Galvanizng Engineer - Nagpur, India
August 9, 2022
A. Commonly used ratios for dross and ash are weights per weight of steel galvanized.
Ash: expect about 0.2-0.5% (as weight ash/weight steel and as %)
Dross: expect about 0.3-0.9%
The variation spread in these figures shows the typical range that general galvanizers experience. Over these % and you should start looking for problems to solve. Under these ranges, take a pat on the back, you're doing well.
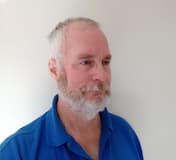
Geoff Crowley, galvanizing consultant
Crithwood Ltd.

Bathgate, Scotland, UK
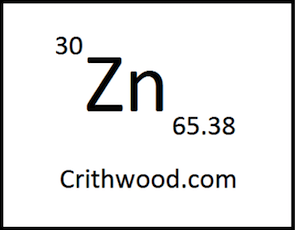
Q, A, or Comment on THIS thread -or- Start a NEW Thread