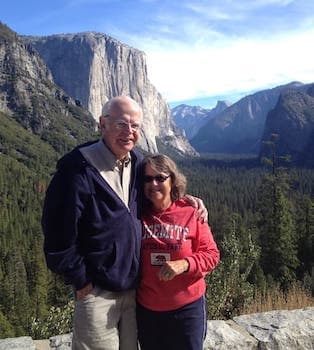
Curated with aloha by
Ted Mooney, P.E. RET
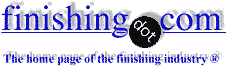
The authoritative public forum
for Metal Finishing 1989-2025
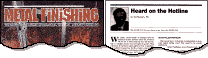
-----
Chemical Conversion Coating Appearance Problem
I have a small commercial chemical conversion coating line processing machined aluminum parts for local machine shops. I typically process 6061, 2024, and 7075 alloys. I often get a blotchy appearance on parts made of 7075 alloy. I have tried increasing cleaning and de-oxidizing times and Iridite bath times, but have made no progress to date. Solution strengths are good. Any suggestions?
Heinz LaufShop owner - Porterfield, Wisconsin
2007
First of two simultaneous responses --
Be sure you use a deoxidizer that is mixed acids. Then consider that the zinc in 7075 "walks" slowly to the grain boundaries and the surface with time, and very fast with heat treatment, and in the case of work hardening there will be more zinc on the surface in the work hardened areas.
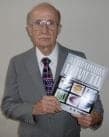
Robert H Probert
Robert H Probert Technical Services

Garner, North Carolina
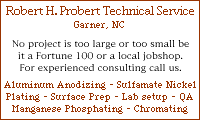
2007
Second of two simultaneous responses -- 2007
Mr. Lauf.
Please check your rinse water following deoxidizing. I've been experienced that overly effective rinsing after deoxidizing aluminum surfaces can adversely affect the surface appearance after conversion coat application. The rinses to get a little
¡°dirtier¡± and ultimately, improve the appearance of the coating.
Don't forget parts are to be processed from one step to the next without allowing the parts to dry.
- BUSAN, KOREA
2007
Mr. Lauf,
I agree with D.Y.Yoo in that extending cleaning and deoxidizing times is not always the best solution to your problem. Sometimes cutting back your times a bit might be the trick (the less chemistry you have touching these pieces the less failure modes you'll have). Also, you should get good color in your Iridite bath within a couple minutes - and start getting problems after more than a few, try cutting those times back a bit too.
The idea is to remove the thin layer of natural oxide on the aluminum without going too deep beyond the surface. Try combinations of shorter cleaner times / longer deox times. Then longer cleaner times
/ shorter deox times. Don't look for a reason, you'll go crazy - just look for what works.
Depending on the volume you have going through these tanks, your
"solution strengths" look good is half the battle, but how are your contaminant levels in your cleaners, deoxidizer, and Iridite?
Good luck to you!
- Seattle, Washington, USA
Q, A, or Comment on THIS thread -or- Start a NEW Thread